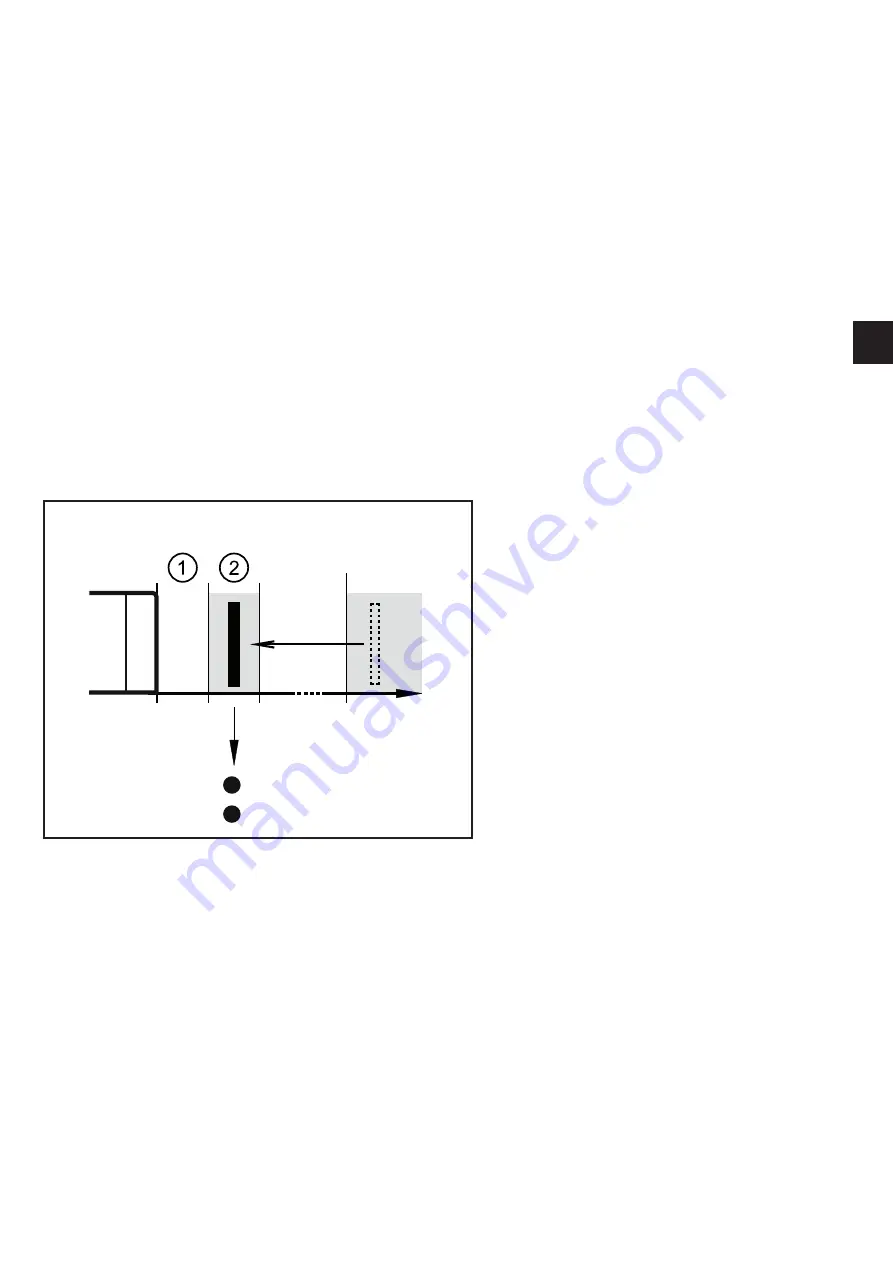
13
UK
9.2 Operating mode
The length of the preceding undamping determines whether the yellow LED
comes on with a delay (→ 9.2.1) or without delay (→ 9.2.2) when a target moves
into the enable zone� In any case, the outputs switch on without delay�
In case of undamping the outputs switch off and the yellow LED goes out without
delay�
In case of damping in the close range the outputs switch off immediately whereas
the yellow LED goes out with a delay of approx� 2 s� When the LED goes out the
outputs are maintained in the safe state ("0")� Thus, switching on again in the en-
able zone is not possible� Enabling is done by undamping (> 30 mm) of more than
2 s or by interrupting the voltage (→ 5.2 Protection against simple defeating)�
9.2.1 Delayed switching of the LED
Undamping > 2 s:
30
0
> 3 s
mm
Signal
Power
If the target was away from the
sensor for more than approx� 2 s
(> 30 mm), the yellow LED goes on
with a delay of approx� 3 s in case of
damping in the enable zone�
This is also the case if the target is in
the enable zone when the voltage is
switched on�
1: close zone
2: enable zone