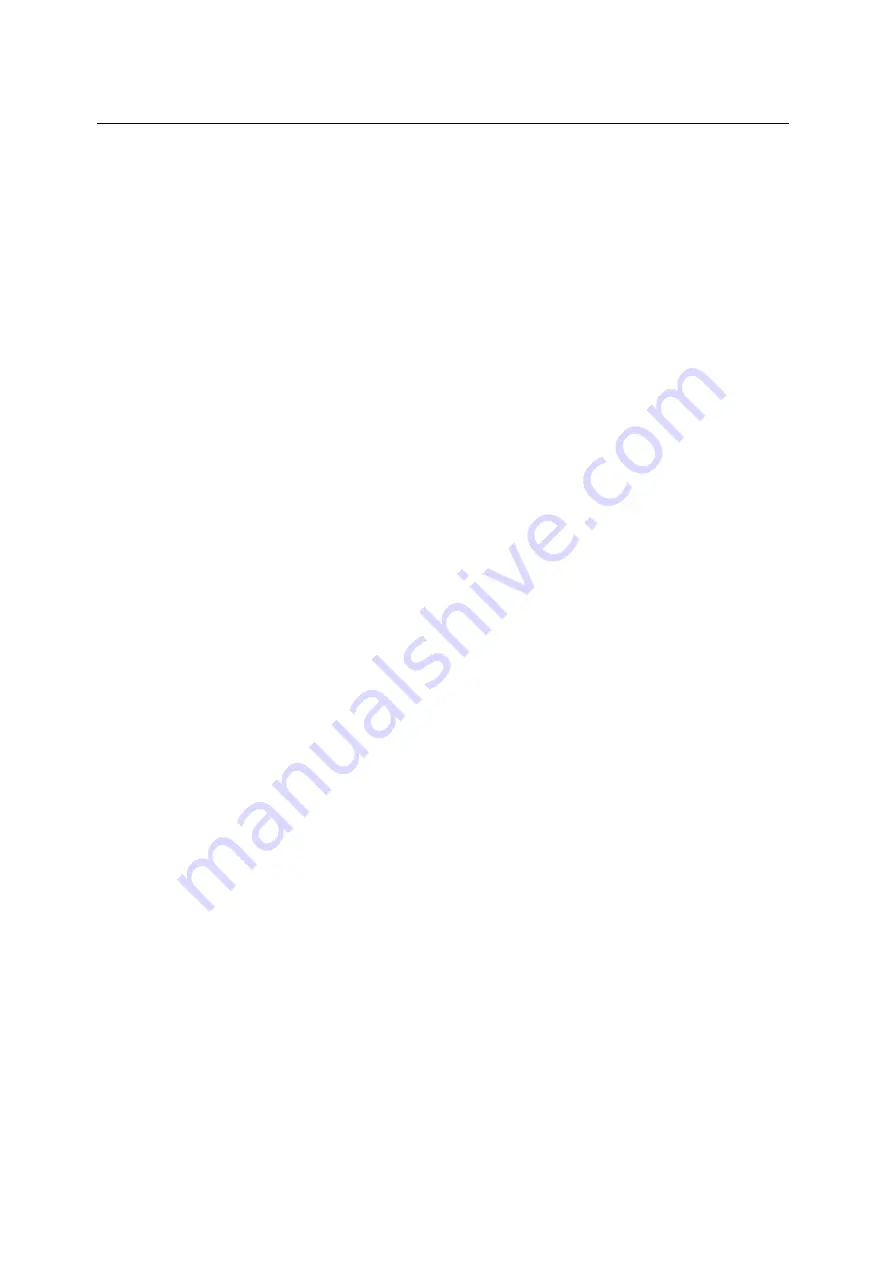
248
ifm
System Manual
ecomat
mobile
SmartController (CR2500, CR2502) V05
More functions in the ecomatmobile controller
Processing analogue input values
10.8
Processing analogue input values
In this chapter we show you functions which allow you to read and process the values of analogue
voltages or currents at the controller input.
Содержание Ecomat 100 ecomatmobile SmartController...
Страница 1: ...System Manual SmartController CR2500 CR2502 CoDeSys V2 3 Target V05 7390667 00 03 2009 ...
Страница 6: ......
Страница 282: ......