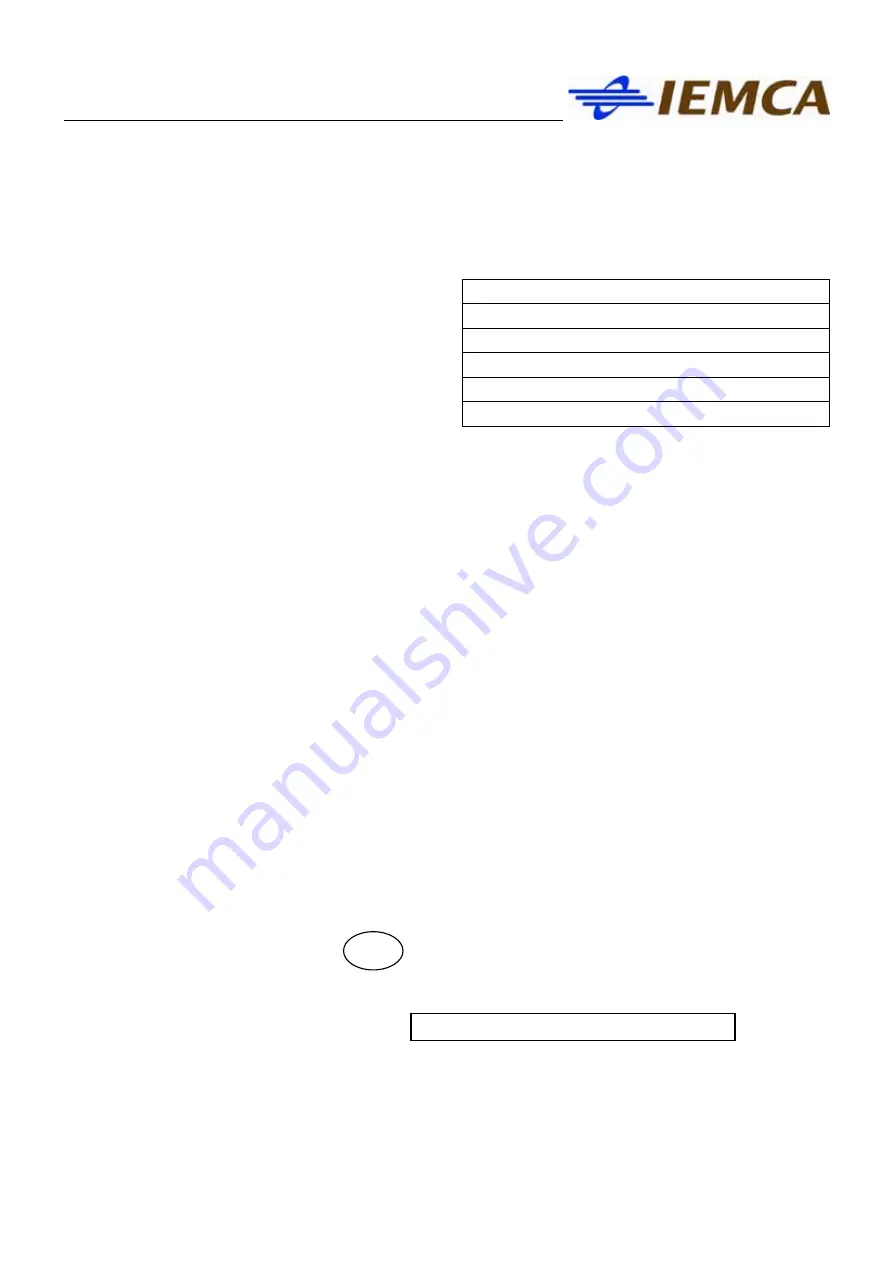
SMART 320 Tp
EN
MANUAL FOR USE AND MAINTENANCE
Rel.
1
Date
21/04/2008
Cod.
401005430
S/N
COMPILER:
Bosi Andrea
ON
APPROVAL:
Ghinassi Andrea
AUTOMATIC BAR FEEDER
ATTACHMENTS LIST
MANUAL FOR USE AND MAINTENANCE
KEYBOARD INSTRUCTION MANUAL
SPARE PARTS BOOK
SCHEMATICS
EC CONFORMITY DECLARATION FOR MACHINE
Содержание Smart 320 Tp
Страница 2: ......
Страница 4: ......
Страница 6: ......
Страница 12: ...EN 1 GENERAL INFORMATION SMART320 1 Pag 6 6 ...
Страница 62: ...EN 4 HANDLING AND INSTALLATION SMART320 4 Pag 26 26 ...
Страница 110: ...EN 7 BAR FEEDER MAINTENANCE SMART320 7 Pag 6 6 ...
Страница 114: ...EN 8 TROUBLES CAUSES SOLUTIONS SMART320 8 Pag 4 4 ...
Страница 120: ...EN 9 PART REPLACEMENT SMART320 9 Pag 6 6 ...