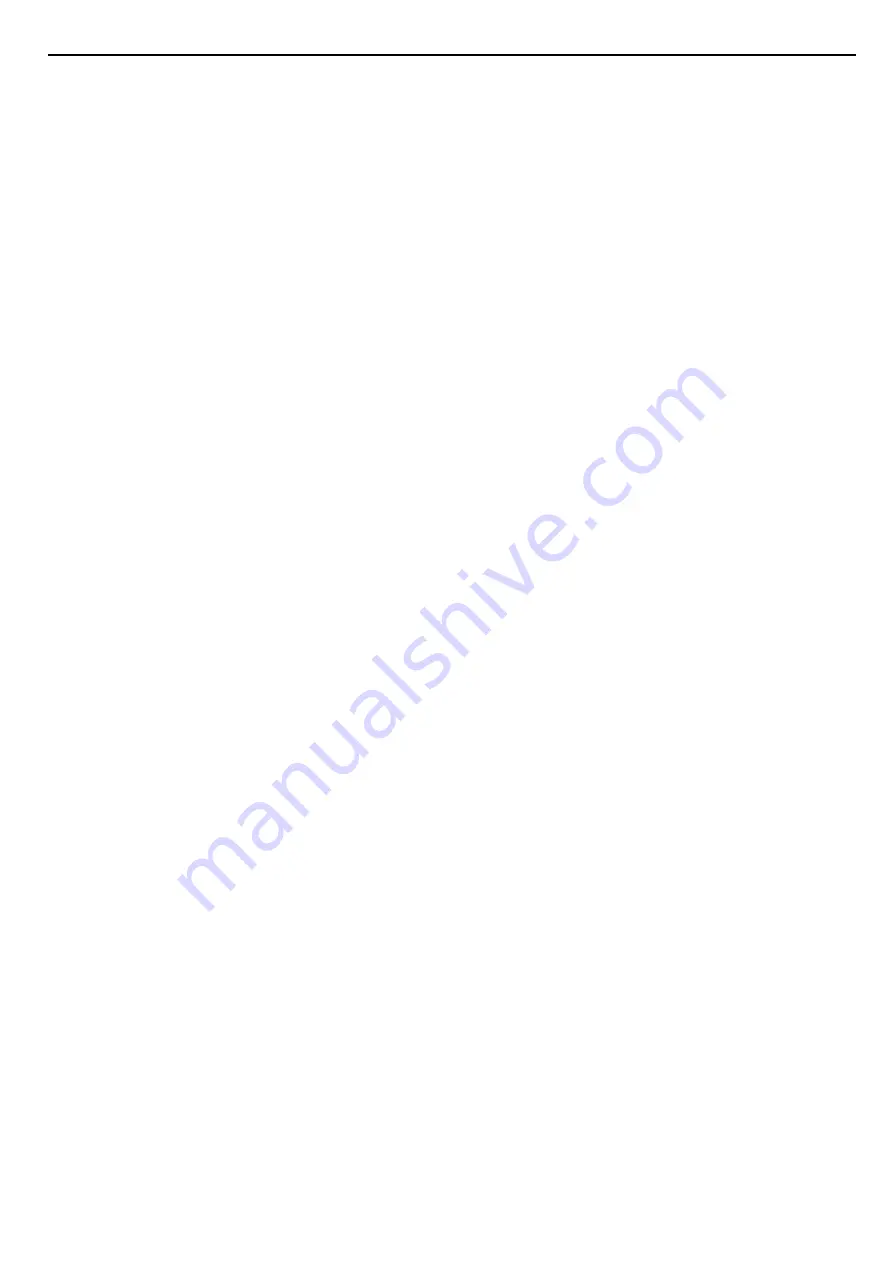
5
SECTION 1 - GENERAL
1 GENERAL
1.1 INTRODUCTION
The
Ideal GB
Series III
range of boilers are wall mounted, full
sequence, automatic spark ignition, low water content, fanned
flue, high efficiency, condensing, combination gas boilers.
Note.
Due to the high efficiency of the boiler a plume of water
vapour will form at the terminal during operation.
Central heating (CH) output is fully modulating with a range of:
24
4.9 to 17.2kW (16720 to 58728 Btu/h)
30
6.1 to 20.4kW (20814 to 69607 Btu/h)
Instantaneous domestic hot water (DHW) output is also fully
modulating with a maximum of :
24
24.2kW (82,570 Btu/h)
30
30.3kW (103,384 Btu/h)
The boiler is supplied fully assembled with DHW plate heat
exchanger, diverter valve, circulating pump, pressure gauge,
safety valve and CH expansion vessel.
Variable CH and DHW temperature controls are fitted on the
user control.
The boiler includes as standard:
-
Automatic bypass
-
Daily pump and diverter valve exercise
-
Mechanical 24hr timer
The boiler casing is of white painted mild steel.
The boiler temperature controls are visible located in the
control panel on the front of the boiler.
The heat exchanger is manufactured from cast aluminium.
The boiler is suitable for connection to fully pumped,
sealed heating systems ONLY. Adequate arrangements for
completely draining the system by provision of drain cocks
MUST be provided in the installation pipework.
Pipework from the boiler is routed downwards.
1.2 OPERATION
With no demand for CH, the boiler fires only when DHW is
drawn off.
When there is a demand for CH, the heating system is
supplied at the selected temperature of between 30
o
C and
80
o
C, until DHW is drawn off. The full output from the boiler is
then directed via the diverter valve to the plate heat exchanger
to supply a nominal DHW draw-off of
24
9.9 l/min at 35
o
C temperature rise.
30
12.4 l/min at 35
o
C temperature rise
The DHW draw off rate specified above is the nominal that
the boiler flow regulator will give. Due to system variations
and seasonal temperature fluctuations DHW flow rates/
temperature rise will vary, requiring adjustment at the draw off
tap.
At low DHW draw-off rate the maximum temperature is limited
to 65
o
C by the modulating gas control.
The boiler features a comprehensive diagnostic system which
gives detailed information on the boiler status when operating,
and performance of key components to aid commissioning
and fault finding.
1.3 SAFE HANDLING
This boiler may require 2 or more operatives to move it to its
installation site, remove it from its packaging base and during
movement into its installation location. Manoeuvring the boiler
may include the use of a sack truck and involve lifting, pushing and
pulling.
Caution should be exercised during these operations.
Operatives should be knowledgeable in handling techniques when
performing these tasks and the following precautions should be
considered:
• Grip the boiler at the base.
• Be physically capable.
• Use personal protective equipment as appropriate, e.g. gloves,
safety footwear.
During all manoeuvres and handling actions, every attempt should
be made to ensure the following unless unavoidable and/or the
weight is light.
• Keep back straight.
• Avoid twisting at the waist.
• Avoid upper body/top heavy bending.
• Always grip with the palm of the hand.
• Use designated hand holds.
• Keep load as close to the body as possible.
• Always use assistance if required.
1.4 OPTIONAL EXTRA KITS
•
Horizontal Flue Terminal (RSF305)
- (900mm long)
•
Horizontal Flue Terminal (RSF303)
- (600mm long)
•
Flue Extension Ducts (RSF341)
- (980mm long)
24-up to 8m (minus any flue kit options)
30-up to 7m (minus any flue kit options)
• Flue Deflector Kit (RSF300)
•
Roof Flue Kit (RSF345)
(min. length 0.950m - max. length 7.5m)
• 90º Elbow Kit (RSF315)
• Flue Vertical Connector (RSF346)