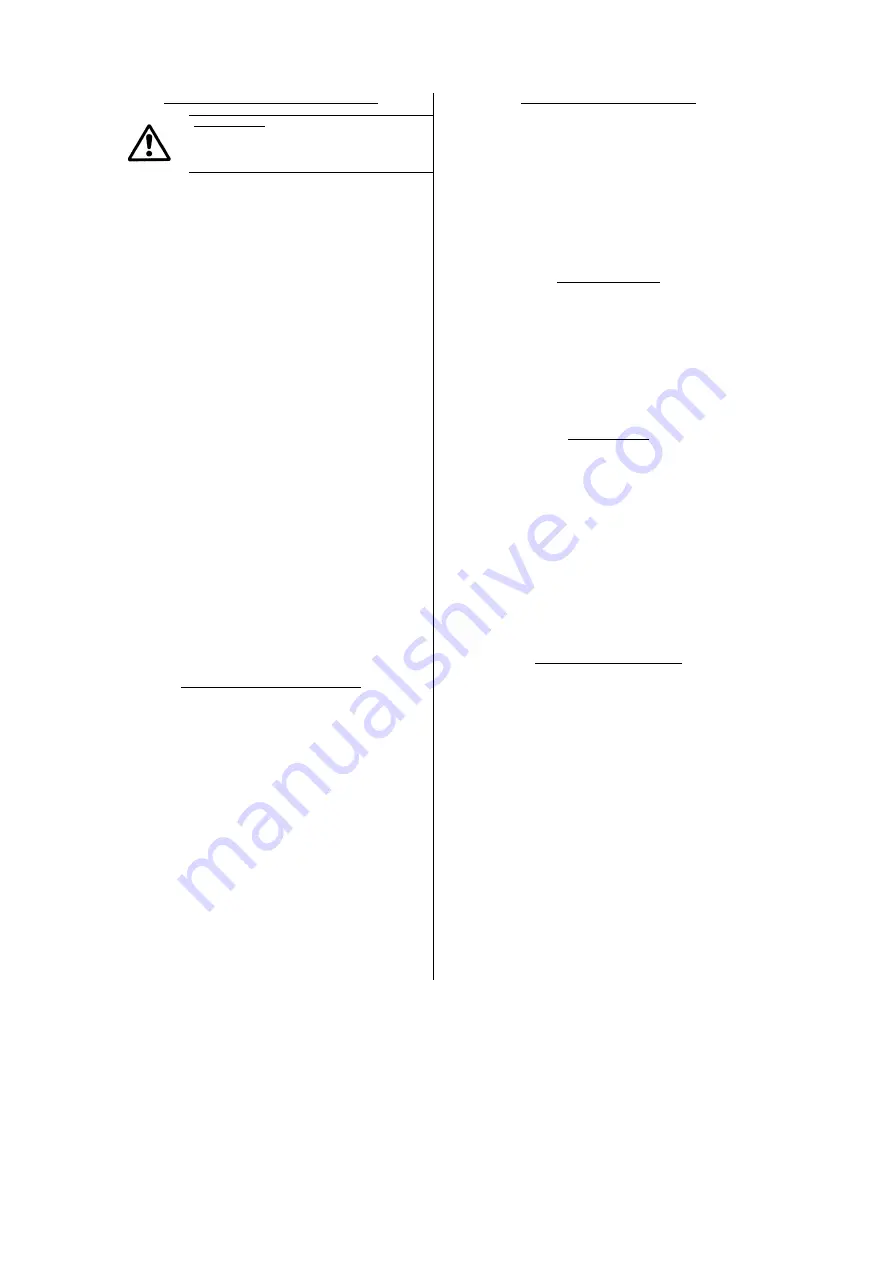
V.00
55
1
– SECURITY AND GENERAL INFORMATION.
1.3. CORRECT USE OF THE MACHINE.
The correct use of the machine involves:
• Not exceeding its working capacity.
• Operating the machine by qualified and trained staff and according to the points
mentioned in the instruccion book.
• Working under the safety systems provided with the machine, checking them
and keeping them.
• Watching the safety measures mentioned in the instruction book and notices on
the machine.
• Wearing clothes which provide personal protection as mentioned in the
instruction book.
• Watching the safety measures which may affect work in the machine and that
can be lawfully expected, as well as those demanded in the workshops.
1.4. PIECE CLAMPING.
Tangential cutting forces and axial forces in the feed direction of the tool are
mainly produced during the drilling process. The tangential forces produce a
moment of forces which make the piece being drilled turn. Therefore, the pieces
to be drilled (or to be machined by one of the operations mentioned above) must
be clamped in an appropiate device such as a drillchuck and the drillchuck must
be correctly clamped to the machine table. For this reason the machine tables are
provided with "T" slots.
The pieces must be clamped conveniently by some clamping device.
The clamping devices in turn must be clamped to the machine table.
The machine table is provided with "T" slots for such purpose.
1.5. TOOL FIXING.
The tools generally used in this machine will have parallel or tapershanks.
Drillholders are normally used to fix to the main spindle of the machine the
parallel shank tools. This fixing device has usually got three jaws, which hold the
tool by the parallel part of the shank. These are used for small drill diametres
(max. up to dia. 16 mm). Bigger diametre drills, usually have taper shank of
morse taper type (the ones of smaller diametres to 16 mm can also have taper
shanks).
The housing in the main spindle to insert the tool is of morse taper type. It is very
important to insert the tool taper correctly in the main spindle taper to avoid the
tool falling from its housing when turning and provoke an accident. The coupling
system itself of the tool male taper in the female taper of the main spindle is auto-
locking, but for it the surfaces of the tool taper and spindle taper must be in
contact. To get the best possible contact, the surfaces of the tool taper as well as
the spindle taper should be in good conditions. Therefore, it is advisable to handle
the tool as well as the main spindle of the machine carefully.
1.6. CHIPS DURING MACHINING.
The machining process removes material from the piece. This material is
released in chips, which can be of different shapes depending on the material
itself. The most commom ones are of three types: fragmented chips in small bits,
short helicoidal chips and long helicoidal chips.
The chips fragmented in small bits can be rejected from the machining area and
can be dangerous if they reach the eyes of the operator. To avoid this, it is
advaisable to wear safety glasses.
The long helicoidal chips tend to roll up the tool and gain considerable volume
before breaking, which is dangerous if they reach the operator as they may
produce injuries. The reached volume may also displace the drill protector from
its security position, increasing the risk of an accident. It is advaisable to use
chipbreaking tools to machine materials which produce such chips. For further
information contact the tool manufacturer.
1.1 - SECURITY
A drilling machine, due to its purpose, is
considered an “ open machine”. Therefore, some
safety measures have to be taken to avoid
accidents.
Bear in mind the following safety instructions:
• The machine must always be operated for the purpose for which was
designed.
• Do not ever stand under a hanging machine or nearby, when it is been
loaded for transportation.
• Connect the machine to an exclusive electric connection, which includes
a differential switch of protection. Plug in first the green-yellow protection
wire and then the others.
• The piece must always be fastened with suitable devices. Do not ever
hand-hold the pieces.
• Sharpened tools in good condition must always be used.
• Appropiate tools must always be used. Do not ever adapt a tool for a use
for which it was not designed.
• Use the correct speeds and feeds for the material being machined as well
as for the tool being used.
• Use glasses to prevent small chips from getting in the eyes.
• Insert the tools correctly in the toolholder cone.
• Fix the piece fastening devices to the machine table.
• Do not wear baggy clothes, loose gloves, etc., which can be caught by
the tool while drilling.
• Do not wear long hair, or at least tie it back while drilling.
• Keep the working place clean.
• Gather the chips with suitable instruments (brush, gloves, etc.).
• Before carrying out any operation which is not strictly drilling, tapping, etc.
(like lubricating, changing of tools, etc.) turn the main switch to the "0"
position.
• Before changing speeds, stop the machine and wait until all moving
elements are completely brought to a halt.
• Do not ever leave the machine on without supervision. When leaving the
machine, check that the general switch is in the "0" position and that all
moving elements are stopped.
• Check periodically the correct operating of all security controls and
elements of the machine.
• Before pressing the starting pushbutton, set the drill protector guard in the
working position.
• Consider work area environment. D'ont use electric power driven tools in
damp or wet locations. Keep work area well lit. D'ont use electric power
tools in presence of flammable liquids or gases.
• Keep children away.
• Use only such accessories and attachments as are recommended in the
operating instructions or the catalogue for the power tool concerned.
1.2. FORESEEN USE OF THE MACHINE.
The drilling machine was designed to be used with specific tools and for
certain machining operations.
The most common machining operation is the drilling of holes with
helicoidal drills. The drilling of holes is carried out by the combination of a
drill turning movement and a feed movement in the turning spindle
direction.
Besides the helicoidal drill, other tools can also be used to drill holes. There
is a great variaty of drill types and shapes in the market which can be used
on this machine, provided that they are designed for such a purpose and
that can be fixed in the spindle taper. They will usually be the Morse taper
or ISO type. The drill shanks should have the corresponding taper to the
spindle in which they are to be fitted, or parallel shank if they are going to
be fitted by means of a toolholder. Contact the tool manufacturer for any
further information. Do not ever use tools which were not designed to be
used in a drilling machine and that have been adapted.
A drilling machine can also perform other machining operations a part from
the drilling, such as tapping, reaming, chamfering, puch marking,
countersinking, spotfacing. To perform such operations, it is necessary to
have appropiate tools, specially designed for this sort of jobs. In the tapping
case, besides using the correct tool, the machine has to be provided with
such a device that reverses the turning direction of the tool when it reaches
the tapping depth previously fixed.
Содержание AX-34
Страница 23: ...V 00 23 MANUAL FEED HANDVORSCHUB DESCENTE MANUELLE AVANCE MANUAL A SX 32 SX 34 SX 40...
Страница 24: ...V 00 24 AUTOMATIC FEED AUTOMATISCHE VORSCH BE AVANCE AUTOMATIQUE AVANCE AUTOMATICO B AX 32 AX 34 AX 40...
Страница 26: ...V 00 26 GEAR BOX GETRIEBEKASTEN BOITE DE VITESSES CAJA DE VELOCIDADES D 19...
Страница 27: ...V 00 27 NEW LIGHT SYSTEM NEUES BELEUVHTUNGSSYSTEM NOUVEAU SYSTEMA D ECLAIRAGE NUEVO SISTEMA DE ALUMBRADO...
Страница 28: ...V 00 28 X Z 32 COLUMN S ULE COLONNE COLUMNA...
Страница 30: ...V 00 30 X Z 34 COLUMN S ULE COLONNE COLUMNA...
Страница 32: ...V 00 32 X Z 40 COLUMN S ULE COLONNE COLUMNA...
Страница 35: ...V 00 35 HEAD BOHRKOPF T TE CABEZAL E...