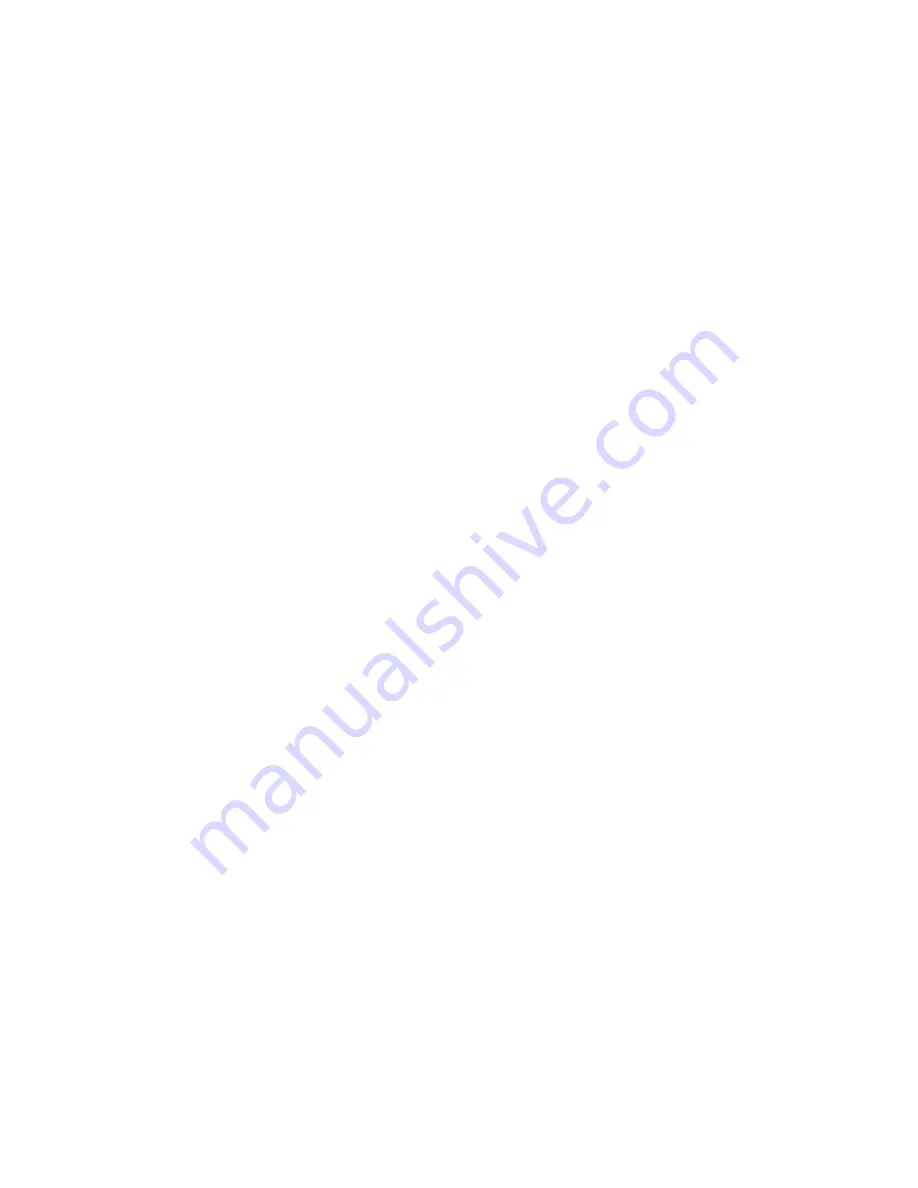
For backward joystick/lever movements, the joy-
stick/lever output signals are indicated with flow
direction A. For forward joystick/lever move-
ments, the joystick/lever output signals are indica-
ted with flow direction B. The specific joystick/
lever position and connector orientation prevent
joystick/lever directions from inadvertently result-
ing in incorrect oil flow directions.
Sensors
Additional analog input is provided by a tempera-
ture sensor and two pressure transducers.
Temperature Sensor
A temperature sensor at the bottom of the hy-
draulic tank has a resistance between 700 and 2000
Ω, depending on the hydraulic oil temperature.
The controller reacts to the temperature signal as
follows:
• When oil temperature is below −5°C (23°F),
the controller displays the fault code hcold.
• When Cold Temperature Protection is activa-
ted, the controller reduces maximum engine
speed by sending a CAN Bus message to the
engine.
• When oil temperature exceeds 90°C (194°F),
the controller displays the fault code hhot.
• When High Temperature Protection (op-
tional) is activated, the controller displays
the fault code hhot when oil temperature ex-
ceeds 88°C (190°F). When oil temperature
exceeds 90°C (194°F), the controller reduces
vehicle speed by sending a CAN Bus mes-
sage to the transmission.
Pressure Transducer
A pressure transducer measuring the pressure in
the lift cylinders provides an input to the hydraulic
controller for the load being lifted. The signal is
used for the following standard/optional features:
• Traction Speed Limiter - Loaded
• Traction Speed Limiter - Container Position
When the sensor detects an error, receives an input
below 300 mv or above 5200 mv, a fault code is dis-
played and the features are turned OFF.
Accumulator Pressure Transducer
A pressure transducer measuring the accumulator
pressure in the main valve (port S ACC) provides
an input to the hydraulic controller for enabling/
disabling the electronically-controlled charge func-
tion:
• Charging is enabled when the accumulator
pressure is below ±16.5 MPa (±2393 psi) for
0.5 seconds.
• Charging is disabled at an accumulator pres-
sure of ±20.5 MPa (±2973 psi).
DIGITAL INPUTS
Hydraulic Control Switches
Five auxiliary functions can be activated by manual
switches (digital inputs): Aux_2, Aux_3, Aux_4,
Aux_5, and Aux_6.
• Aux_2 (Twist Locks) - Lock/Unlock
• Aux_3 (Hydraulic Stop) - Lock/Unlock
• Aux_4 (Side Shift) - Right/Left
• Aux_5 (Extend/Retract) - Extend/Retract
• Aux_6 (Reach) - Forward/Backward
Depending on the position of the switch, the con-
troller sends a 24 volt signal to the relevant sole-
noid valve.
INTERRUPTS
Interrupts disable the lifting/lowering functions un-
der specific circumstances. The interrupts are gen-
erated in the Twist Module depending on the fol-
lowing signals:
• Not Locked Signal
• Locked Signal
• All Seated Signals
There are separate interrupt signals for lowering
and lifting.
1900 SRM 1561
Description
3