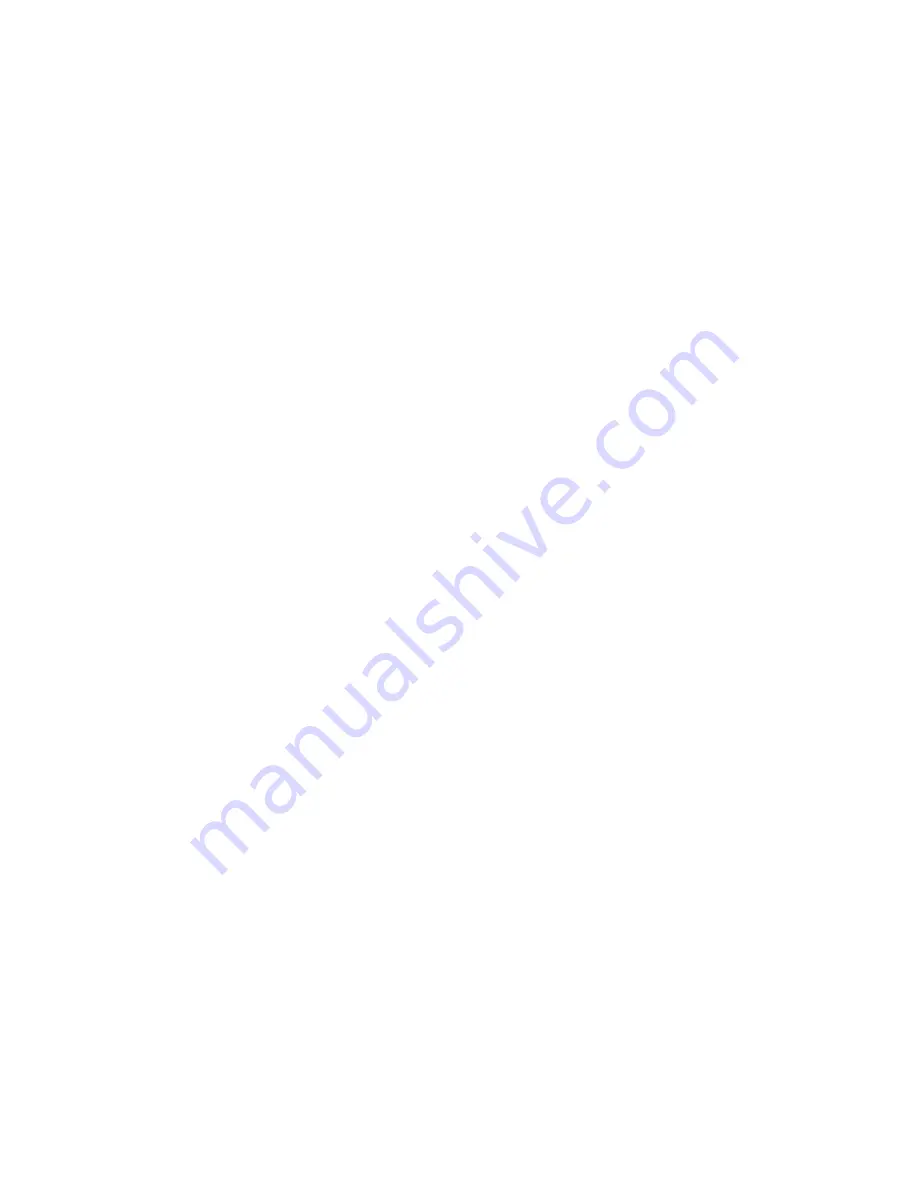
Lift Interrupt (Twist Module)
The lift interrupt function disables the lift function
during locking and unlocking of the twist locks.
Both signals “Not Locked” and “Locked” are used to
generate this interrupt. When the lift interrupt is
active the tilt backward function is also disabled.
Lower Interrupt (Twist Module)
The lowering interrupt function disables the lower-
ing function when all “Seated” signals are active.
All “Seated” signals are used to generate this inter-
rupt. When the lowering interrupt is active the tilt
forward function is also disabled.
Function Override
The “Lift Interrupt” and “Lower Interrupt” signals
can be overruled by the input: Function Override.
The "Function Override" button, if it is included on
the truck, is located on the twist module.
Operator Presence System (OPS)
The OPS has an electrical switch in the seat that
sends a signal to disable the hydraulic lift/lower,
tilt forward/backward, and auxiliary functions 1
second after the OPS switch has been activated.
In order to reset the OPS and re-enable the hy-
draulic functions, the operator has to sit on the seat
again.
DIGITAL SWITCHED INPUTS
ECO eLo HiP Switch
The ECO eLo HiP Switch switches between HiP
(High Performance) and ECO eLo (Fuel Efficiency)
operating modes. The switch is located on the
truck's side console.
Not Locked Signal
The Not Locked signal is used for the traction
speed limiter – container position, to switch be-
tween max vehicle speed, vehicle speed limit 1, or
vehicle speed limit 2. See Programmed Features.
(Lift Position, Tilt Position, Slew RH Position,
Slew LH Position) Sensor
The lift position sensor together with the tilt, slew
right hand, and slew left hand position sensors act
as one input for the “Traction Speed Limiter – Con-
tainer Position (Optional G117 Only)”. The sensors
are located on the mast/gantry and depending on
the position of the mast/gantry, the speed limiter
switches between max vehicle speed, vehicle speed
limit 1 or vehicle speed limit 2. See Programmed
Features.
Calibration Switch
When the calibration switch is activated, the
charger enable output is deactivated. The calibra-
tion switch also disables the hibernate idle function
and the automatic throttle-up features to make
sure the truck operates in normal idle mode so the
operator can calibrate the transmission at a fixed
engine speed.
Ignition Switch Signal
The ignition switch signal is used to activate the
“Hydraulic Control Relay” to maintain battery
power for 10 seconds after the ignition switch is
turned off. This is to provide the fan drive valve
with power so the system can be powered down in a
steady way.
Brake Filter Pressure Switch
The brake filter pressure switch signal indicates
that the brake pressure filter has too high a restric-
tion and needs to be replaced. The hydraulic oil
temperature needs to be at least 40°C (104°F) be-
fore a fault code is generated.
Pressure Signal
The spreader sends a pressure signal to the hy-
draulic controller to give output on the auxiliary
valve so the spreader can lock/unlock the twist
locks.
CAN BUS COMMUNICATION
CAN Bus communication can consist of both input
and output signals.
The hydraulic controller communicates via the
CAN Bus circuit with the following controllers:
Description
1900 SRM 1561
4