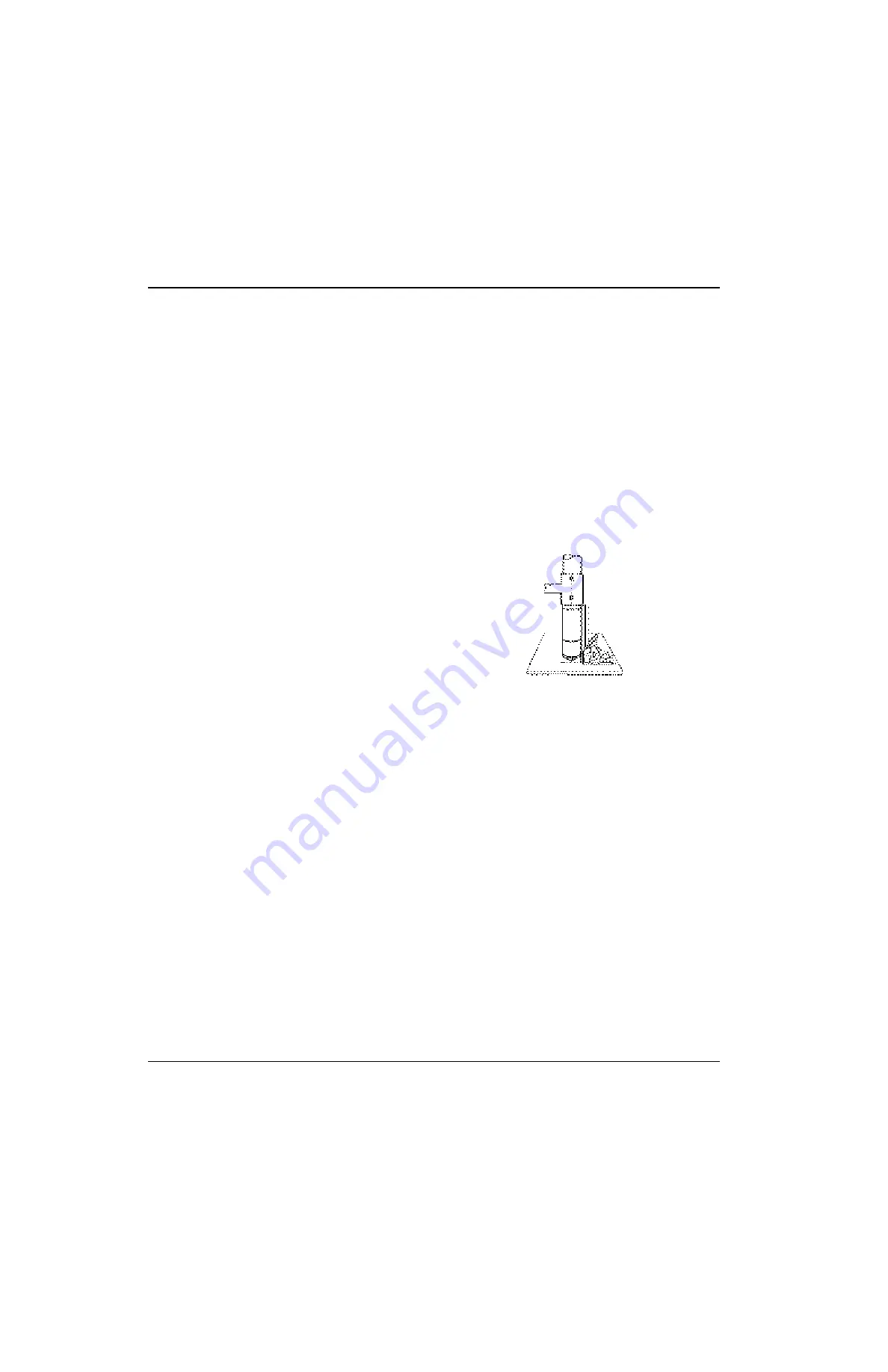
96
MAXPRO200
Instruction Manual 807700 Revision 1
Operation
•
Cut quality is poor. The causes can be:
•
The metal being cut is too thick for the amperage.
•
The wrong consumables are being used (gouging consumables are installed instead of drag-cutting
consumables, for example).
•
Moving the torch too quickly or too slowly.
•
The arc sputters and consumables life is shorter than expected. The cause can be:
•
Moisture in the gas supply.
•
Incorrect gas pressure.
•
Consumables incorrectly installed.
Optimizing cut quality
The following tips and procedures will help produce square, straight, smooth, and dross-free cuts.
Tips for table and torch
Plasma setup tips
Follow carefully each step in the Daily Start-up procedure described earlier in this section.
Purge the gas lines before cutting.
Maximize the life of consumable parts
Hypertherm’s LongLife
®
process automatically increases the gas and current flow at the start of each cut and decreases
them at the end to minimize erosion of the electrode’s center surface. The LongLife process also requires that cuts start
and stop on the workpiece.
•
The torch should never fire into the air.
•
Starting the cut at the edge of the workpiece is acceptable, as long as the arc is not fired in the air.
•
To start with a pierce, use a pierce height that is 1.5 to 2 times the cut height. Refer to the cut chart for your
process for more information.
•
Each cut should end with the arc still attached to the workpiece to avoid arc blow-outs (ramp-down
errors).
•
When cutting small parts that drop down after being cut from the workpiece, check that the arc remains attached
to the edge of the workpiece for proper ramp-down.
•
If arc blow-outs occur, try one or more of the following:
•
Reduce the cutting speed during the final part of the cut.
•
Stop the arc before the part is completely cut to allow completion of the cut during the ramp-down.
•
Program the path of the torch into the scrap area for ramp-down.
•
Use a square to align the torch at right angles to the workpiece.
•
The torch may travel more smoothly if you clean, check, and
tune motion on the rails and drive system of the cutting table.
Unsteady machine motion can cause a regular, wavy pattern on
the cut surface.
•
The torch must not touch the workpiece during cutting. Contact
can damage the shield and nozzle, and affect the cut surface.
Содержание MAXPRO200
Страница 1: ...MAXPRO200 Instruction Manual 807700 Revision 1 ...
Страница 3: ...MAXPRO200 Instruction Manual 807700 Revision 1 English March 2013 Hypertherm Inc Hanover NH 03755 USA ...
Страница 26: ...22 MAXPRO200 Instruction Manual 807700 Revision 1 Safety ...
Страница 34: ...30 MAXPRO200 Instruction Manual 807700 Revision 1 Product Stewardship ...
Страница 38: ...34 MAXPRO200 Instruction Manual 807700 Revision 1 Specifications ...
Страница 88: ...84 MAXPRO200 Instruction Manual 807700 Revision 1 Operation Side gouging Side gouge Weaving gouge ...