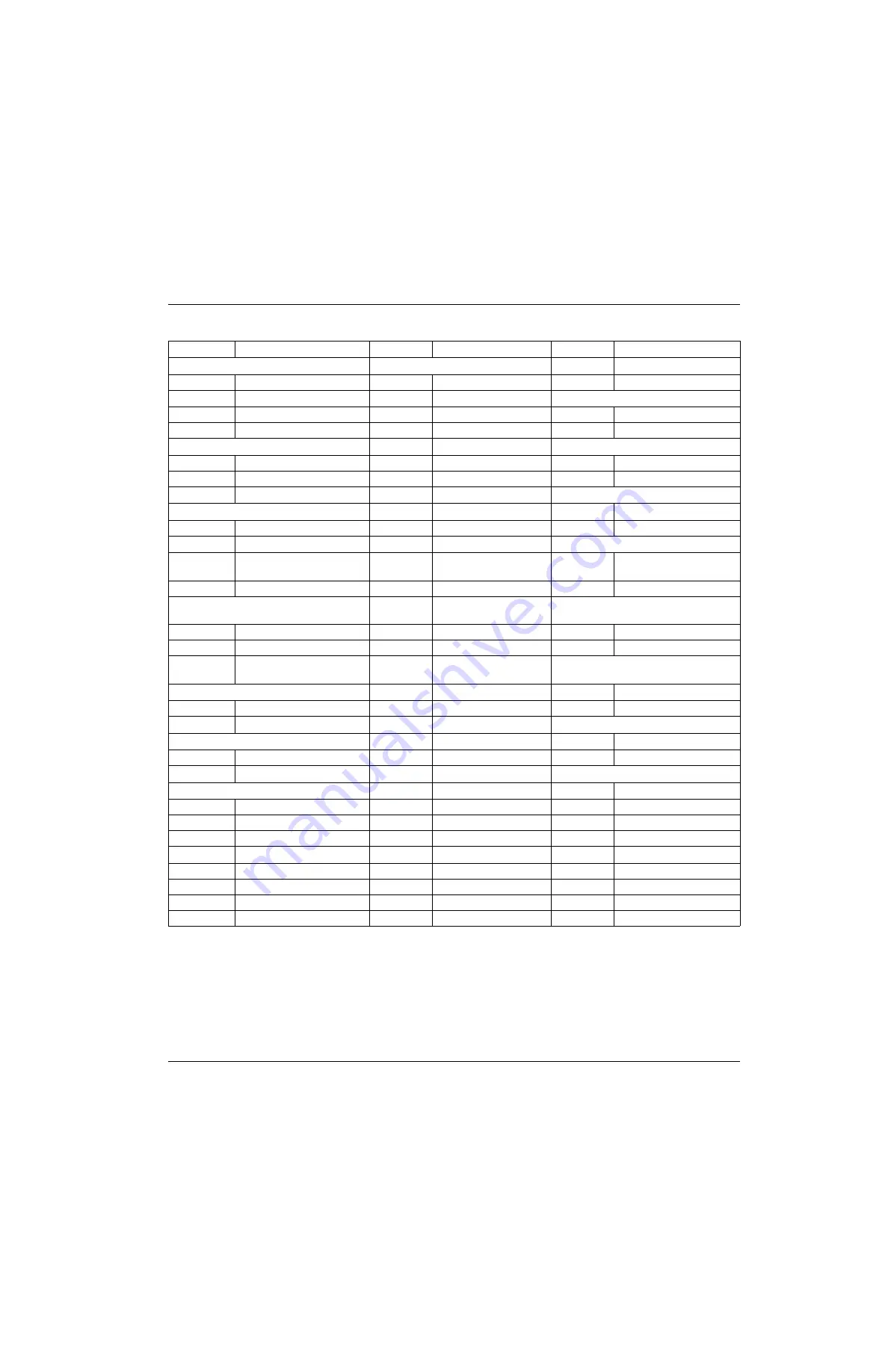
EDGE Pro Ti CNC
Instruction Manual 807660
119
Maintenance and Diagnostics
Operator control panel board (141058)
Table 22 Pinouts for J1 to J16
Pin no.
Signal
Pin no.
Signal
Pin no.
Signal
J1 Station 2
J7 To utility PCB
33
Logic +5 V
1
Auto select 2
1
Start
34
Logic +12 V
2
Logic ground
2
Stop
J9 Raise 2
3
Manual select 2
3
Manual
1
Logic ground
4
Not used
4
Forward on path
2
Raise torch 2
J2 Jog potentiometer
5
Backward on path
J10 Raise 1
1
Logic ground
6
JoY
1
Logic ground
2
Analog (jog speed)
7
Joystick -Y
2
Raise torch 1
3
4.096 V Reference
8
Joystick -X
J11 Manual
J3 Station 1
9
JoX
1
Logic ground
1
Auto select 1
10
Logic ground
2
Manual switch
2
Logic ground
11
Logic ground
J12 Lower 2
3
Manual select 1
12
Not connected Front panel
ID 1
1
Logic ground
4
Not used
13
Ground Front panel ID 0
2
Lower torch 2
J4 Cut potentiometer
14
Not connected Front panel
ID 1
J13 Lower 1
1
Logic ground
15
Logic ground
1
Logic ground
2
Analog (cut speed)
16
Logic ground
2
Lower torch 1
3
4.096 V Reference
17
Not connected Front panel
ID 2
J14 Forward
J5 Stop
18
Auto select 1
1
Logic ground
1
Logic ground
19
Manual select 1
2
Forward on path
2
Stop switch
20
Raise torch 1
J15 Back
J6 Start
21
Lower torch 1
1
Logic ground
1
Logic ground
22
Auto select 2
2
Backward on path
2
Start switch
23
Manual select 2
J16 Power switch
J8 Joy stick
24
Raise torch 2
1
Logic +12 V
1
Up
25
Lower torch 2
2
MB On/Off 1
2
Down
26
Station enable LED1
3
MB On/Off 2
3
Left
27
Station enable LED2
4
Logic ground
4
Right
28
Motherboard On/Off 1
5
Logic ground
29
Motherboard On/Off 2
6
Logic ground
30
Cut speed
31
Jog sped
32
4.096 V Reference
Содержание EDGE Pro Ti
Страница 1: ...Instruction Manual 807660 Revision 3 EDGE Pro Ti Shape Cutting Control...
Страница 18: ...xviii Safety and compliance Safety...
Страница 48: ...48 EDGE Pro Ti CNC Instruction Manual 807660 Installation Mounting the THC...
Страница 92: ...92 EDGE Pro Ti CNC Instruction Manual 807660 Installation Hypernet and LAN cable...
Страница 144: ...144 EDGE Pro Ti CNC Instruction Manual 807660 Maintenance and Diagnostics Plasma interface assembly 228256...
Страница 149: ...EDGE Pro Ti CNC Instruction Manual 807660 149 EDGE Pro Ti Parts List PCB kits 9 8 7 6 5 4 3 2 1...
Страница 154: ...154 EDGE Pro Ti CNC Instruction Manual 807660 Wiring Diagrams Wiring diagram symbols...