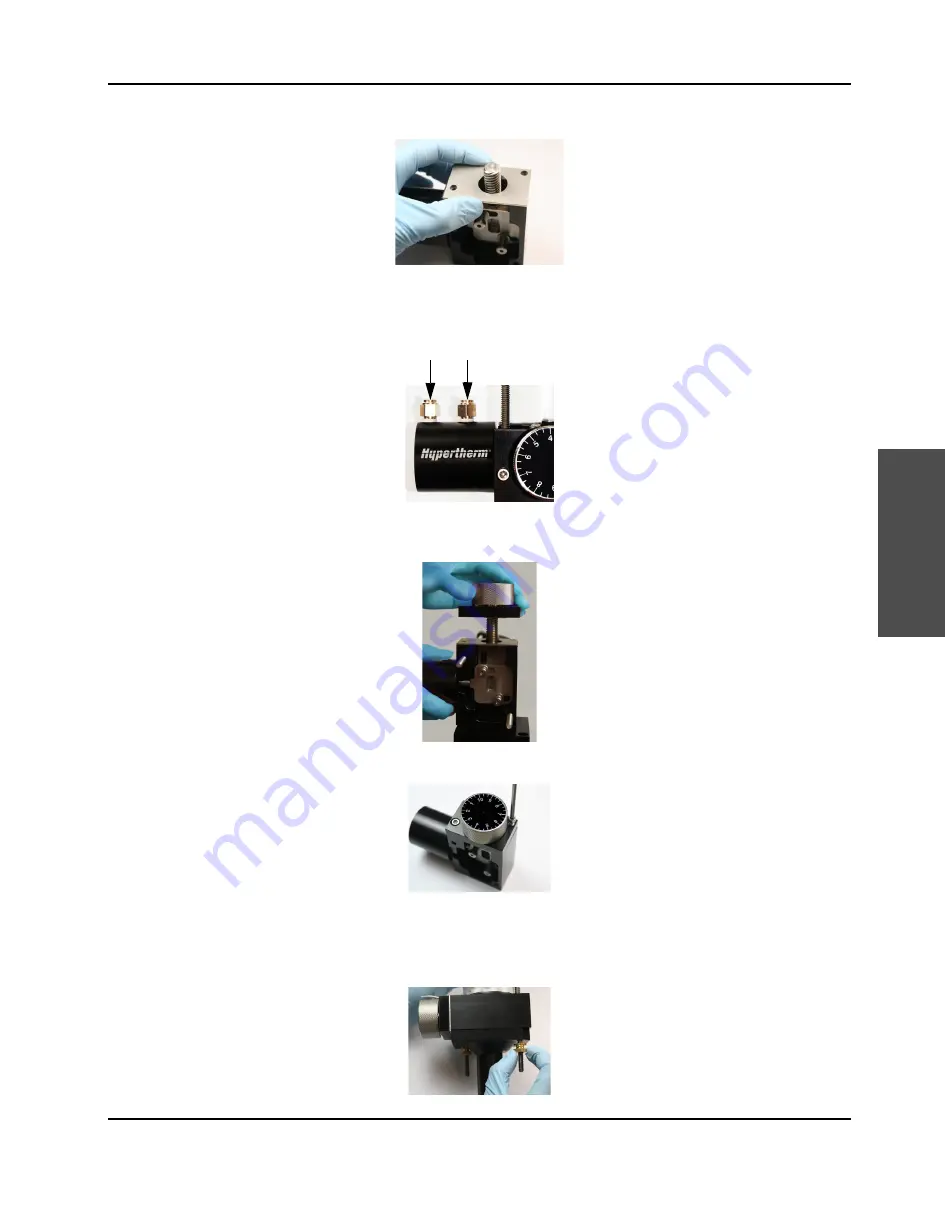
Abrasive Regulator II
Instruction
Manual 809030
29
Preventive maintenance
Preventive mainte
na
n
ce
7.
Put the divider on the side of the housing base.
Make sure that the beveled side of the divider faces out.
8.
Blow compressed air into 1 air cylinder fitting to make sure that the gate slides back and forth. Repeat this
procedure on the other air cylinder fitting.
9.
Put the control knob mounting plate onto the divider so that the holes line up. Turn the control knob clockwise
until it is tight on the regulator base.
10.
Install the socket-head cap screws. Tighten the screws.
11.
Put the regulator base on the threaded rods.
12.
Reassemble the thumb nuts on the threaded rods. Hand tighten the thumb nuts with the knurled side toward the
end of the threaded rod.
Содержание Abrasive Regulator II
Страница 1: ...Abrasive Regulator II Instruction Manual 809030 Revision 0 English ...
Страница 4: ......
Страница 6: ...6 Abrasive Regulator II Instruction Manual 809030 Contents ...
Страница 8: ...SC 8 Safety and compliance Warranty Warranty ...
Страница 10: ...SC 10 Safety and compliance Environmental stewardship Environmental stewardship ...
Страница 12: ...SC 12 Safety and compliance Safety Safety ...
Страница 14: ...SC 14 Safety and compliance Symbols and marks Symbols and marks ...
Страница 18: ...18 Abrasive Regulator II Instruction Manual 809030 Product description Product description ...
Страница 34: ...34 Abrasive Regulator II Instruction Manual 809030 Parts lists Parts lists ...