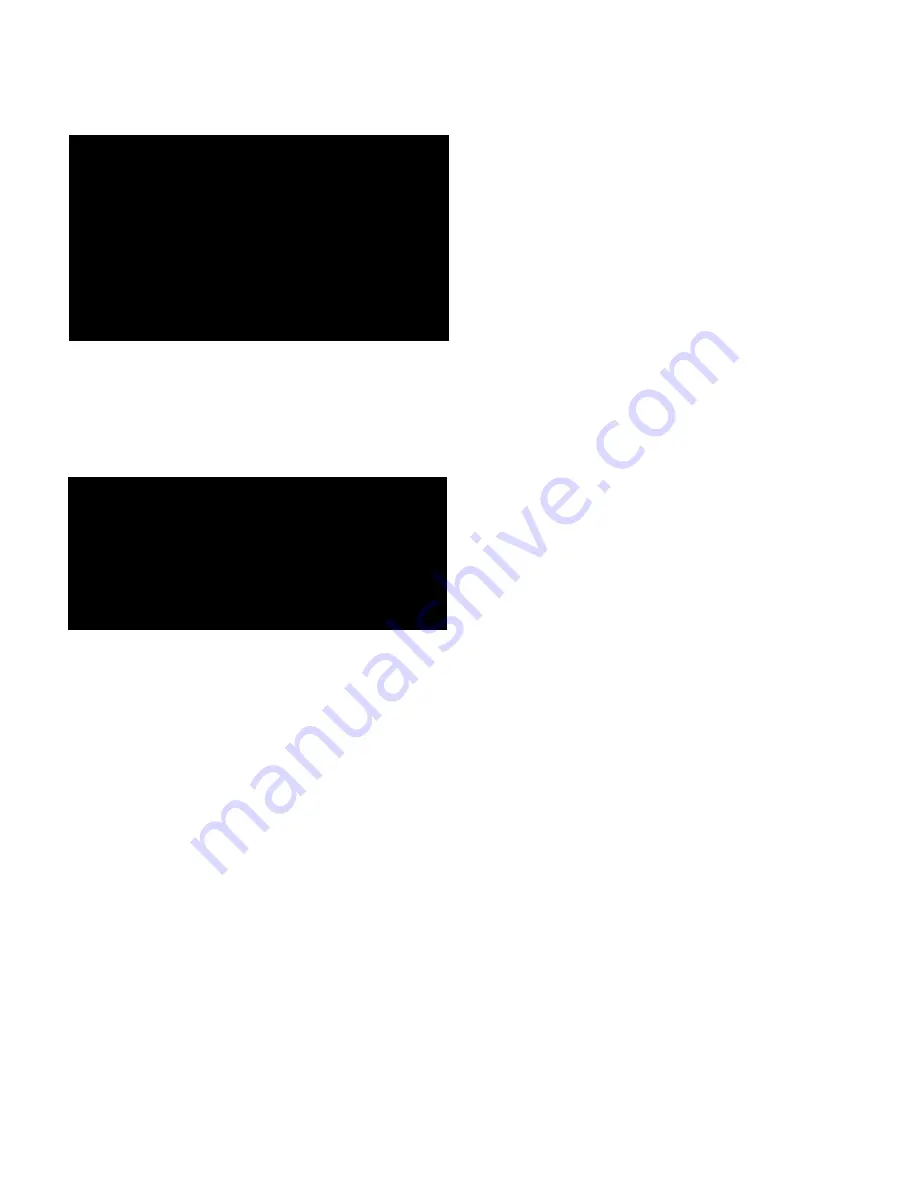
SECTION 4: MAINTENANCE
This boiler has been designed to provide years of trouble
free performance in normal installations. Examination by
the homeowner at the beginning of each heating season,
and in mid-heating season, should assure continued good
performance. In addition, the boiler should be examined by
a qualified service professional at least once every year.
NOTE: Do not draw water from heating system for
cleaning. Minerals in the water can build up on the
heat transfer surfaces and cause overheating and
subsequent failure of the cast iron sections.
NOTE: To reduce the risk of fouling, the low water cut-
off should be blown down at least once a week during
heating season.
BEFORE EACH HEATING SEASON
1. Remove and inspect draft diverter and smoke pipe
(connecting draft diverter to chimney or vent) for obstruc-
tions, soot accumulation, rust or corrosion. Clean and
replace as necessary. Check tightness of joints; seal all
joints where necessary.
2. Check boiler flue passageways in the boiler sections for
any blockage or soot accumulation. Remove draft diverter,
jacket top and flue collector. Using a flashlight, examine all
flue passageways.
a. If passageways are free of soot and obstructions,
replace collector and seal with furnace cement.
b. If passageways need cleaning, remove flueway baffles
and burners as described in paragraph 3 below. Insert
long-handle bristle flue brush down between section
tubes and upward through sections from combustion
chamber in both diagonal directions to remove carbon
from finned surfaces. Vacuum debris. Replace the draft
diverter and seal with furnace cement.
c. Reinstall jacket top panel and draft diverter.
3. Check and clean burner assembly. Remove burner
access panel. Lift burners up and to rear until burners are
disengaged from orifices. Brush top of burners with soft
bristle brush and blow out with air or vacuum.
4. Check gas manifold for proper position and reassemble
burners to the manifold. Line up holes in burners with the
orifices, and slide assembly back into position. BE SURE
TO REINSTALL BURNERS WITH BURNER PORTS ON
THE TOP SURFACE (UPRIGHT).
5. When a low water cut-off has been utilized, follow the
manufacturer’s maintenance instructions. As a minimum,
Inspect the probe and test the operation of electronic con-
trols at least once a year. Remove, clean and inspect the
probe. Float type controls should be flushed once a month
during heating season. If the LWCO fails to operate prop-
erly it must be replaced.
6. Follow "System Start-Up & Adjustments" procedures in
Section 3 of this manual.
STEAM BOILER CLEANING INSTRUCTIONS
The following procedures must be followed on initial start-
up and if the presence of sediment, sludge or impurities
hamper proper boiler operations.
1. With gate valves closed on supply and return lines, start
burner and allow boiler to become pressurized so that the
pressuretol may be adjusted and set for limit cut-off
desired (normally about 3 psi). Turn off burner and allow
pressure to drop to 0 psi., then proceed with the following
cleaning procedure.
2. Remove the pressure relief valve.
3. Add caustic soda (lewis lye) through this opening at the
rate of one pound per thousand square feet of radiation
capacity. Scout, Squirk or similar steam boiler cleaners
may be used instead of lye. Trisodium phosphate (1/4#) is
also an excellent cleaner.
4. Provide pipe connection (full size) from pressure relief
valve opening to a convenient drain to serve as a vent.
5. Fill the boiler with a manual fill valve until water starts to
trickle from this pipe.
DANGER:To avoid fire and explosion hazards: Do
not store anything against the boiler or allow dirt or
debris to accumulate in the area immediately sur-
rounding the boiler. Keep boiler area clear and free
from combustible materials, gasoline and other
flammable vapors and liquids. Lint, paper or rags
must not be allowed to accumulate near the burn-
ers. Do not place clothing on boiler casing to dry.
15
WARNING: Improper installation, adjustment, alter-
ation, service or maintenance can cause property
damage, personal injury exposure to hazardous
materials or loss of life. Installation and service
must be performed by a qualified installer, service
agency or the gas supplier who must read and fol-
low the supplied instructions before installing, ser-
vicing or removing this boiler, This boiler contains
crystalline silica materials that have been identi-
fied as carcinogenic or possibly carcinogenic to
humans when inhaled.
Содержание VSB2-605
Страница 23: ...23 NOTES...