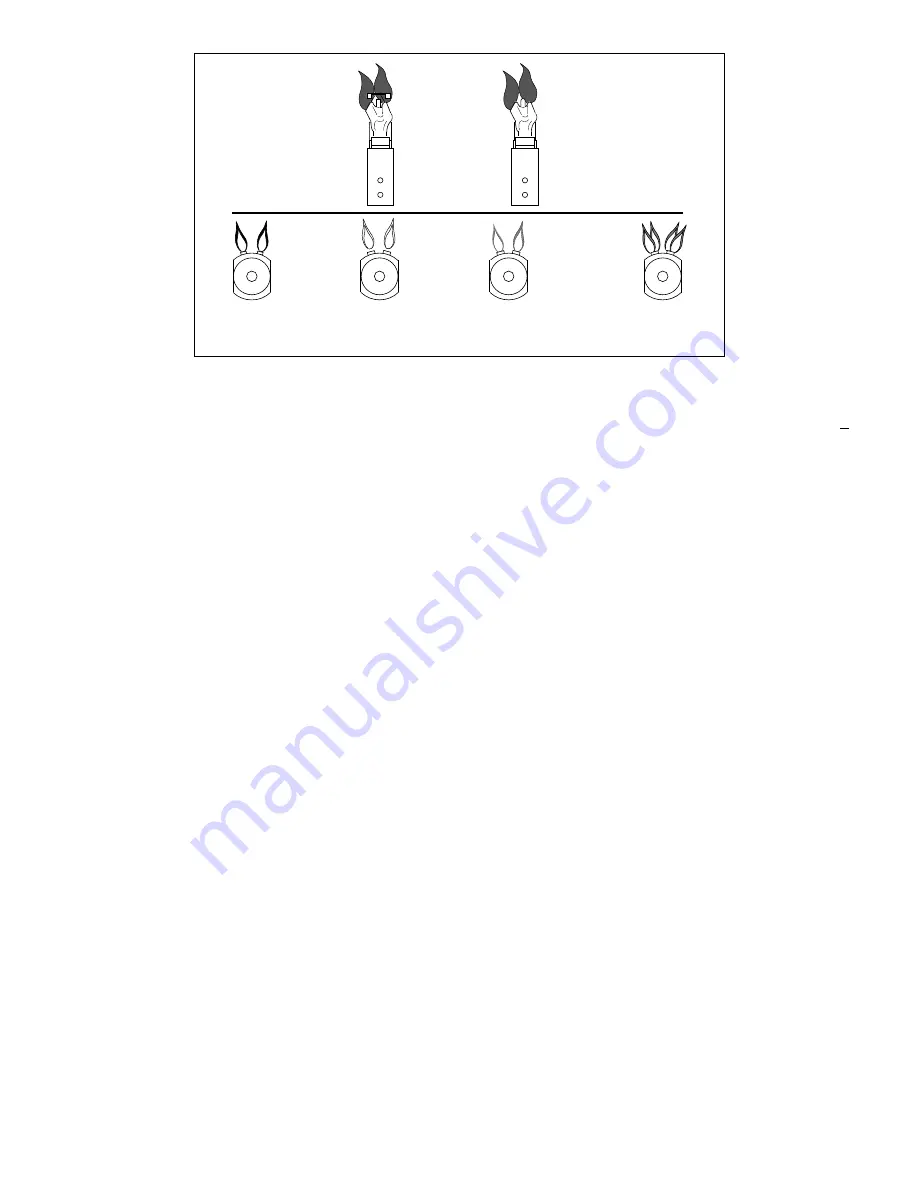
tion unless there is lifting of the flame above the burner
ports. If there is lifting, the air shutters should be gradu-
ally closed until the lifting is eliminated. It may also be
necessary to adjust the primary air shutters if the input
rate is reduced by a change in the orifices.
6. After burner has been in operation for about 10 min-
utes, check gas input rate to boiler as follows:
a. Make sure all appliances served by the meter are
turned off during timing of gas input rate to the boiler.
b. Measure the time in seconds that it takes for the
boiler to use 10 cubic feet of gas. Divide 36,000 by
the number of seconds (this is the number of cubic
feet of gas used per hour). Multiply this figure by the
heating value of the gas to obtain Btu input per hour.
Example: A VS-110B boiler takes 5 minutes, 27 sec-
onds to use 10 cubic feet of natural gas. The local utility
indicated the heating value of the natural gas being sup-
plied is 1000 Btu/cu ft. Therefore:
5 minutes, 27 seconds = 327 seconds.
36,000
X 1000 = 110,000 Btu/hr
327
Therefore, the boiler input is correct.
NOTE: Before calculating the input of the heating
equipment, obtain the heating value of the gas from
the local utility.
7. If input needs to be corrected, adjust combination gas
valve pressure regulator. (Regulator is factory set at 3-
1/2" W.C. for natural gas and 10" W.C. for propane.)
Turn adjusting screw clockwise to increase gas flow
(increase input). Turn adjusting screw counterclockwise
to decrease gas flow (decrease input). In no case
should final manifold pressure setting vary more than +
.3" from factory-set pressures. If rated input cannot be
obtained with adjustment, gas supply pressure or orifice
size may be cause. Consult local utility and Hydrotherm.
8. Gas burner orifices supplied with boiler have been
carefully designed to provide correct gas input rate for
most gas conditions typically found in the U.S. Occa-
sionally, however, local gas characteristics may not allow
unit to be properly adjusted for input. If this is the case,
local utility or Hydrotherm may recommend orifices be
changed. When changing orifices follow the procedures
detailed in Section 4 of this manual.
9. Start and stop burners several times by raising and
lowering the thermostat setting.
10. After boiler has been firing long enough to raise boil-
er pressure above minimum setting of the primary pres-
suretol limit, check limit by turning its setting from maxi-
mum to minimum setting. This should turn boiler off.
Return limit to desired setting.
11. Check boiler safety shutoff controls.
a. For boilers with standing pilot, with boiler firing, dis-
connect thermocouple lead from the valve. The valve
should close.
b. For boilers with intermittent pilot, with boiler firing,
disconnect wire connected to the "PV" terminal on the
Honeywell S8600 control. The gas valve should
close.
12. On initial start-up and prior to each heating season,
boiler must be cleaned with a commercially available
steam boiler cleaner (see "Steam Boiler Cleaning
Instructions" in Section 4 of this manual).
12
FIGURE 3.2: BURNER FLAME COMPARISON/PILOT FLAME
NORMAL
(HARD FLAME)
LIFTING
(TOO MUCH AIR)
YELLOW TIPPING
(MARGINAL)
YELLOW FLAME
(TOO LITTLE AIR)
NORMAL PILOT
FLAME
MAIN BURNER FLAMES
Q314A/Q309A
CONSTANT PILOT
MODELS
Q345
INTERMITTENT
IGNITION PILOT
MODELS
Содержание VSB2-605
Страница 23: ...23 NOTES...