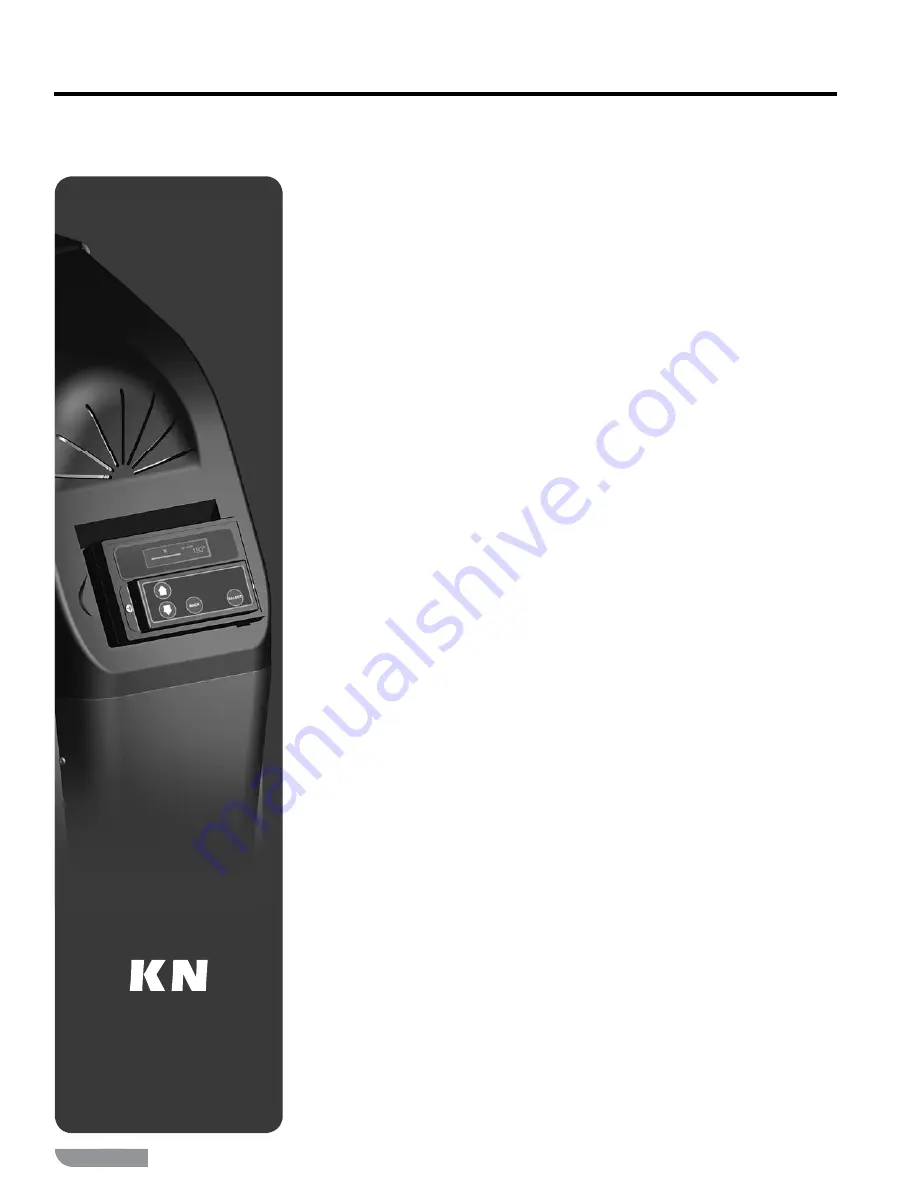
2
P/N 42-9452 8/08 Copyright Hydrotherm
KN USER’S CONTROL MANUAL
The KN boiler — HeatNet
TM
control
Control overview
Th e KN HeatNet control monitors boiler temperature and limit circuit inputs, modulating boiler fi ring
rate to meet demand. Th e control uses microprocessor electronics, watching time-average response from
the system to anticipate how much heat the system needs. Coupled with the fi ve-to-one turndown of the
KN boiler, this results in maximum possible condensing-mode operation. Th e KN boiler will provide
unmatched seasonal effi ciency.
Indoor air reset (IAR)
HydroTh erm’s unique approach to boiler output regulation is its Indoor Air Reset function. Th e control
monitors the demand from up to 8 diff erent zones. Watching the demand duration and response to supply
temperature, averaging over time, the HeatNet control anticipates system needs. It sets boiler maximum
fi ring rate and adjusts supply water temperature to fi ne-tune boiler heat output. All that is required to
enable IAR is to connect thermostat circuit wires to the IAR inputs. Th e HeatNet control can also be
confi gured for outdoor reset operation, but IAR provides response based on system behavior rather than
just looking at outdoor temperature.
The HeatNet platform
HeatNet controls are designed to provide an integrated boiler management system on every boiler. Th e
platform provides multiple levels of selectivity. HeatNet electronics can be operated as a simple single-
boiler control, while still providing intelligent regulation of boiler fi ring rate to match system demand.
With a few key strokes on the key pad, the HeatNet control can operate as a sophisticated multiple-boiler
controller, using simple RJ45 cable interfacing between units. Th
e control can even accept external control
commands from building managements systems (Modbus standard, with optional bridge for BACnet or
LonWorks) or 20-milliamp analog input from an external controller.
Th
e control method used by the HeatNet control is based on digital communications, which eliminates the
need for analog control signals. Analog signal inputs are supported, but a higher level of control precision,
repeatability and feedback is gained with digital communications.
Th e HeatNet control can be versatile, providing for operation in multiple ways:
Operation as a stand-alone boiler.
Operation as a boiler in a boiler network, using the on-board HeatNet protocol.
Operation as a member boiler in a boiler management system.
Operation as a member of a remotely-controlled boiler network (20-milliamp regulation).
Setpoint can be determined by the HeatNet control or by a 20-milliamp input signal.
PID response
Th e HeatNet control uses proportional-integral-derivative calculations to determine the response to
boiler water temperature changes. Th is means it not only looks at how far away the water temperature is
from the setpoint temperature, but how fast the temperature is changing and how it has responded over
time. Th is ensures the boiler won’t make sudden unnecessary changes in fi ring rate.
Multiple boiler operation
Th
e HeatNet control easily interfaces with other HeatNet controls. Multiple boiler operation using HeatNet
protocol only requires RJ45 cables daisy-chained from boiler to boiler and a few key strokes sett ing up
control behavior. Th e master boiler is automatically selected by connecting a sensor lead to its HEADER
sensor terminals. Th e HeatNet control recognizes the sensor and confi gures the boiler as the master.
Other boilers only need to have an address assigned.
Among the advanced design features of the HeatNet control is the MOD-MAX sett ing. Th is limits the
fi ring rate of all boilers to a pre-set maximum (50% by default). Th
is means all of the boilers will be run
at a very effi cient level until all boilers are on. Only then can fi ring rate increase above this sett ing. Boiler
rotation can be fi rst-on/fi rst-off , fi rst-on/last-off , or true rotation (the HeatNet control monitors the total
on time of all boilers, and rotates their usage so the total on time is the same for all).
•
•
•
•
•
HeatNet
Control panel