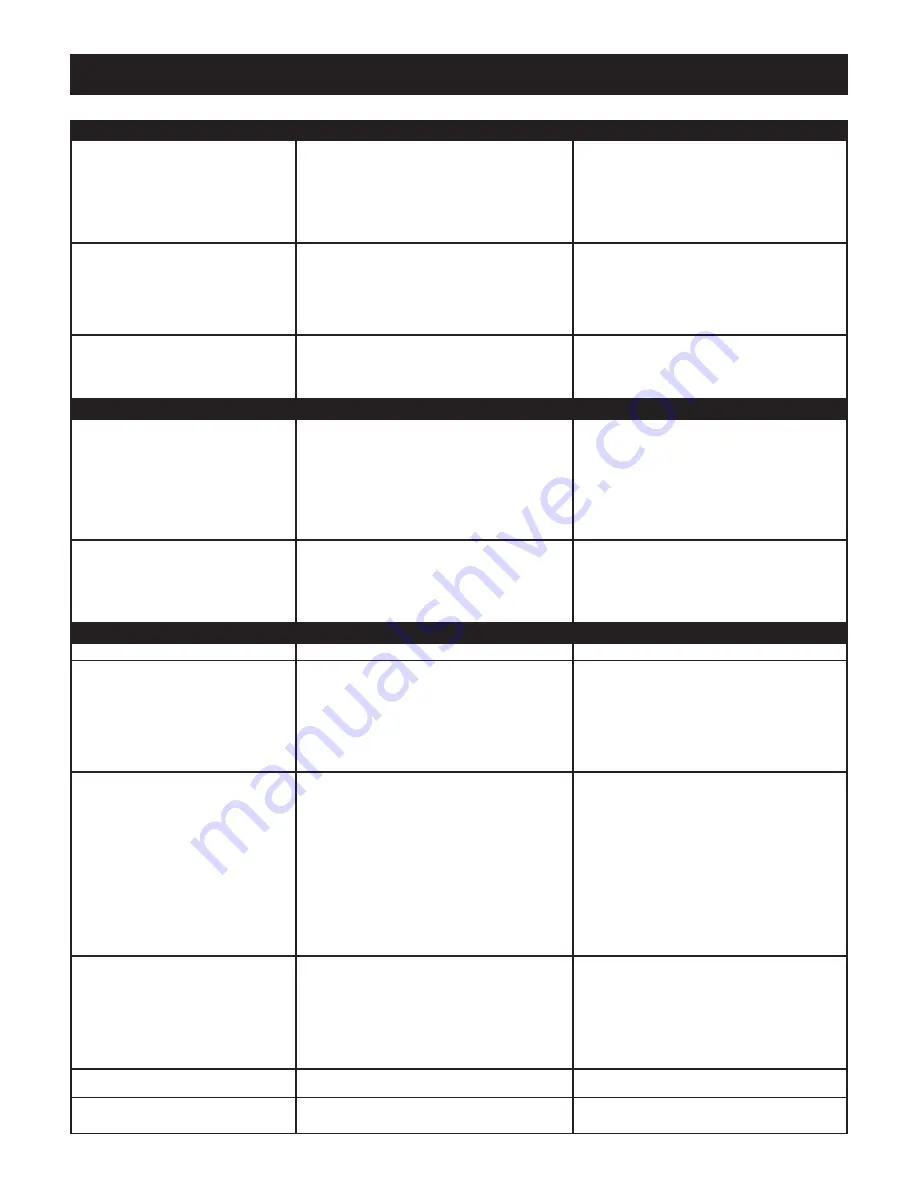
12
TROUBLE SHOOTING GUIDE
PROBLEM
PROBABLE CAUSE*
REMEDY
Charge or replace battery, add electrolyte if
battery is new.
Clean connections.
Connect or replace damaged cables.
Replace or repair seized part.
Repair or replace.
Check engine power switch.
Add oil to engine, check more frequently.
Fill with the appropriate fuel.
Replace or clean fuel filter.
Choke only as required.
See engine manual or engine dealer.
Lower the pressure on the unit and check for
correct engine speed (RPM).
Remove head and wire brush deposits.
Check cord, plug, socket, and breaker.
Reset manual overload by depressing the thermal
switch on the outside of the motor or starter after the
motor has cooled. CAUTION! Automatic overload will
restart the motor automatically when it has cooled.
Check power switch.
Replace or repair motor and/or wiring.
Connect water Supply.
25 psi minimum.
Descale coil for better water flow.
Remove spray nozzle and pull trigger to check
auto-start function
Check mechanical function & electrical signal to relay.
Clean valve assembly or replace gun.
Turn water on.
Clean or replace with proper size.
Close soap valve or submerge detergent pickup
tube into solution.
Clean obstruction or scale deposits from coil
with coil cleaner.
Crack open fitting on high pressure outlet of pump.
Install Nozzle.
Dual wand valve must be closed and high
pressure nozzle installed.
Replace hose, quick coupler, or o-ring in the
quick coupler.
Clean and check more frequently.
Replace with nozzle of proper size.
Tighten or replace with correct belt.
Install pressure gauge on pump head to adjust
pressure. Check valve seat on unloader.
Reseal fittings and inspect inlet hoses for air leaks.
Increase water supply flow.
Clean out or replace worn valves.
Check fittings and hose for air tight seal, clean
inlet strainer screen.
Replace seals.
Pressure feed the pump and replace L.P. seals
if water leaks from the pump head.
Replace pump or bearing.
Locate point of oil leakage and replace damaged
O-ring or seal.
* The most recurring probable cause is listed first. Repairs should be made only by a qualified technician.
Power System: Gasoline Engine Driven
Engine will not start or crank over.
Engine will not start but will crank
over.
Engine bogs down under load,
whenever spray gun is triggered.
Electric motor does not start.
Machine will not auto-start(If
equipped).
Trigger gun leaks or will not shut off.
Pump runs but there is no spray pressure.
Pump runs but has low spray pressure.
Pump runs but there is erratic,
fluctuating pressure.
Excessive crankshaft play or loud,
knocking noise in pump.
Oil leaking from pump.
Pumping System
Battery dead.
Dirty battery connection.
Battery cables disconnected.
Engine, pump, or gearbox is seized.
Keyswitch, solenoid and starter on engine
defective.
Engine power switch is off or defective.
Low oil shut down is activated.
Low on fuel.
Fuel filter is clogged.
Engine flooded or starved.
Engine needs to be repaired or replaced.
Operating in high elevation.
Carbon deposits on cylinder head.
No electric power.
Thermal overload in the motor or starter has
been tripped.
Power switch inoperative.
Electric motor or wiring failure.
No water to inlet.
Must have adequate water supply.
Coil scale build up.
Check filter screen & inlet pressure.
Inlet flow switch defective or jammed with
debris.
Debris in gun valve assembly.
Water turned off.
Nozzle is plugged.
Inlet chemical injection valve is open, without the
end of the pickup tube inserted into detergent.
Coil on hot water machines is obstructed.
Priming of pump after run dry.
Nozzle not installed.
Dual wand valve is open.
Leaky discharge hose or quick coupler.
Water sprays out around nozzle.
Inlet strainer clogged.
Worn or wrong size nozzle.
Belt slippage.
Unloader valve worn or improperly adjusted.
Air leak in inlet plumbing.
Inadequate incoming water supply.
Stuck inlet or discharge valves.
Restricted inlet or air entering the inlet plumbing
on the pump.
Leaking H.P. seals.
Leaking L.P. seals.
Broken or worn bearing or connecting rod in
crankcase.
Loose drain plug or damaged seal.
Power System: Electric Motor Driven
Содержание HG SERIES
Страница 16: ...WIRING DIAGRAMS ST 16 ...
Страница 17: ...17 WIRING DIAGRAMS ST ...
Страница 18: ...WIRING DIAGRAMS SR 18 ...
Страница 19: ...19 WIRING DIAGRAMS SK ...
Страница 20: ...20 WIRING DIAGRAM SH ...
Страница 21: ...21 WIRING DIAGRAMS SH ...
Страница 22: ...22 WIRING DIAGRAMS HG ...