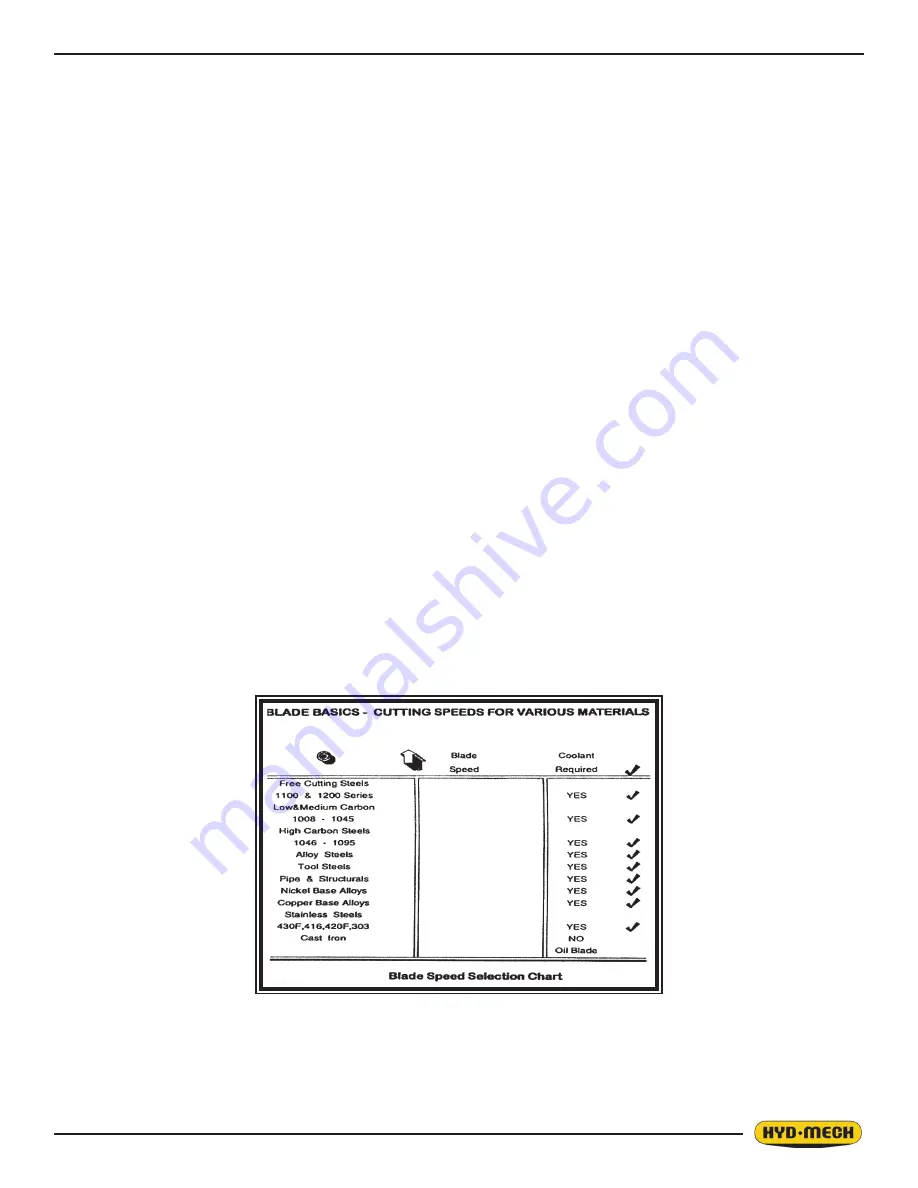
2.5
BLADE BASICS
Technology is rapidly changing all aspects of production machining. Metal cutoff is no exception. The advances made in
the bandsaw industry have definitely brought down the cost per cut, despite the three-fold increase in the price of newer
technology blades. Variable pitch (following pages), bi-metal blades (like the ¾ or 4/6 bi-metal blade supplied with the
Hyd-Mech machine) last much longer, cut faster and more accurately than the conventional carbon steel blades. In order
to take advantage of the superiority of bi-metal blades, it is critical to properly “break in” a new blade. This is accomplished
by taking two or three cuts through solid four or five-inch diameter mild steel at an extremely slow feed rate. These two or
three slow cuts sufficiently lap (polish) the new blade so that it does not snag the material being cut. Proper break-in will
alleviate blade vibration, improve surface finish and accuracy, and improve expected blade life.
1. A new blade must be properly “broken-in”.
Proper break-in will alleviate blade vibration, improve surface finish
and accuracy, and improve expected blade life. The most convenient way to do this is to cut the intended work-
piece, at the standard recommended blade speed for that material, but with the feed rate reduced to about 25% of
normal. Near the end of the first cut, increase the feed rate again, and once again when the blade approaches the
end of the second cut. Keep increasing feed rate in this fashion, so that normal feed rate is reached after 300 to
400 square centimeters of cutting.
2. Generous coolant application is essential with almost all materials.
A high quality and well-mixed coolant will
dramatically extend blade life, and will increase cutting rate and surface finish. On those few materials where cool
-
ant is undesirable, a slight coolant flow or periodic oiling of the blade is necessary to prevent the blade from being
scored by the carbide guides.
3. The Stock being cut must be securely clamped in the vises
. Stock movement during cutting will strip blade
teeth. Noticeable stock vibration reduces cutting performance and blade life – consideration should be given to
reorientation of the stock, or additional clamping measures (e.g. wood between vise jaws and work-piece).
4. The proper blade speed for the work-piece material must be selected
. Use the following chart as a starting
point:
Blade speeds higher than recommended will quickly dull the blade. Blue chips are evidence of excessive blade
speed.
Lower than recommended speeds will not prolong blade life, and will require reduced feed rate. However, reduced
speeds may be helpful in reducing vibration, and therefore may increase blade life.
5. The proper feed rate must be applied
. Feed rate is the speed which the head “free-falls” and is set with the feed
rate control knob. The head will descend more slowly when the blade encounters the work-piece. Verification of
proper feed rate is provided by the appearance of the cut chips, which ideally form nicely curled “clock springs”.
Note that cast irons and interrupted cuts result in short, broken chips even at ideal feed rates. Excessive feed rate
will result in short blade life and/or crooked cuts.
(
( in SFM )
310
220
140, 220
140, 220
90, 140
140, 220
90, 140
140, 220
140, 220
140, 220
Содержание S20 SERIES III
Страница 2: ......
Страница 16: ......
Страница 24: ......
Страница 36: ......
Страница 38: ......
Страница 39: ...5 1 FOR HYDRAULIC SCHEMATICS AND PLUMBING DIAGRAMS SEE PDF ON ATTACHED CD SECTION 5 HYDRAULIC ...
Страница 40: ......
Страница 41: ...6 1 FOR MECHANICAL ASSEMBLY DRAWINGS SEE PDF ON ATTACHED CD SECTION 6 MECHANICAL ASSEMBLIES ...
Страница 42: ......
Страница 43: ...7 1 FOR OPTIONAL ASSEMBLY DRAWINGS SEE PDF ON ATTACHED CD SECTION 7 OPTIONS ...
Страница 44: ......
Страница 46: ...8 2 S20 Series III Layout ...
Страница 47: ...8 3 S20 Series III Foot Print ...
Страница 48: ......
Страница 50: ......