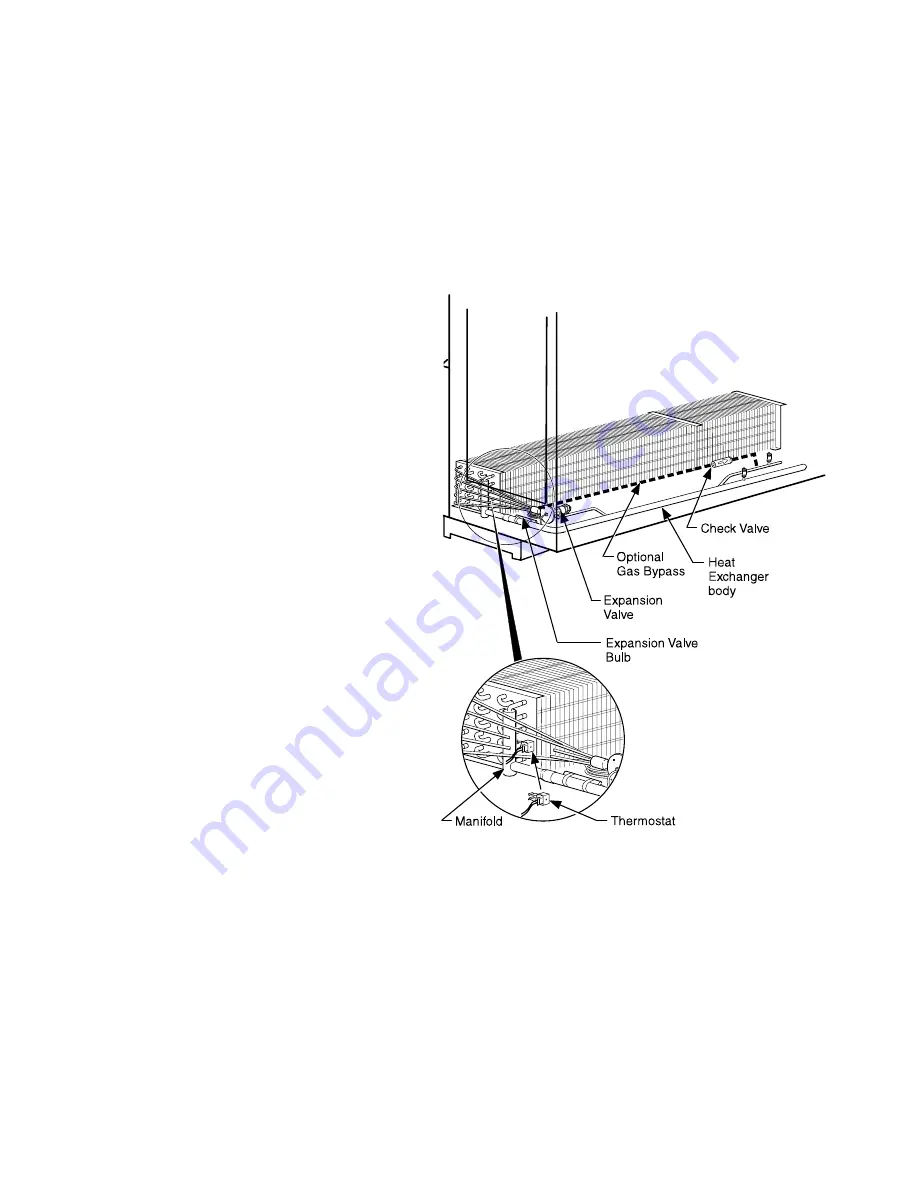
4-2
s
tart
up
P/N 0520677_W
U.S. & Canada 1-800-922-1919 • Mexico 1-800-890-2900 • WWW.HUSSMANN.COM
EXPANSION VALVE ADJUSTMENT
Expansion valves on Freedom cases are pre-
adjusted from the factory, but some adjustment
may be necessary to adjust for specific store
conditions. Before attempting to adjust valves,
make sure the evaporator is either clear or
only lightly covered with frost, and that the
merchandiser is within 10 deg F (6.5 deg C) of
its expected operating temperature. Adjust valves
as follows:
Method 1 (recommended): Attach a sensing
probe (either thermocouple of thermistor)
to the evaporator outlet, under the clamp
holding the expansion valve bulb. Attach
a pressure probe to the access valve on the
suction line. Measure superheat by subtracting
the saturation temperature at the measured
pressure from the measured outlet temperature.
Method 2: Attach two sensing probes.
Note:
When using high glide refrigerants (e.g.,
R-407A, R-448A), use the evaporator pressure
and subtract the dew point from the coil
outlet refrigerant temperature to measure the
superheat level.
Attach two sensing probes (either thermocouple
or thermistor) to the evaporator. Position one
under the clamp holding the expansion valve
bulb; securely tape the other to the coil inlet
line.
Some “hunting” of the expansion valve is
normal. The valve should be adjusted so that
during the hunting
the
greatest
Difference
between
the
two
probes
is
3–5
deg
f
(1.7–2.8
deg
c).
With this adjustment, during
a portion of the hunting the temperature
difference between the probes will be less than
3 deg F
(1.7
deg
c)
and at times 0.
Make adjustments of no more than
1
/
4
turn for
Balanced Port TEV and
1
/² turn at a time for
other valve models. Wait at least 15 minutes
before re checking the probe temperature or
making further adjustments.
Component Location in
RL / RM / RLN /
RLNI Models