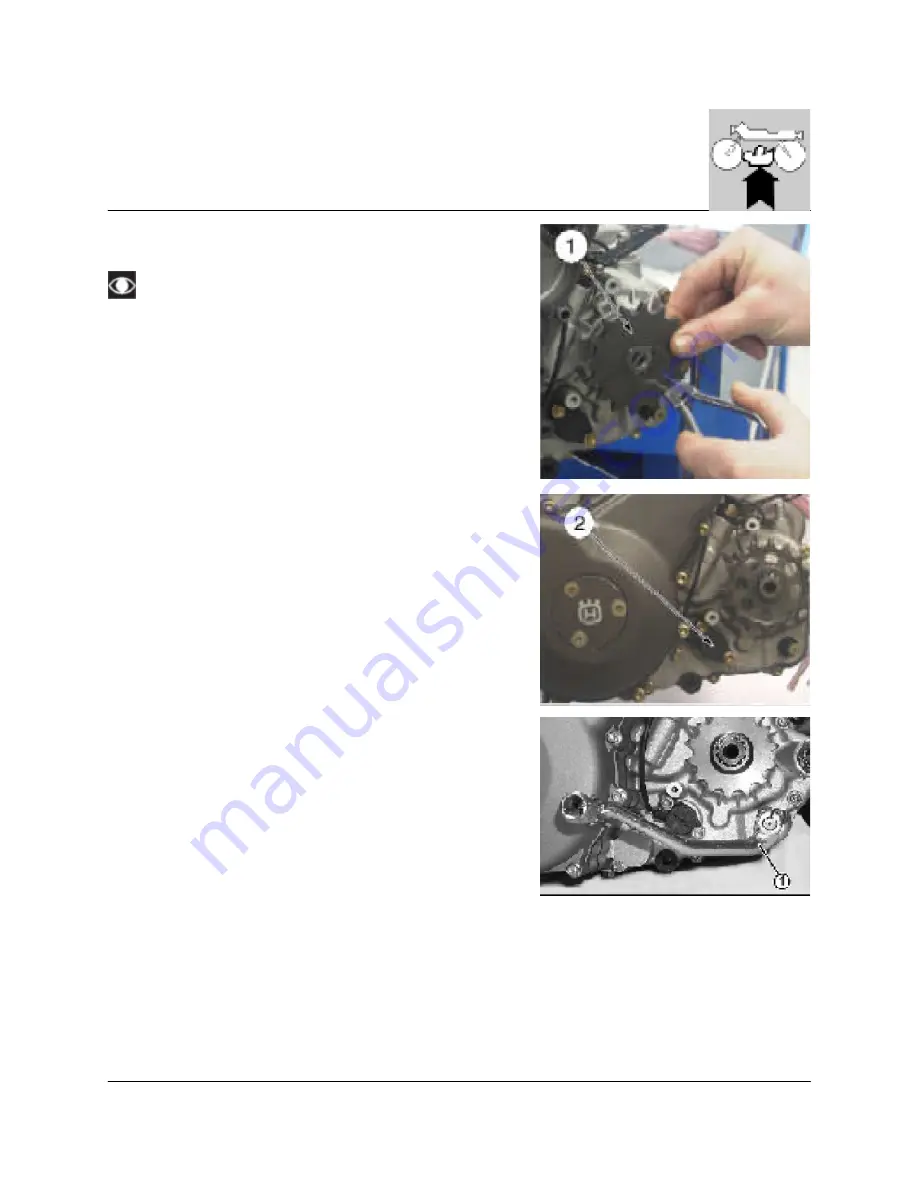
2 7
E N G IN E R E A S S E M B LY
R e a s s e m b ly o f re a r p in io n , n e u tra l s e n s o r a n d g e a r s h ift p e d a l
In sta ll th e re a r p in io n (1 ) w ith a n e w re ta in in g rin g .
P a y a tte n tio n to re a r p in io n (1 ) re a s s e m b lin g s e n s e : th e c ro w n in g
s id e h a s to b e tu rn e d to w a rd th e in s id e .
In sta ll th e n e u tra l se n so r (2 ) w ith its fa ste n in g scre w s (6 N m -0 ,6 K g m -4 .3 ft/
lb ).
In sta ll th e g e a r sh ift p e d a l (3 ) w ith its fa ste n in g scre w (9 N m -0 ,9 K g m -6 .5 ft/
lb ) in a cco rd a n ce w ith th e m a rk p re vio u sly d o n e .
A fte r th e e n g in e a sse m b ly, ch e ck th e va lve p la y a n d in sta ll th e sp a rk p lu g .
A fte r th e e n g in e a sse m b ly ch e ck th e va lve cle a ra n ce a n d in sta ll th e sp a rk
p lu g .
R e a sse m b le th e e n g in e o n th e fra m e , co n n e ctin g th e co o lin g a n d lu b rica tio n
circu its, th e e le ctric syste m a n d th e p a rts p re vio u sly re m o ve d .
Содержание SM 610 2006
Страница 1: ...1 W orkshop Manual SM 610 TE 610 2006 Part N 8000 A4640 04 2005 ...
Страница 4: ...4 W here not otherwise specified data and instructions refer to all m odels SM 610 TE 610 ...
Страница 6: ...6 ...
Страница 7: ...1 GENERAL Section ...
Страница 15: ...1 Section MAINTENANCE ...
Страница 19: ...1 TROUBLESHOOTING Section ...
Страница 25: ...1 SETTINGS AND ADJUSTMENTS Section ...
Страница 41: ...1 GENERAL OPERATIONS Section ...
Страница 53: ...1 ENGINE DISASSEMBLY Section ...
Страница 74: ...22 ...
Страница 75: ...1 ENGINE OVERHAULING Section ...
Страница 100: ...26 ...
Страница 101: ...1 ENGINE REASSEMBLY Section ...
Страница 106: ...6 ENGINE REASSEMBLY ...
Страница 110: ...10 ENGINE REASSEMBLY A 28m m 1 1 in M AIN SHAFT B 25m m 0 98 in AUXILIARY SHAFT ...
Страница 129: ...1 FRONT SUSPENSION Section ...
Страница 144: ...16 ...
Страница 145: ...1 REAR SUSPENSION Section ...
Страница 153: ...9 REAR SUSPENSION ...
Страница 158: ...14 REAR SUSPENSION L 234 5 237 5 m m 9 23 9 35 in ...
Страница 163: ...1 BRAKES Section ...
Страница 171: ...9 BRAKES Periodically check the connecting hoses A and B if the hoses are worn or cracked their replacem ent is advised ...
Страница 172: ...10 ...
Страница 173: ...1 ELECTRIC SYSTEM Section ...
Страница 176: ...4 ELECTRIC SYSTEM ...
Страница 179: ...7 ELECTRIC SYSTEM ...
Страница 197: ...25 ELECTRIC SYSTEM Fig 1 Fig 2 Fig 3 Fig 4 Fig 5 Fig 1 Fig 7 Fig 8 Fig 9 Fig 10 Fig 6 Fig 12 Fig 11 ...
Страница 202: ...30 ELECTRIC SYSTEM TE SM L H COM M UTATOR ...
Страница 205: ...1 ENGINE COOLING SYSTEM Section ...
Страница 208: ...4 ...
Страница 209: ...1 LUBRICATION CIRCUIT Section ...
Страница 211: ...1 SPECIFIC TOOLS Section ...
Страница 219: ...1 FRAME AND W HEELS Section ...
Страница 229: ...1 NOTES FOR USA CDN AUS MODELS Section ...