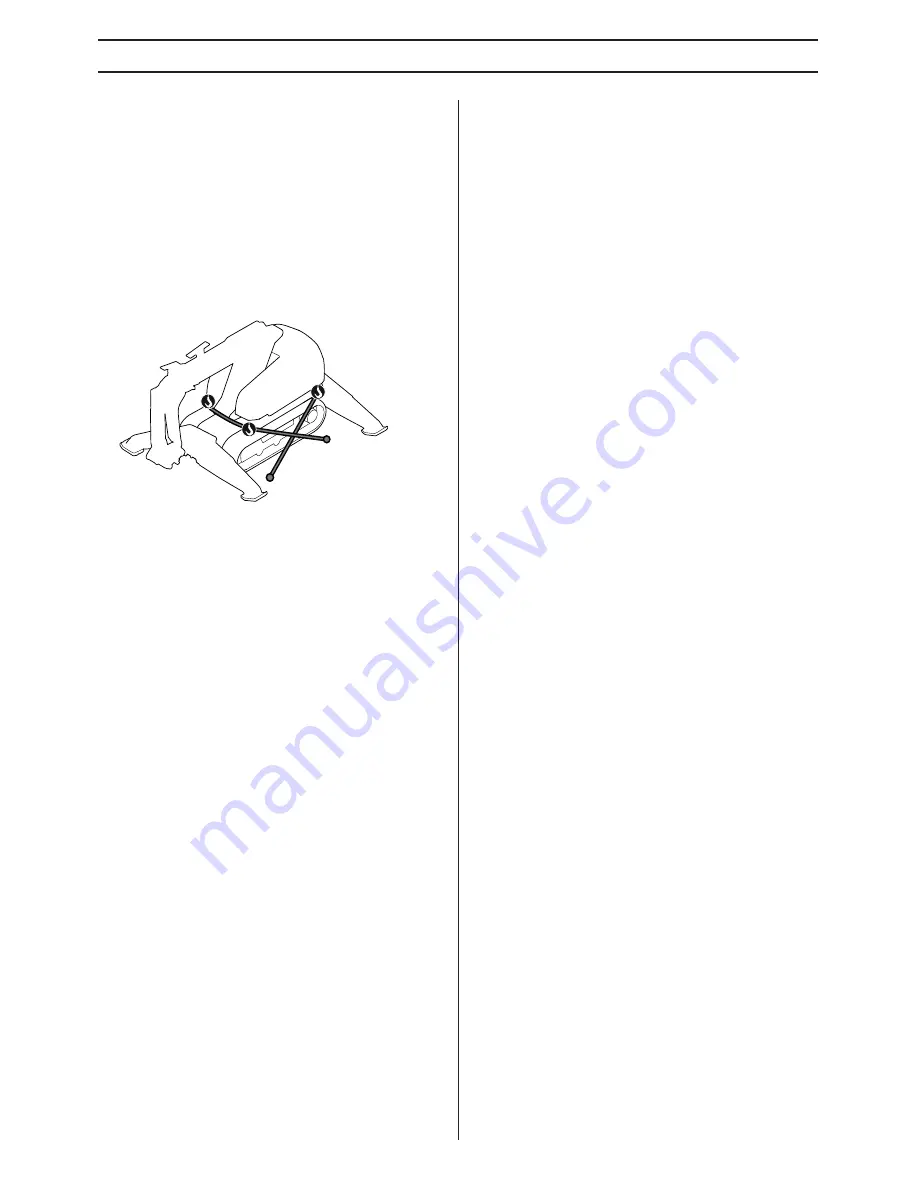
22 –
English
SAFETY INSTRUCTIONS
The machine’s position on the loading platform
•
Position the machine against the front edge of the
platform in order to reduce the risk of it sliding forward if
the vehicle brakes.
•
Manoeuvre the arm system so that it is resting against the
platform, positioned as low as possible. Extend the
outriggers without lifting the machine.
Securing the load
•
Secure the machine with approved tightening straps.
Ensure that no part of the machine are squashed or
damaged by the tightening straps. It is a good idea to
cover the machine.
•
Tools and other equipment must be secured with separate
tightening straps.
•
Regularly check that the load is secure during
transportation.
Storage
•
Remove the tool from the machine.
•
Retract the arm system to attain a centre of gravity that is
as low as possible and to save space.
•
Store the equipment in a lockable area so that it is out of
reach of children and unauthorized persons.
•
Store the machine and its equipment in a dry and frost
proof place.
•
The main switch on the machine can be locked with a
padlock to prevent unauthorised persons from starting the
machine.
Towing
The machine is not designed to be towed. When the machine
is depressurized, the drive motor’s parking brakes are
activated and the caterpillar tracks cannot rotate. Only tow the
machine if its position constitutes a risk and there is no other
solution. Tow it for the shortest possible distance.
•
If possible, retract the outriggers before towing the
machine in order to reduce the risk of them getting stuck
and being damaged.
•
To minimize the load on the towing device and mechanical
components, reduce the friction by preparing the route
that the machine is going to be towed.
•
If possible tow in the direction of the tracks.
•
Use a towing device intended for the particular load.
•
Parts can loosen during towing. Keep your distance!
Maintenance and service
Most accidents involving machines occur during trouble
shooting, service and maintenance as staff have to locate
themselves within the machine’s risk area. Prevent accidents
by being alert and by planning and preparing the work. You
can also refer to 'Preparations for maintenance and service”
in the 'Maintenance and service” section.
•
Never carry out repairs without having the necessary
expertise.
•
The user must only carry out the maintenance and service
work described in this Operator's Manual. More extensive
work must be carried out by an authorized service
workshop.
•
Use personal protective equipment as well as equipment
to mechanically secure machine components during
maintenance and service.
•
Only trained service personnel are permitted to intervene
in the electrical or hydraulic systems.
•
Set out clear signs to inform persons in the vicinity that
maintenance work is in progress.
•
If service operations or trouble shooting does not require
the machine to be switched on, the power cable must be
removed and positioned so that it cannot be connected by
mistake.
•
Ensure there is no current to the machine by removing the
power cable before opening or removing the electric
cabinet or any other component that contains electrical
current.
•
Pipe and hose couplings can remain pressurized despite
the motor being switched off and the power cable
disconnected. It must always be assumed that hydraulic
hoses are pressurized and they must be opened with
great care. Relieve the pressure on the arm system by
resting it on the ground and turn off the electric motor
before undoing the hoses.
•
Never try to stop hydraulic oil leaking from a broken hose
by hand. Finely dispersed hydraulic oil at high pressure
can permeate under the skin and cause very severe
injuries.
•
When dismantling machine parts, heavy components can
start moving or fall down. Secure moving parts
mechanically before loosening screw joints or hydraulic
hoses.
•
Use an approved lifting device to secure and lift heavy
machine parts.
•
Several components heat up during work with the
machine. Do not commence any servicing or
maintenance tasks until the machine has cooled.
•
Keep work area clean and well lit.
Cluttered or dark
areas invite accidents.
•
The machine’s movements can be defective if a terminal,
cable or hose is incorrectly assembled. Exercise caution
during test runs and be prepared to turn off the machine
immediately in the event of a fault.
Содержание DXR300
Страница 55: ...English 55 TECHNICAL DATA 4868 192 2368 93 5231 206 1818 72 ...
Страница 58: ......
Страница 59: ......
Страница 60: ... z X16 6y 2013 09 25 z X16 6y 1156172 26 GB Original instructions ...