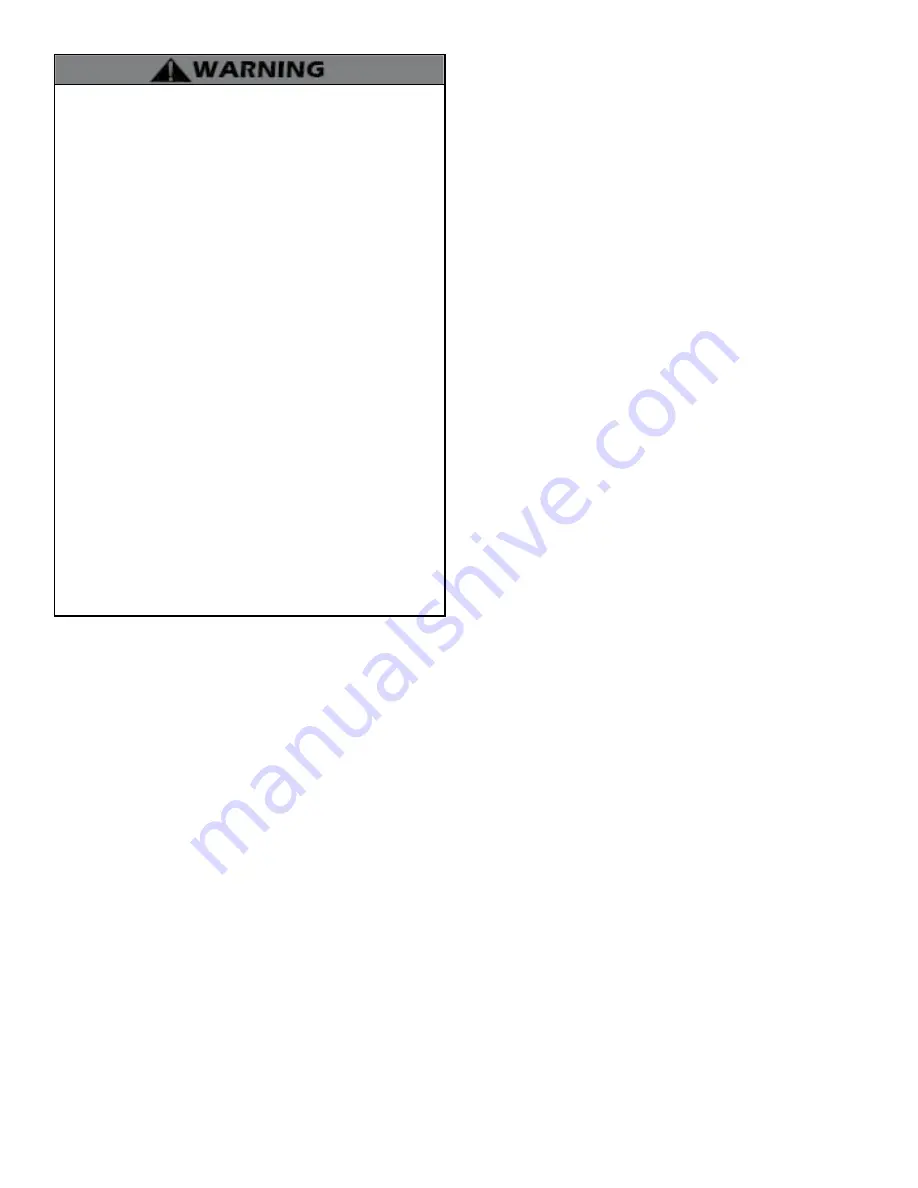
LP-314 Rev. 012 Rel. 003 Date 9.27.19
4
E. Temperature and Pressure Relief Valve for DHW
H. Hydronic Heating Module Piping
I. Pressure Relief Valve for the Hydronic System
J. Hydronic Expansion Tank and Make-Up Water
K. Hydronic Heating Module System Piping
L. Hydronic Heating Module Output
B. Approved Materials for Exhaust Vent and Intake Pipe
C. Additional Requirements for Installation in Canada
D. Exhaust Vent and Intake Pipe Location
E. Exhaust Vent and Intake Pipe Sizing
G. Exhaust Vent and Intake Pipe Installation
1. Direct Vent Installation of Exhaust and Intake
2. Venting Through an Existing System
3. Power Venting, Indoor Combustion Air in Confined or Unconfined
Space
E. Optional 0-10 Volt Building Control Signal
3. LP (Liquid Propane) Gas Pipe Sizing
D. Checking Gas Pressure at the Appliance for Proper Operation
B. Fill and Purge Hydronic Heating Loop
C. Purge Air from Hydronic Heating Module
D. Using the Control to Assist in Purging System Loops
E. Programming the Total System Control
Part 10 - Start-Up Procedures for the Installer
C. Programming the System Setting
D. System Setting Program Navigation
F. Resetting the Maintenance Schedule
Table of Contents
Part 1 - General Safety Information
C. When Servicing the Appliance
F. High Elevation Installations
G. Water Temperature Adjustment
Part 3 - Prepare the Appliance
C. Clearances for Service Access
D. Residential Garage and Closet Installations
E. Exhaust Vent and Intake Pipe
1. Direct Vent of Exhaust and Intake
2. Power Venting, Indoor Combustion Air in Confined or Unconfined Space
G. Prevent Combustion Air Contamination
H. Removing an Appliance from a Common Vent System
I. Water Chemistry Requirements
Part 4 - Domestic Hot Water and Hydronic Piping
1. System Domestic Water Piping
2. Appliance Domestic Water Piping
From the Uniform Plumbing Code 2000 - Section 510 -
Protection From Damage
1. Appliances generating a glow, spark or flame capable of igniting
flammable vapors may be installed in a garage, provided the pilots,
burners or heating elements and switches are at least eighteen (18)
inches (457 mm) above the floor level.
2. Where such appliances installed within a garage are enclosed
in a separate, approved compartment having access only from
outside of the garage, such appliances may be installed at floor level
provided the required combustion air is also taken from the exterior
of the garage. Fuel burning appliances having sealed combustion
chambers need not be elevated.
3. All appliances installed in areas where they may be subjected to
mechanical damage shall be suitably guarded against such damage
by being installed behind adequate barriers or by being elevated or
located out of the normal path of a vehicle using any such garage.
4. In seismic zones 3 and 4, appliances shall be anchored or strapped
to resist horizontal displacement due to earthquake motion.
Strapping shall be at points within the upper one-third (1/3) and
lower one-third (1/3) of its vertical dimensions. At the lower point, a
minimum distance of four (4) inches (102 mm) shall be maintained
above the controls with the strapping.
5. An appliance supported from the ground shall rest on level
concrete or other approved base extending not less than three (3)
inches (76 mm) above the adjoining ground level.
6. When an appliance is located in an attic, attic-ceiling assembly,
floor-ceiling assembly, or floor-subfloor assembly where damage
may result from a leaking appliance, a watertight pan of corrosion
resistant materials shall be installed beneath the appliance with
a minimum three-quarter (3/4) inch (20 mm) diameter drain to an
approved location.