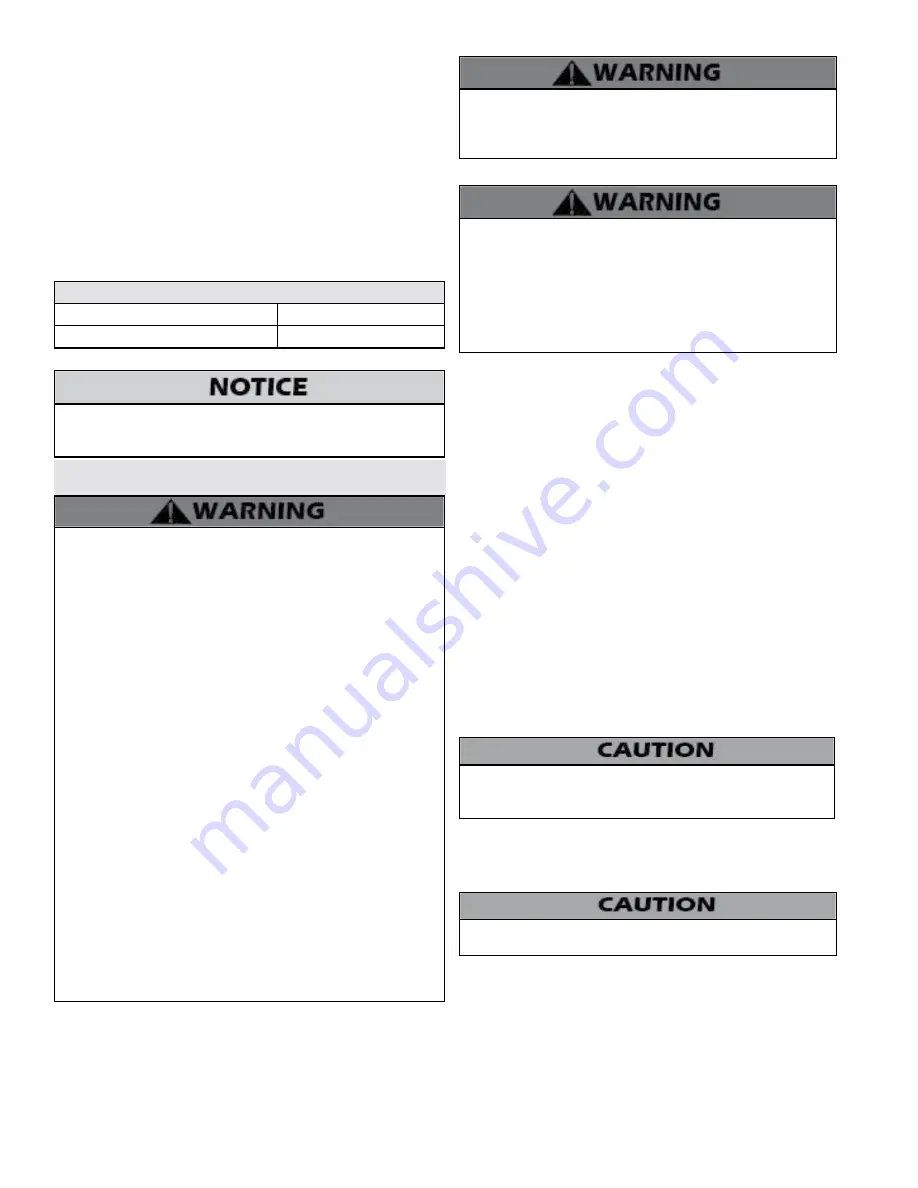
LP-314 Rev. 012 Rel. 003 Date 9.27.19
36
D. Checking Gas Pressure at the Appliance for Proper
Operation
NOTE:
Refer to Figure 39 when checking gas pressure.
1. The appliance and its individual shutoff valve must be disconnected
from the gas supply piping system during any pressure testing of the
system at pressures greater than ½ psi (3.5 kPa).
2. The appliance must be isolated from the gas supply piping system
by closing its individual manual shutoff valve during any pressure
testing of the gas supply piping system at test pressures equal to or
less than ½ psi (3.5 kPa). Loosen the screw on the pressure tap inlet to
attach a manometer and check the gas inlet pressure.
The minimum and maximum inlet gas line pressures must meet the
requirements shown in Table 22.
Natural or LP Gas
Minimum Pressure
3.5” WC
Maximum Pressure
14”WC
Table 12 - Gas Pressure Requirements
Do not fire (operate) the appliance until all connections have been
completed and the heat exchanger is filled with water. Doing so will
damage the appliance and void the warranty.
Part 9 - Start-Up Preparation
FOR YOUR OWN SAFETY READ BEFORE OPERATING
1. This appliance does not have a pilot. It is equipped with an ignition
device which automatically lights the burner. Do not try to light the
burner by hand.
2. BEFORE OPERATING: Smell all around the appliance area for gas.
Be sure to smell next to the floor because some gas is heavier than
air and will settle on the floor.
WHAT TO DO IF YOU SMELL GAS
• Do not try to light any appliance.
• Do not touch any electric switch, do not use any phone in your
building.
• Immediately call your gas supplier from a neighbor’s phone.
Follow the gas suppliers’ instructions.
• If you cannot reach your gas supplier, call the fire department.
• Turn off the gas shutoff valve (located outside the appliance)
so that the handle is crosswise to the gas pipe. If the handle will
not turn by hand, don’t try to force or repair it, call a qualified
service technician. Force or attempted repair may result in a
fire or explosion.
4. Do not use this appliance if any part has been under water.
Immediately call a qualified service technician to inspect the
appliance and to replace any part of the control system and any gas
control that has been damaged.
5. The appliance shall be installed so the gas ignition system
components are protected from water (dripping, spraying, rain, etc.)
during appliance operation and service (circulator replacement,
condensate trap, control replacement, etc.)
Failure to follow these instructions could result in property damage,
serious personal injury, or death.
Ensure the appliance is full of water before firing the burner.
Failure to do so will damage the appliance. Such damage IS NOT
covered by warranty, and could result in property damage, serious
personal injury, or death.
A. Fill and Purge DHW
The power must remain off until the potable water side of the appliance
is fully purged of air. To purge the tank, turn on the cold water feed and
open a faucet at the highest point of the system. Observe filling of the
tank and inspect for any leaks in the system which may occur and need
to be repaired. Shut off faucet once all evidence of air is purged from
the water stream.
B. Fill and Purge Hydronic Heating Loop
1. Local codes may require back flow preventer or actual disconnect
from city water supply.
2. The power must remain off until the hydronic heating loop is fully
purged of air.
3. Determine freeze protection fluid quantity using total system
water content of 1/2 gallon. Remember to include expansion tank
water content and follow fluid manufacturer’s instructions.
4. When using freeze protection fluid with automatic fill, install a
water meter to monitor water make-up. Freeze protection fluid may
leak before the water begins to leak, causing concentration to drop,
reducing the freeze protection level.
5. Manually close any automatic air vents and any drain valves in the
hydronic system loop.
6. Fill the system to correct pressure after ensuring the water quality
meets the water quality standards outlined within this manual. The
correct pressure will vary with each application.
a. Typical system pressure is 15 PSI.
b. Pressure will rise when the hydronic module starts to heat with
the heated water from the domestic side of the system. Operating
pressure must never exceed the relief valve pressure setting of 30
psi.
c. At initial fill and during start-up and testing, check system
thoroughly for any leaks. Repair all leaks before proceeding further.
Never use automotive or standard glycol antifreeze, or ethylene
glycol made for hydronic systems. Use only freeze-prevention
fluids certified by fluid manufacturer as specified for use with
stainless steel hydronic heating module heat exchanger and
verified in fluid manufacturer’s literature. Thoroughly clean and
flush any system that has used glycol before connecting to the
stainless steel hydronic heating module heat exchanger. Provide
MSDS material data safety sheet on fluid used to owner.
Eliminate all system leaks. Continual fresh make-up water will
reduce the hydronic heating module heat exchanger ability to
effectively transfer heat and reduce performance.
7. The system may have residual substances that could affect
water chemistry. After the system has been filled and leak tested,
verify that water pH and chloride concentrations are acceptable by
sample testing.
It is important that you purge the system of air to avoid damage to
the modulating pump.
C. Purge Air from Hydronic Heating Module
1. Connect to a purge and drain valve location (shown in piping
details) and route hose to an area where water can drain and be
seen.
2. Close the ball valves below the purge and drain valve.
3. Close zone isolation valves.
4. Open quick-fill valve on make-up water line.
5. Open purge valve.
6. Open the isolation valves one zone at a time. Allow water to run
through the zone and push out air. Run until no noticeable air flow