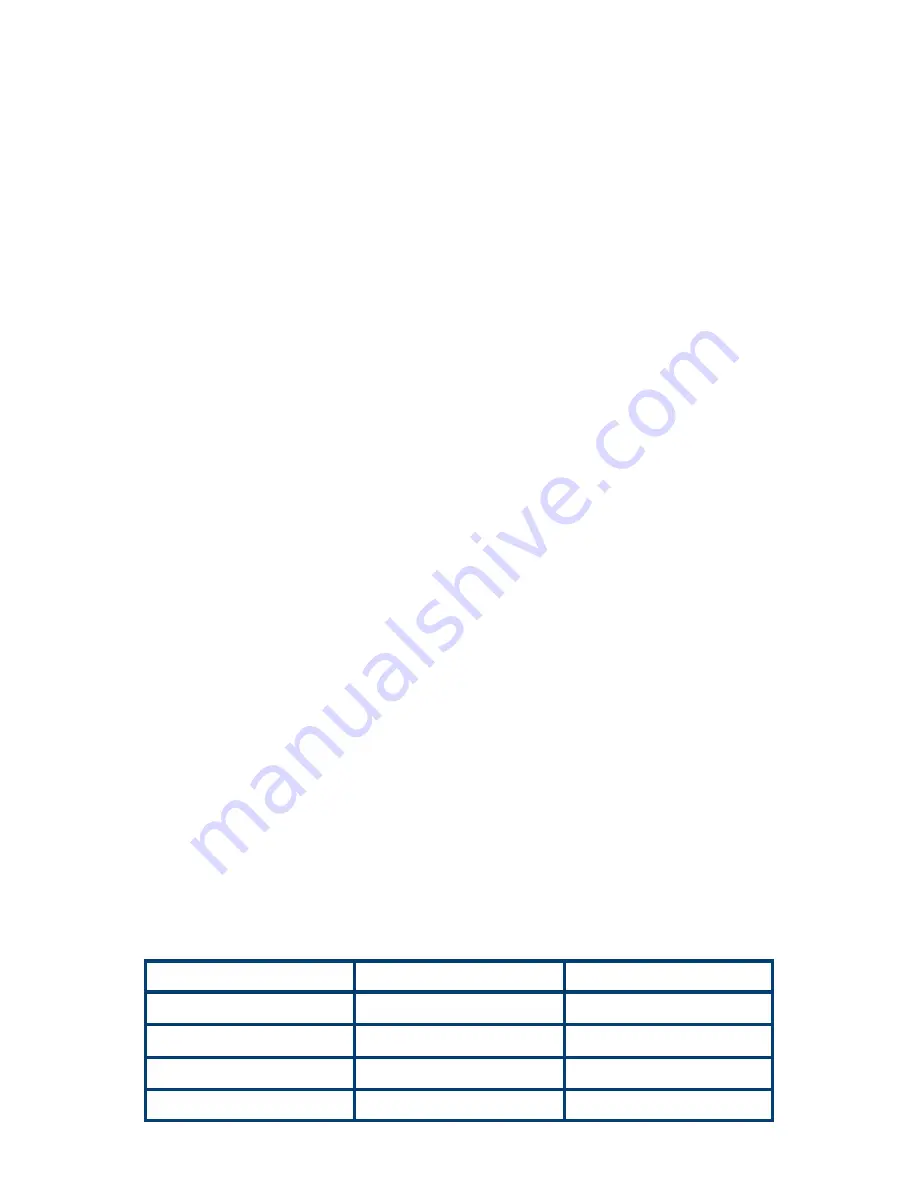
15
j) Pulse in Stick (Square Wave Only)
Advantages of Pulse Welding
Pulse welding includes ALL of the following advantages, but
not all at the same time
. At a later point in the manual, we
cover, in more detail, suggested settings regarding how, when, and where certain situations apply.
Visually spatter free (MIG & TIG only, though still reduced spatter when stick welding)
Higher travel speeds
Deeper penetration
Less heat input, which equals less material distortion
Ability to weld thinner material than you could without pulse
Superior control of the weld puddle, especially when welding out of position
Easily join materials of differing thicknesses
Better gap bridging when welding materials with poor fit up
Ability to make leak-tight welds
Improved bead appearance
Ability to use one size bigger welding rod than normal
Weld on thinner material without burning through
Easier for beginner welders
Disadvantages of Pulse Welding
Pulse welding can interfere with sensitive electronics like pacemakers and auto-darkening welding helmets
Low pulse frequencies (less than 1.5Hz) can be perceived as unpleasant, sound-wise, by the operator (TIG and Stick
only)
Common Stick Welding Electrode Types and Descriptions
6010—Rod with a cellulosic coating, fast freeze puddle, deep penetration, slag can be hard to remove, less elongation of
welds, not the most attractive welds, may present some hydrogen cracking. However, rod runs in all positions, including
vertical up and down. Also forgiving for some contamination of the parent metal. An excellent choice for root passes.
6013—Rod with a titania potassium coating that runs on old and simple AC (alternating current) stick welders. Typically
referred to as the farmer’s rod.
7014—Rod with properties similar to 7018, but also designed to run on older, simpler stick welders.
7018—Rod with a low hydrogen coating that flows nicely. Probably the most popular rod in today’s market. Builds a
thick, easy to remove slag layer on top of the weld, medium penetration, excellent bead appearance, puddle stays wet
and fluid much longer than 6010, higher tensile strength than 6010. A good choice for the maintenance welder and even
to do x-ray quality structural welds.
The rods listed above represent the most common types of rods available today. However, an almost endless selection of
various rods exist. We simply cannot cover all rod types in the manual. Since 7018 is probably the most popular welding
rod available today, please find a few pointers below.
How do you find the right amperage when you lose the box?
The
general rule of thumb with 7018: For every 0.001” of welding rod diameter, you need about 1 amp.
What does this
mean? Will these numbers be a perfect fit for every rod manufacturer and every position you weld 7018 rod in?
No, but the numbers get you really close.
Rod Diameter Fraction
Rod Diameter Decimal
Required Amperage
3/32”
0.09375” rounded to 0.094
94 amps
1/8”
0.125”
125 amps
5/32”
0.15625” rounded to 0.156”
156 amps
3/16”
0.1875” rounded to 0.188”
188 amps
Fig. 8
Содержание Invertig 313
Страница 6: ...6 Fig 1 ...
Страница 33: ...33 12 WIRING DIAGRAM Invertig 400 AC DC ONLY ...
Страница 34: ...34 13 EXPLODED VIEW INVERTIG 400 AC DC ONLY ...