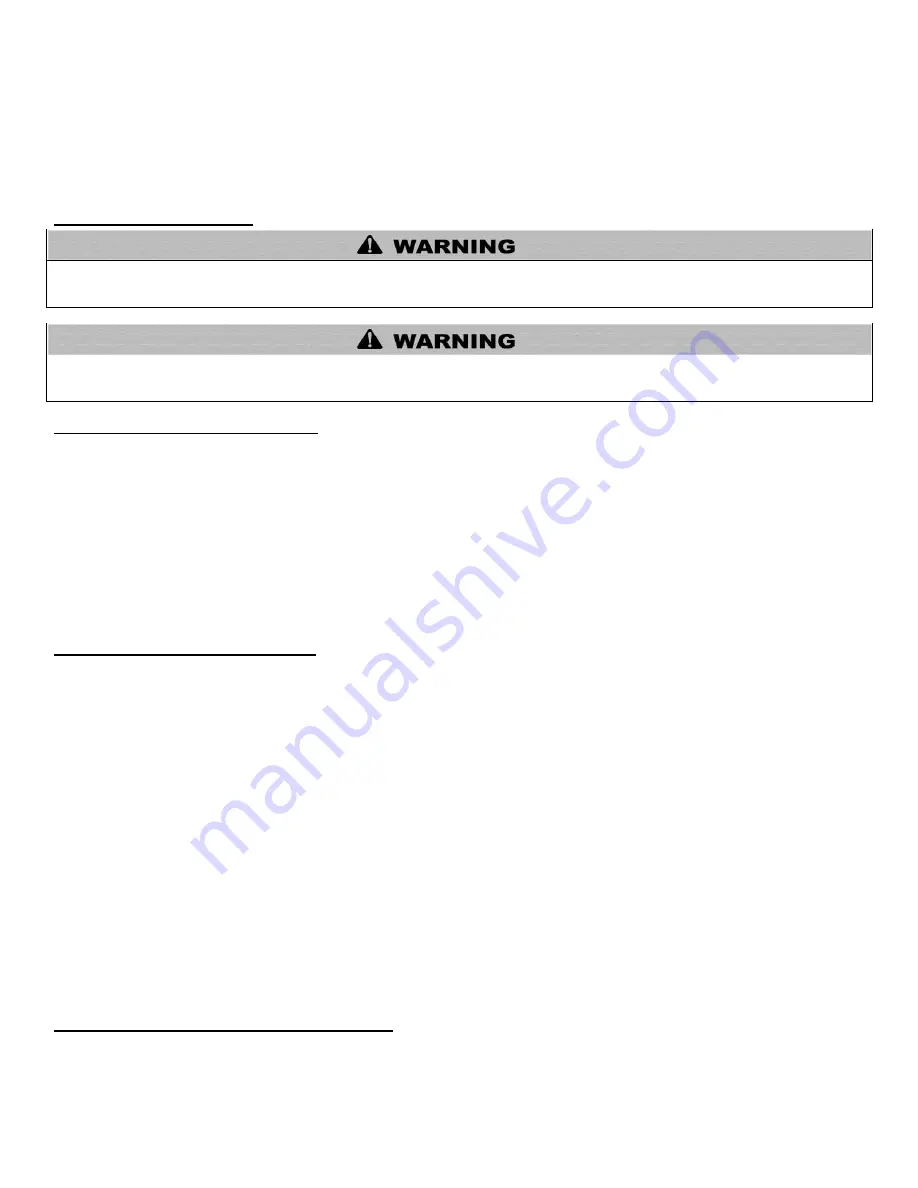
60
LP-185 Rev. 9.9.14
g. Close the quick-fill water valve and purge valve and remove the hose. Open all isolation valves. Watch that system pressure
rises to correct cold-fill pressure.
h. After the system has operated for a while, eliminate any residual air by using the manual air vents located throughout the
system.
i. If purge valves are not installed in system, open manual air vents in system one at a time, beginning with lowest floor. Close
vent when water squirts out. Repeat with remaining vents.
j. Refill to correct pressure.
E. CHECK FOR GAS LEAKS
Before starting the boiler, and during initial operation, smell near the floor and around the boiler for gas odorant or any unusual odor.
Remove boiler front door and smell interior of boiler enclosure. Do not proceed with startup if there is any indication of a gas leak.
Repair any leak at once.
Propane boiler only
– Your propane supplier mixes an odorant with the propane to make its presence detectable. In some instances,
the odorant can face, and the gas may no longer have an odor. Before startup (and periodically thereafter), have the propane supplier
verify the correct odorant level in the gas.
F. CHECK THERMOSTAT CIRCUIT(S)
1. Disconnect the two external wires connected to the boiler thermostat terminals (low voltage terminal strip terminals 5 and 6).
2. Connect a voltmeter across these two incoming wires. Close each thermostat, zone valve and relay in the external circuit one at a
time and check the voltmeter reading across the incoming wires.
3. There should NEVER be a voltage reading.
4. If a voltage does occur under any condition, check and correct the external wiring. (This is a common problem when using 3-wire
zone valves.)
5. Once the external thermostat circuit wiring is checked and corrected if necessary, reconnect the external thermostat circuit wires to
boiler low voltage terminal strip. Allow the boiler to cycle.
G. CHECK CONDENSATE REMOVAL
1. This a high efficiency condensing boiler, therefore, the unit has a condensation drain. Condensate is nothing more than water vapor,
derived from combustion products, similar to an automobile when it is initially started. The condensation is slightly acidic (typically with
pH of 3 to 5) and must be piped with the correct materials. Never pipe the condensate using steel, copper, brass or other materials that
will be subject to corrosion. Plastic PVC or CPVC pipe are the only approved materials. A condensate filter, if required by local
authorities, can be made up of lime crystals marble or phosphate chips that will neutralize the condensate. This may be done by the
installer or you may purchase a condensate neutralizer from HTP (p/n 7450P-218).
2. The boiler is equipped with a ¾
” pipe connection that runs the condensation line to a local drain. It is very important that the
condensate line is sloped away from the boiler and down to a suitable inside drain. If the condensate outlet is lower than the drain, you
must use a condensate removal pump, available at HTP (#554200). This pump is equipped with two leads that can be connected to an
alarm or another type of warning device to alert residents of a condensate overflow, which, if not corrected, could cause property
damage.
3. The boiler is equipped with an internal vent on the top plug connection to assure adequate flow of condensate. This vent should
never be blocked.
4. If a long horizontal run is used, it may be necessary to create a second vent to prevent a vacuum lock in the condensate line. Do not
expose the condensate to freezing temperatures.
5. Do not expose the condensate to freezing temperatures.
6. It is very important you support the condensation line to assure proper drainage.
H. FINAL CHECKS BEFORE STARTING BOILER
1. Read Startup Procedures within this manual for proper steps to start boiler. (See Startup Report to record steps for future reference.)
2. Verify the boiler and system are full of water and all system components are correctly set for operation.
3. Fill condensate trap with water.
Содержание 140M
Страница 12: ...12 LP 185 Rev 9 9 14 Figure 1 Dimensions T 50M T 80M 80M ...
Страница 13: ...13 LP 185 Rev 9 9 14 Figure 2 Dimensions 140M 199M 399M ...
Страница 48: ...48 LP 185 Rev 9 9 14 I DIAGRAMS FOR SIDEWALL VENTING Figure 25 Venting ...
Страница 49: ...49 LP 185 Rev 9 9 14 Figure 26 Sidewall Venting ...
Страница 50: ...50 LP 185 Rev 9 9 14 J DIAGRAMS FOR VERTICAL VENTING Figure 27 Vertical Venting ...
Страница 55: ...55 LP 185 Rev 9 9 14 Figure 29 ...
Страница 70: ...70 LP 185 Rev 9 9 14 Figure 31 ...
Страница 71: ...71 LP 185 Rev 9 9 14 Figure 32 ...
Страница 72: ...72 LP 185 Rev 9 9 14 Figure 33 ...
Страница 73: ...73 LP 185 Rev 9 9 14 Figure 34 ...
Страница 74: ...74 LP 185 Rev 9 9 14 Figure 35 ...
Страница 75: ...75 LP 185 Rev 9 9 14 Figure 36 ...
Страница 78: ...78 LP 185 Rev 9 9 14 ...
Страница 79: ...79 LP 185 Rev 9 9 14 ...
Страница 80: ...80 LP 185 Rev 9 9 14 MAINTENANCE NOTES ...