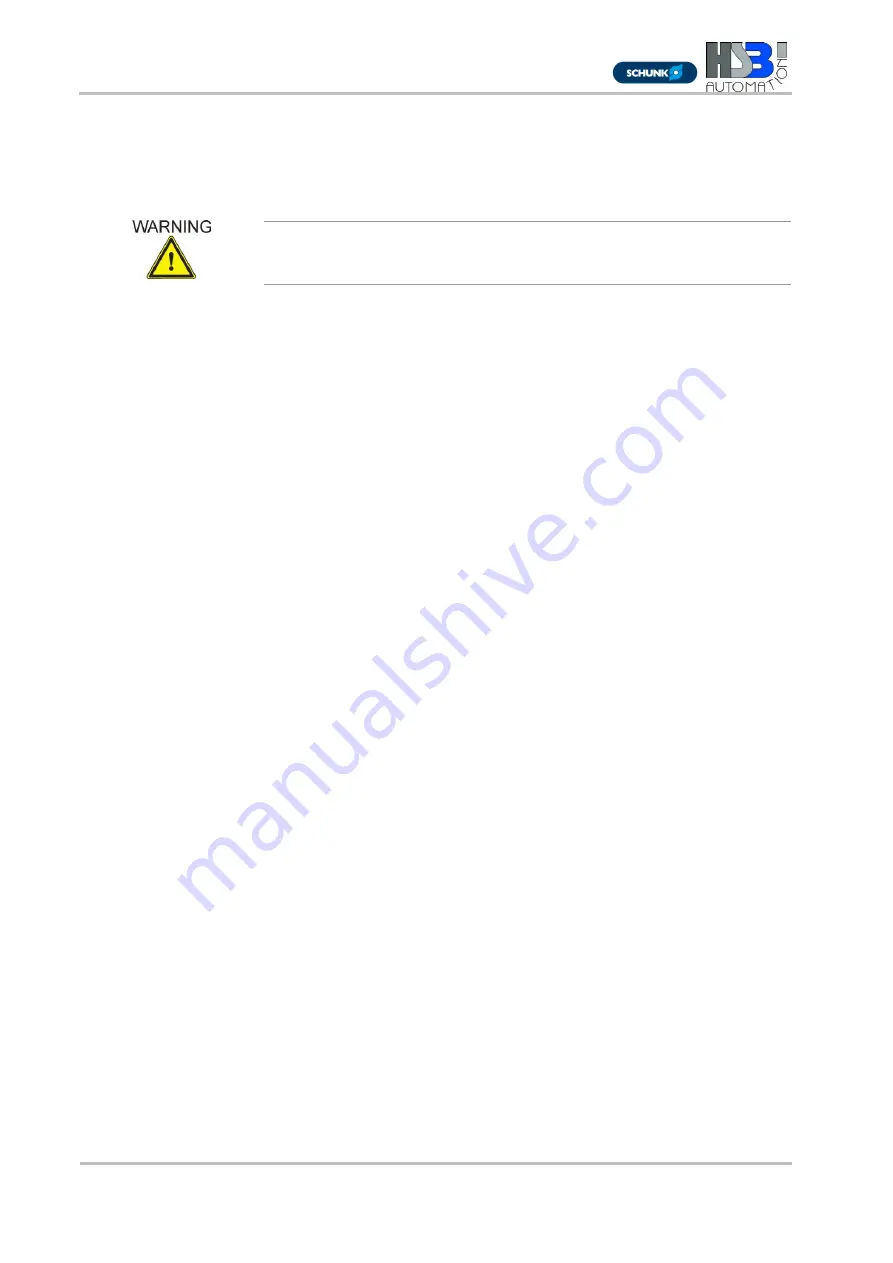
Shutdown
26
2022-09-01
FM 239 MuW Beta Type Z Rev.01
distributed by
9
Shutdown
Risk of personal injury or damage to other system components
caused by falling system components.
Only authorised specialist personnel may disassemble the linear unit.
1.
Cut the power to the machine/line.
2.
Dismantle the drive from the linear unit.
3.
Detach the linear unit from the machine/line.
Содержание Beta 100-D-ZSA
Страница 2: ......