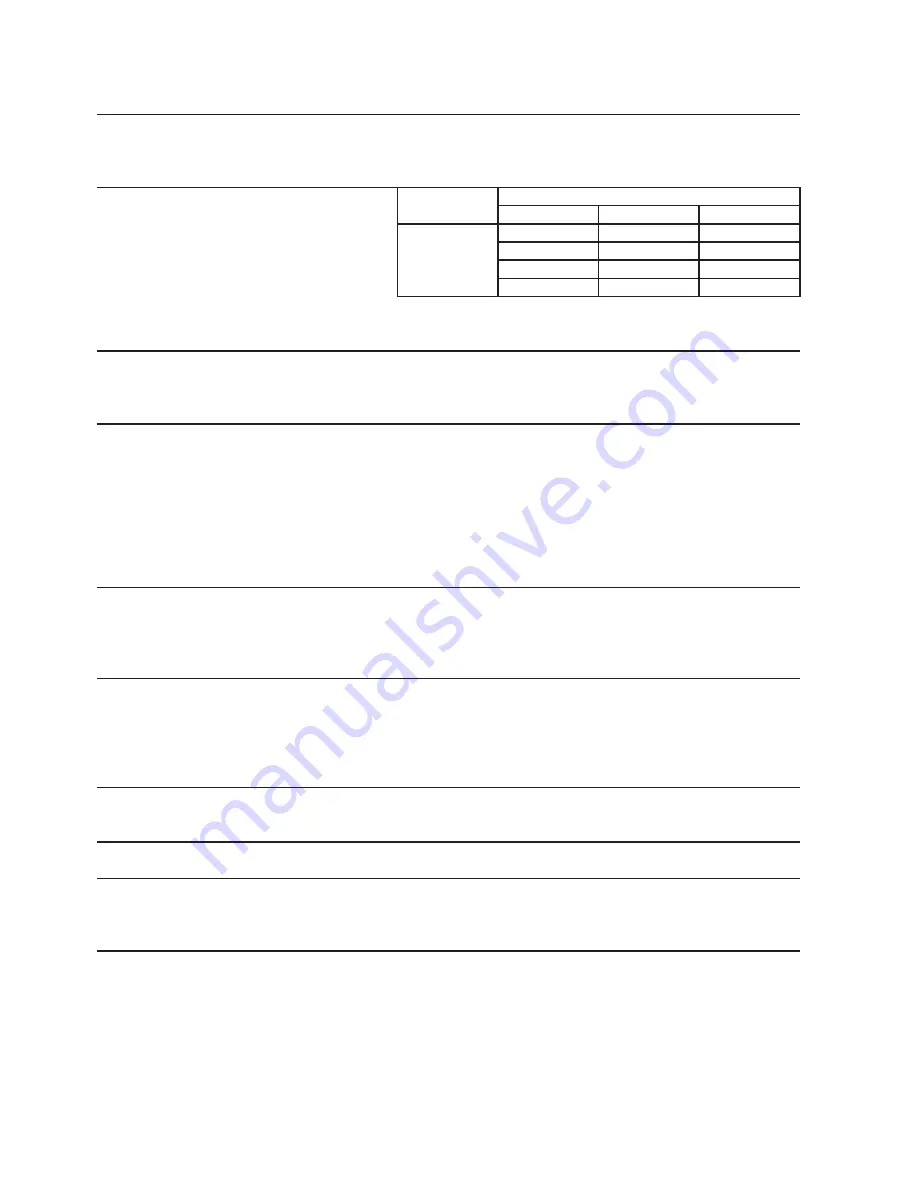
4
[d] KM-151BWH
AC SUPPLY VOLTAGE
115/60/1
AMPERAGE
6.8A ( 5 Min. Freeze AT 104°F / WT 80°F )
MINIMUM CIRCUIT AMPASITY
15A
MAXIMUM FUSE SIZE
15A
APPROXIMATE ICE PRODUCTION
Ambient
WATER TEMP. (°F)
PER 24 HR.
Temp.(°F)
50
70
90
lbs./day ( kg/day )
70
*146 (66)
141 (64)
136 (62)
Reference without *marks
80
142 (65)
135 (61)
131 (59)
90
141 (64)
*130 (59)
125 (57)
100
141 (64)
129 (58)
*121 (55)
SHAPE OF ICE
Crescent Cube
ICE PRODUCTION PER CYCLE
2.75 lbs. (1.25 kg) , 130 pcs.
APPROXIMATE STORAGE CAPACITY
78 lbs. (36 kg)
ELECTRIC & WATER CONSUMPTION
90/70°F
70/50°F
ELECTRIC W (kWH/100 lbs.)
395(7.3)
390(6.5)
POT. WATER gal./24HR (gal./100 lbs.)
29(25.0)
52(36.0)
COND. WATER gal./24HR (gal./100 lbs.)
181(140)
103(71)
EXTERIOR DIMENSIONS (WxDxH)
23.75" x 28" x 39" (603 x 712 x 990 mm)
Including 6" legs
EXTERIOR FINISH
Stainless Steel, Galvanized Steel (Rear)
WEIGHT
Net 121 lbs. (55 kg), Shipping 154 lbs. (70 kg)
CONNECTIONS - ELECTRIC
Cord Connection
- WATER SUPPLY
Inlet
1/2" FPT
- DRAIN
Outlet
3/4" FPT
CONDENSER WATER
Inlet
1/2" FPT
Outlet
1/2" FPT
CUBE CONTROL SYSTEM
Float Switch
HARVESTING CONTROL SYSTEM
Hot Gas and Water, Thermistor and Timer
ICE MAKING WATER CONTROL
Timer Controlled. Overflow Pipe
COOLING WATER CONTROL
N/A
BIN CONTROL SYSTEM
Mechanical Level Switch with Delay
COMPRESSOR
Hermetic, Model QA125K29CAU6-E0GS
CONDENSER
Water-Cooled, tube type
EVAPORATOR
Vertical type, Stainless Steel and Copper
REFRIGERANT CONTROL
Thermostatic Expansion Valve
REFRIGERANT CHARGE
R134a, 10.7 oz. (290g)
DESIGN PRESSURE
High 250PSIG, Low 150PSIG
P.C. BOARD CIRCUIT PROTECTION
High Voltage Cut-out ( Internal )
COMPRESSOR PROTECTION
Auto-reset Overload Protector ( Internal )
LOW WATER PROTECTION
Float Switch
ACCESSORIES -SUPPLIED
Ice Scoop, 6" leg 4 pcs
ACCESSORIES -REQUIRED
N/A
OPERATING CONDITIONS
VOLTAGE RANGE
104 - 127 V
AMBIENT TEMP.
45-100°F
WATER SUPPLY TEMP.
45- 90°F
WATER SUPPLY PRESSURE
10-113 PSIG
DRAWING NO. (DIMENSION)
372097
We reserve the right to make changes in specifications and design without prior notice.
Содержание KM-61BAH
Страница 16: ...11 ...
Страница 30: ...25 2 WIRING DIAGRAM a KM 61BAH ...
Страница 31: ...26 b KM 101BAH ...
Страница 32: ...27 c KM 151BAH KM 151BWH ...
Страница 83: ...78 Water Supply Inlet 1 2 FPT Drain Outlet 3 4 FPT Fig 34 KM 61BAH KM 101BAH KM 151BAH ...