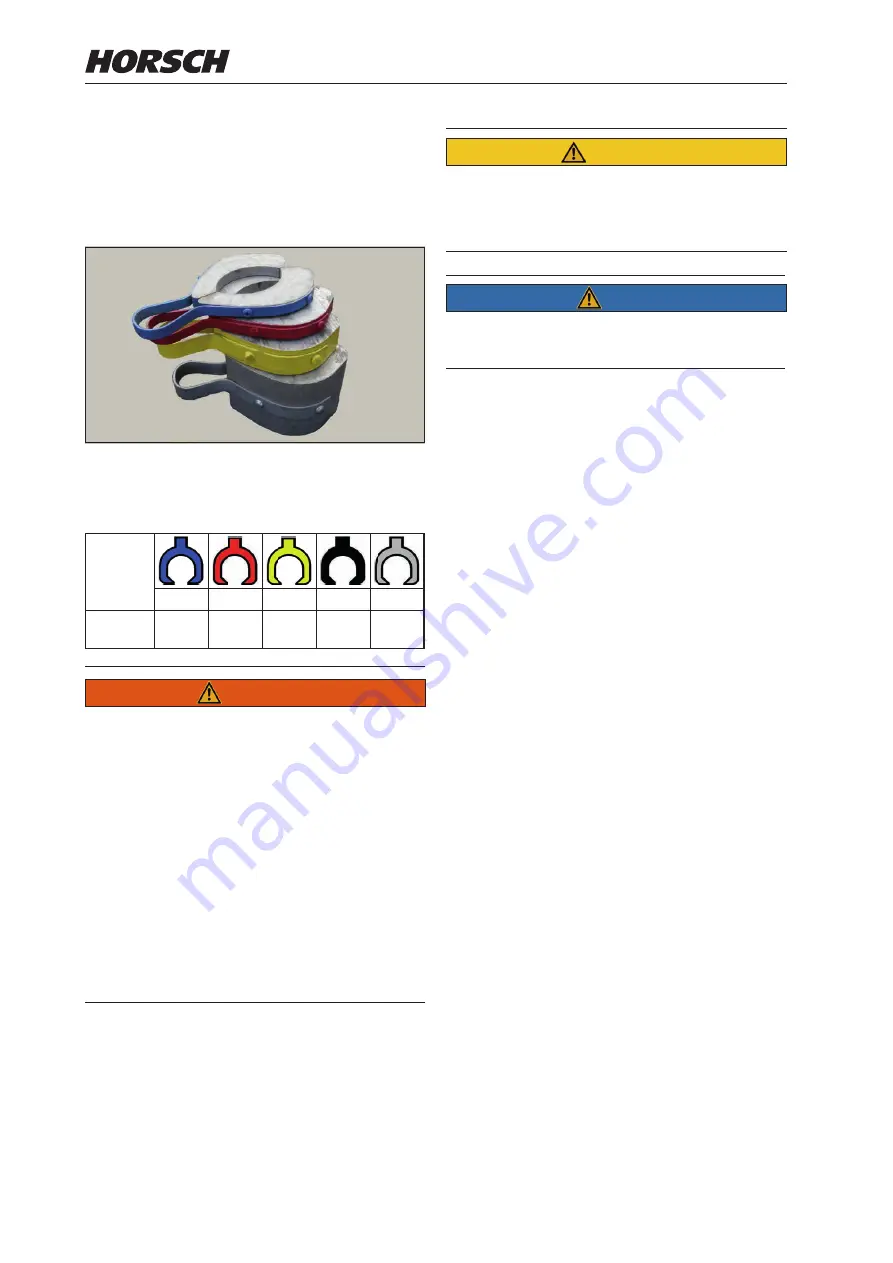
Aluminium
clips
The aluminium clips are placed on the piston
rods of hydraulic cylinders, depending on the
operating states, see chapter
Operation
.
Different aluminium clips
The thickness of the clips differs according to
colour:
Colour
blue
red
yellow black
silver
Thick-
ness
7 mm
10 mm 19 mm 30 mm 50 mm
WARNING
Risk of injury on the hydraulic cylinders!
Limbs may be pinched or crushed by uninten-
tional retraction of the piston rods.
¾
When attaching or removing the clips the
machine must be parked with the parking
brake pulled.
Nobody may be about in the area of the tractor
cab at this time.
¾
Lock control units mechanically or electrically,
depending on the version.
¾
Make sure when placing or removing clips
that the control units are not operated by any
other person.
CAUTION
Danger of damage to the packer frame.
¾
Depending on the design, do
not
remove any
fixed clips or depth limitations!
NOTE
¾
Pay attention to the ratio on the machine, see
Depth setting
.
38
39