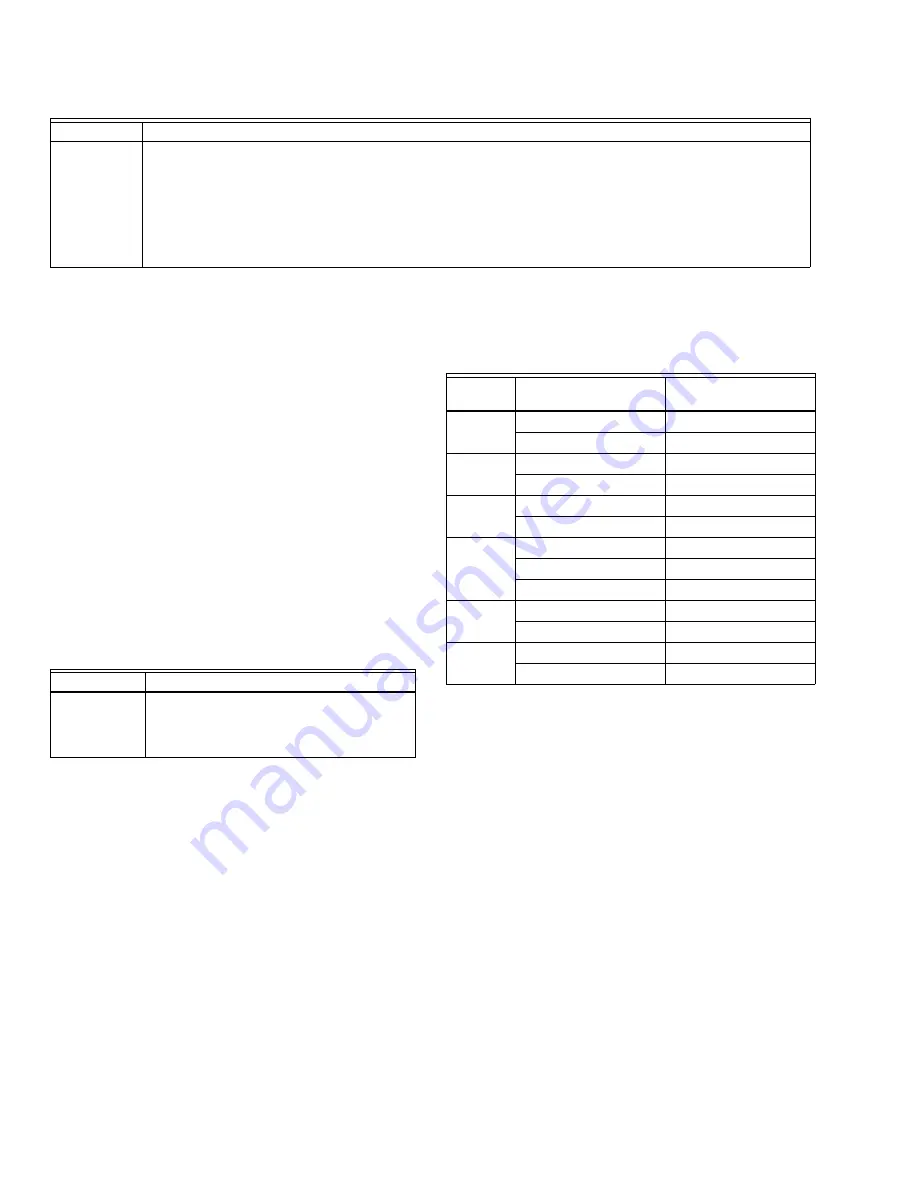
WEBVISION™
95-7769—01
72
HYD Wiring
Purpose
To display the wiring diagram for the Hydronic controller.
Mode
Configuration can be performed with the wizard Off-line or
On-line.
Procedure
1.
Click the
Wiring
button on the left pane to open the
Wiring Configuration
page.
2.
Enter information into available fields.
3.
Click
Commit
to save the settings or
Reset
to revert to
the last saved settings.
4.
Click
Back
to display the
PID Configuration
page.
HYD Wiring fields
DI1 Window / Occupancy / Air Flow / Changeover
LON Bus
The terminals in Table 49 are used to connect the LON Bus
FTT-10A. The LON terminals are insensitive to polarity.
Power
Power Supply
24 Vac; 50/60 Hz
Thermal
Switching
Band/PID
Boost
Cooling/Heating
Boost Temp
Sets a boost band for normal PID operation and when using thermal actuators. The variables indicate a
setpoint-space temperature deviation outside which the outputs are switched to full operation to act as a boost
function when space temperature deviates significantly from the desired setpoint. These values also serve as a
threshold for two-point switching of thermal actuators.
•
The threshold can be set in the range 0 to 10 DDC (7.2 to 180 DDF).
•
If the threshold is set to 0 DDC, the boost function is disabled.
Table 47. Hydronic PID Parameters. (Continued)
Name
Definition
Table 48. HYD Wiring Diagram.
Name
Definition
Wall Module
Override LED
Setpoint
Bypass Button
Room Temp Sensor
Table 49. LON Bus FTT-10A Terminal Connections.
Output 1 /
Output 2
Terminal 14/15
Terminal 17/18
Floating
14 on =open valve
17 on = open valve
15 on = close valve
18 on = close valve
1-stage
14 = on/off
17 = on/off
15 = not used
18 = not used
2-stage
14 on = stage 1
17 on = stage 1
14 on + 15 on = stage 2 17 on + 18 on = stage 2
3-stage
14 on = stage 1
17 on = stage 1
15 on = stage 2
18 on = stage 2
14 on + 15 on = stage 3 17 on + 18 on = stage 3
PWM
14 = PWM
17 = PWM
15 = not used
18 = not used
Thermal
14 = Pulse modulated
17 = Pulse modulated
15 = not used
18 = not used