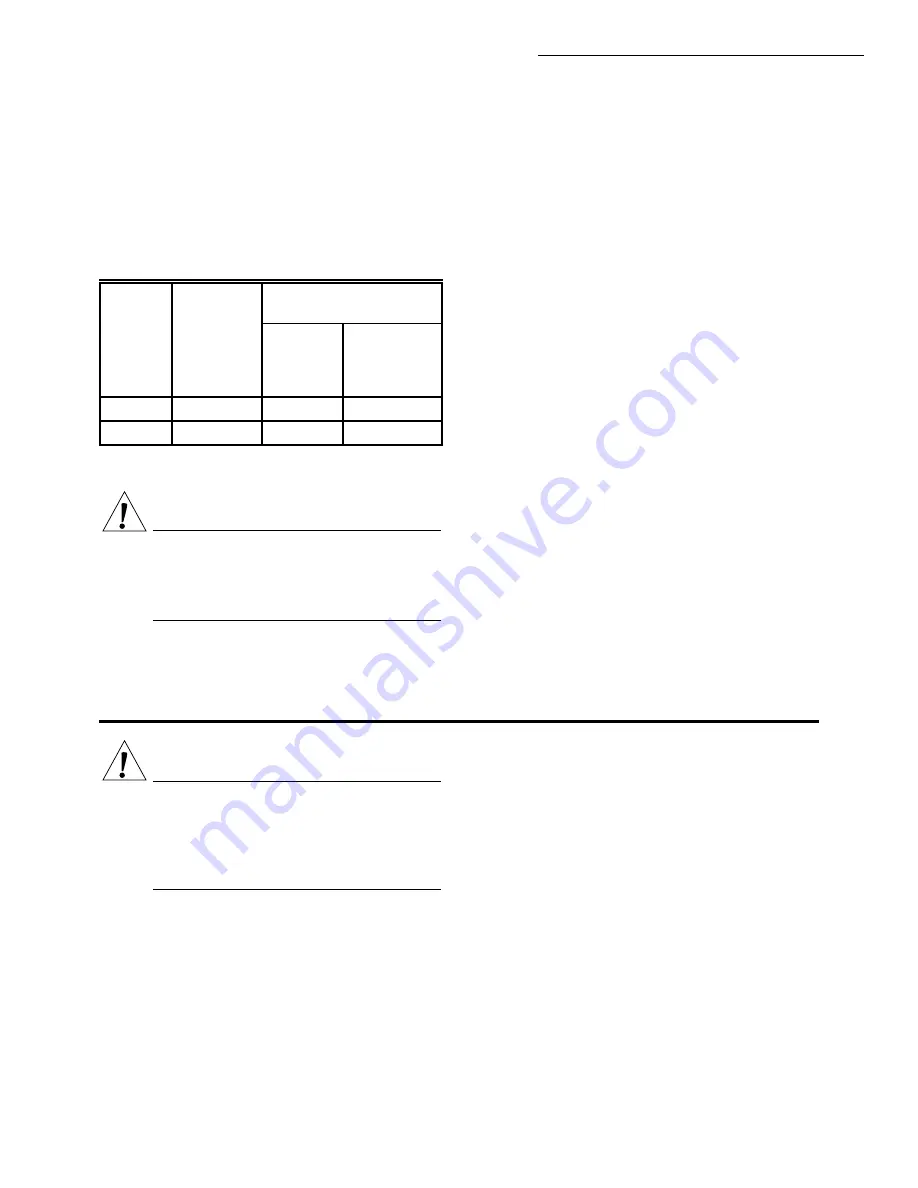
13
68-0160
4. If the desired outlet gas pressure or gas flow rate
cannot be achieved by adjusting the gas control, check the
gas control inlet pressure by using a manometer at the inlet
pressure tap. If the inlet pressure is in the normal range (refer
to Table 5), replace the gas control. Otherwise, take the
necessary steps to provide proper gas pressure to the gas
control.
TABLE 5—PRESSURE REGULATOR
SPECIFICATION PRESSURES FOR STANDARD-
OPENING NATURAL GAS.
NOTE: Read steps 1 through 7 below before starting and
compare to the safety shutdown or safety lockout tests
recommended for the intermittent pilot (IP), hot surface
(HSI) or direct spark (DSI) module. When different, use
the procedure recommended for the module.
1. Turn off gas supply.
2. Set the thermostat or controller above room tempera-
ture to call for heat.
3. • Intermittent Pilot Ignition—Watch for an ignition
spark at pilot burner either immediately or follow-
ing prepurge. See ignition module specifications.
• Hot Surface or Direct Spark Ignition—Watch for
an ignition spark or glow at hot surface igniter
either immediately or following prepurge. See ig-
nition module specifications.
4. If module has timed ignition, time the length of the
igniter operation. See ignition module specifications.
5. • Intermittent Pilot Ignition—After the module locks
out, turn on gas supply and make sure there is no
gas flow to the pilot or main burner.
NOTE: With modules that continue spark until pilot lights or
system is shut down manually, pilot should light when
gas supply is turned on.
• Hot Surface or Direct Spark Ignition—After the
module locks out, turn on gas supply and assure
there is no gas flow to main burner.
6. Set the thermostat below room temperature and wait at
least 45 seconds to reset system.
7. Operate system through one complete cycle to make
sure all controls operate properly.
Maintenance
The maintenance program should include regular check-
out of the gas control; see Startup and Checkout section. To
check out the control system, see the appliance manufac-
turer literature. Maintenance frequency must be determined
individually for each application. Some considerations are:
• Cycling frequency. For appliances that may cycle
100,000 times annually, check monthly.
• Intermittent use. For appliances that are used season-
ally, check before shutdown and again before the next
use.
• Consequence of unexpected shutdown. Where the cost
of an unexpected shutdown would be high, check the
system more often.
• Dusty, wet, or corrosive environment. Because these
environments can cause the gas control to deteriorate
more rapidly, check the system more often.
NOTE: If the gas control will be exposed to high ammonia
conditions; e.g., those used in greenhouses or animal
barns, contact your Honeywell sales representative to
request a gas control with corrosion resistant construction.
Outlet Pressure
(Full Rate)
Unit
of
Measure
Nominal
Inlet
Pressure
Range
Nominal
Factory
Outlet
Setting
Adjustment
Setting
Range
in. wc
5.0 - 7.0
3.5
3.0 - 5.0
kPa
1.2 - 1.7
0.9
0.7 - 1.2
CHECK SAFETY SHUTDOWN PERFORMANCE
WARNING
FIRE OR EXPLOSION HAZARD
CAN CAUSE PROPERTY DAMAGE,
SEVERE INJURY, OR DEATH
Perform the safety shutdown test any time work is
done on a gas system.
WARNING
FIRE OR EXPLOSION HAZARD
CAN CAUSE PROPERTY DAMAGE,
SEVERE INJURY, OR DEATH
Improper cleaning or reassembly can cause gas
leakage. When cleaning, be sure that the control is
reassembled properly and perform gas leak test.
Regular preventive maintenance is important in applica-
tions that place a heavy load on system controls such as
commercial cooking, agricultural and industrial operations
because:
• In many such applications, particularly commercial
cooking, the equipment operates 100,000 to 200,000
cycles per year. Such heavy cycling can wear out the
gas control in one to two years.
• Exposure to water, dirt, chemicals and heat can dam-
age the gas control and shut down the control system.
VR8345M
STARTUP AND CHECKOUT • MAINTENANCE
Содержание TRADELINE VR8345M
Страница 18: ...68 0160 18 ...
Страница 19: ...19 68 0160 ...