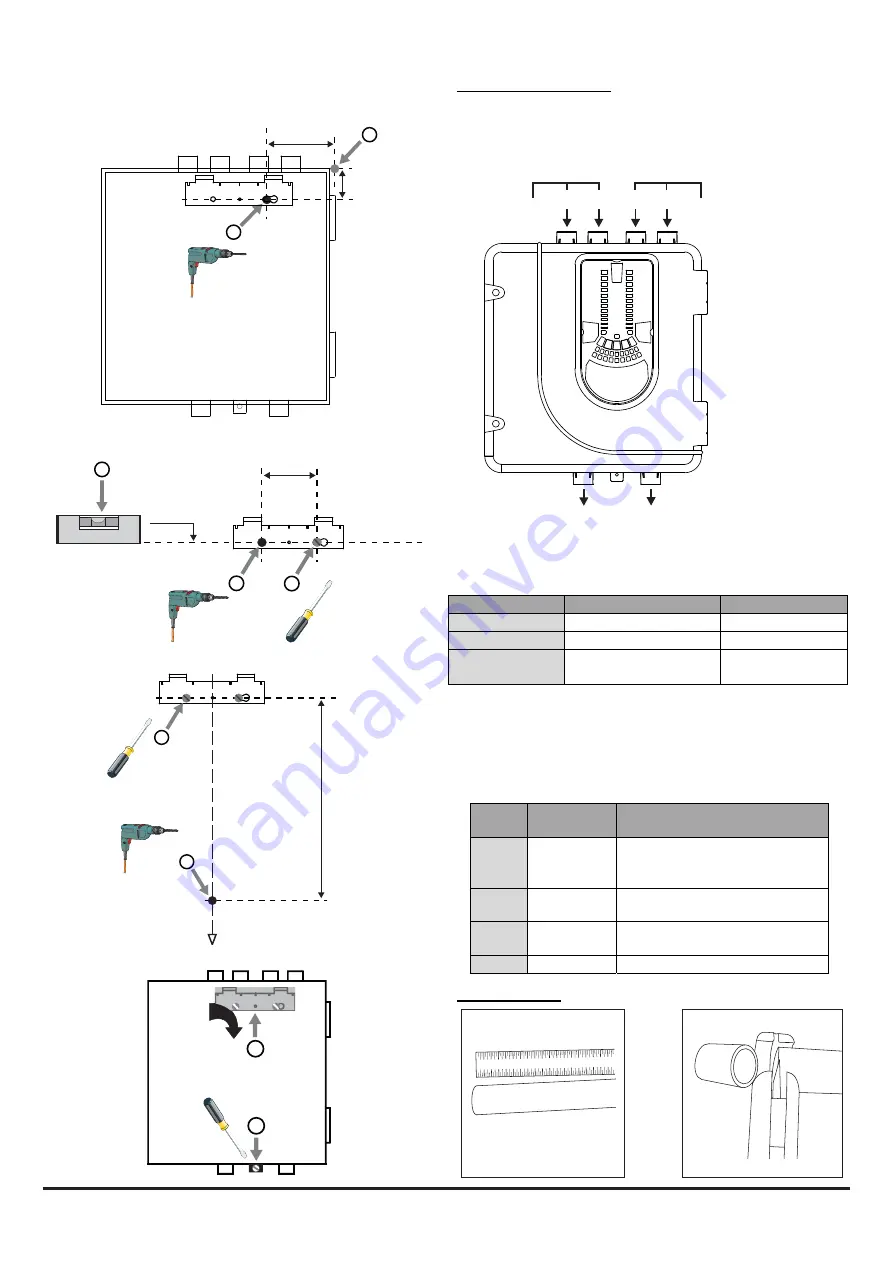
N200-102-00
3
I56-3947-202
Figure 7: Sequence (1 to 9) to Mount the Detector on the Bracket
Pipe Installation
1 2 3 4 5 6 7 8 9 10 11 12 13 14 15 16 1
7 18
1 2 3 4 5 6 7 8 9 10 11 12 13 14 15 16 17
18
99 mm
41
1
2
mm
90 mm
4
3
0.00
o
5
329 mm
6
7
7a
7b
7c
7d
8
9
1
2
FAAST LT MODEL
INLET PIPE HOLE
OUTLET PIPE HOLE
NFXI‐ASD11
1 and / or 2
5
NFXI‐ASD12
1 and / or 2
6
NFXI‐ASD22
Channel 1 ‐ 1 and / or 2
Channel 2 – 3 and / or 4
5
6
Pipe Hole Configuration
Figure 8
below shows the pipe holes available on the unit. Each
unit has 2 pipe holes per channel connected together like a T-Piece.
If using a 1 channel unit, holes 3 and 4 do not function. Use
Table
1
to locate the holes required for the installation:
Figure 8: Pipe Holes
Table 1: Pipe Holes Used for Each FAAST LT Model
Note 1:
Pipe holes not used should be kept sealed.
Note 2:
Do
NOT
glue pipes into the pipe holes.
Table 1a: Maximum Number of Pipe Holes Allowed Per Channel
for EN54-20 Compliance
All figures quoted using highest (level 1) sensitivity.
1
2
3
4
5
6
CHANNEL 1
CHANNEL 2 (ONLY FUNCTION
ON 2 CHANNEL UNITS)
CHANNEL 1 (NOT
USED FOR COMMON
CHAMBER UNIT)
CHANNEL 2 (ONLY FUNCTIONS
ON 2 CHANNEL AND COMMON
CHAMBER UNITS)
CLASS PIPE LENGTH
(m)
MAX NUMBER OF HOLES PER
CHANNEL
C
100
18
(5
x
2mm,
6
x
2.5mm,
3
x
3mm,
3
x
3.5mm
and
1
x
4mm)
+
4mm
non
sensing
end
hole
C
160
(2
x
80)
Using
T
‐
Piece
9
holes
per
branch
(3
x
2.5mm,
6
x
3mm)
+
3mm
non
sensing
end
hole
B
100
6
(2
x
3.5mm,
2
x
4mm,
2
x
5mm
inc
end
hole)
A
80
3
(1
x
5mm,
2
x
6mm
inc
end
hole)