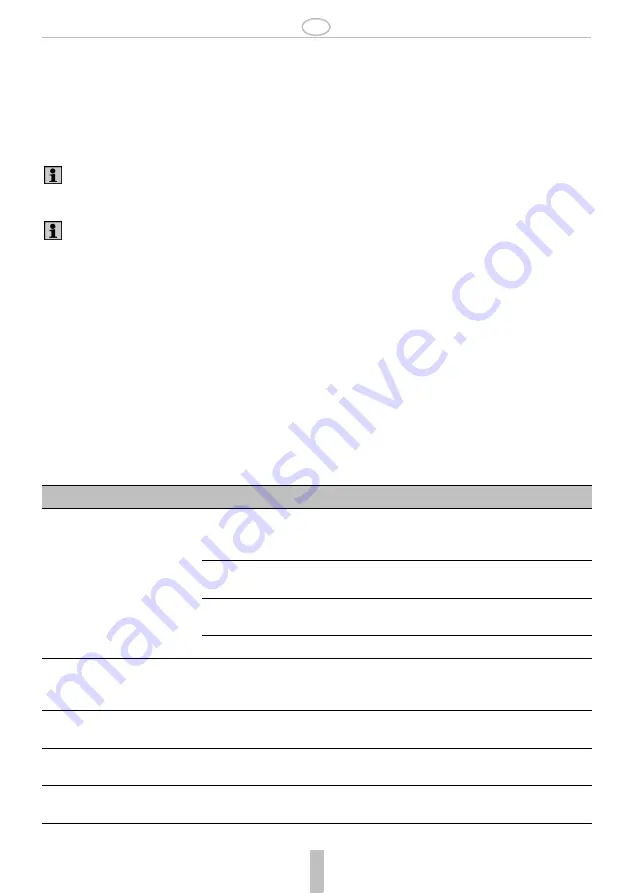
Honeywell GmbH
16
MU1H-1546GE23 R0908
GB
9.2.3 Check valve
1. Close ball valve on the inlet side of the refilling
combination and on the outlet side of the blending
unit
2. Decompress the outlet side by opening the
sampling valve (air bleed valve of the blending unit)
3. Replace non return valve
4. Check operation
9.3 Replacing cartridge
1. Close ball valve on the inlet side of the refilling
combination and on the outlet side of the blending
unit
2. Decompress the outlet side by opening the
sampling valve (air bleed valve of the blending unit)
3. Unscrew the cartridge from the blending unit
4. Screw the new cartridge in manually
5. Open ball valves on the inlet and outlet side
10. Disposal
• Dezincification-resistant brass housing
• Discharge valve, cartridge insert, valve insert,
mechanical components of the blending unit and
spring bonnet made of high-quality plastic
• Fibre-reinforced NBR diaphragm
• Seals in NBR and EPDM
• Spring steel adjustment spring
• Stainless steel fine filter mesh
• Cartridge made of polypropylene (dispose of with
residual waste)
Check valve will be destroyed after demounting
When the filling level of the heating system
exceeds the specified capacity, a cartridge
exchange has to be performed.
The maximum capacity is determined according
to the total water hardness and the dilution
setting. (see table in chapter 14)
The capacity is noted on a table included in the
scope of delivery, as well as the respectively
added amounts of water. If the filling level
exceeds the noted water flow meter end value, a
cartridge exchange has to be performed.
An exchange of the softening cartridge is recom-
mended at least 12 months after its first usage
due to technical safety purposes.
11. Troubleshooting
Problem
Cause
Remedy
No or too small water flow rate Refilling combination is not fitted in flow
direction
Fit refilling combination in flow direc-
tion (note direction of arrow on
housing)
Ball valves up- or downstream of refilling
combination are not fully open
Open ball valves entirely
Pressure reducing valve is not set to the
desired outlet pressure
Set outlet pressure
integrated strainer is contaminated
clean strainer
Discharge valve opens without
reason (no fluctuation of inlet
pressure)
Non return valve upstream or discharge
valve are contaminated
Remove cartridge insert and clean
or exchange it
Discharge valve does not close Discharge valve is contaminated or faulty Remove cartridge insert and clean
or exchange it
Water is escaping from spring
hood
Valve insert diaphragm damaged
Exchange valve insert
The outlet pressure set does not
remain constant
Valve insert, sealing ring or edge of nozzle
is contaminated or worn
Exchange valve insert
Содержание NK300soft
Страница 55: ...Honeywell GmbH 55 MU1H 1546GE23 R0908 CZ ...