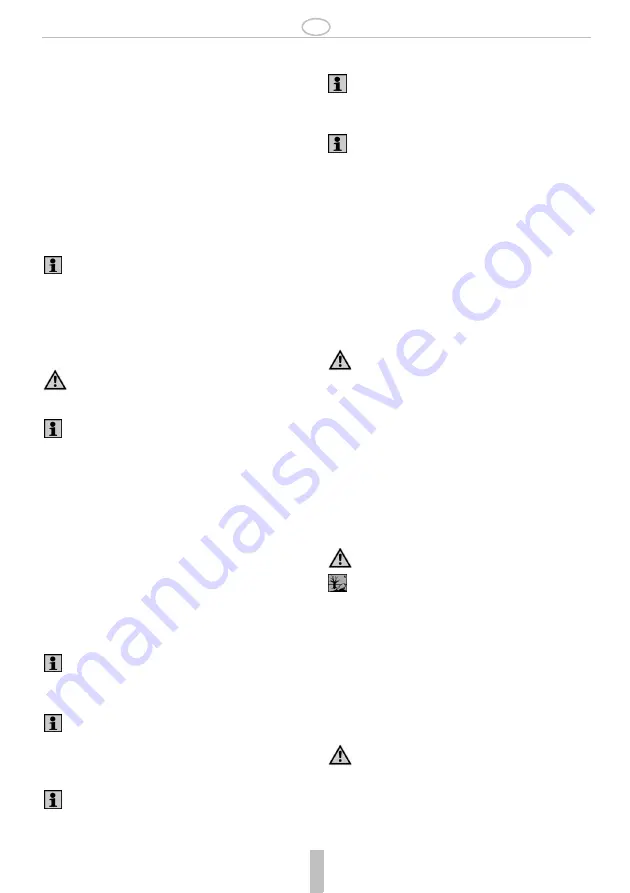
Honeywell GmbH
15
MU1H-1546GE23 R0908
GB
2. Set the dilution unit with the blue adjustment handle
o The suitable dilution setting (marker 0-3 on the
casing of the dilution unit, remove insulation lining
if necessary) is dependant on the regional water
hardness and the desired residual hardness. The
value can be extracted from the table attached to
the cartridge.
8.3 Filling up the system
1. Slowly open the ball valve on the inlet and outlet
side of the refilling combination and on the outlet
side of the blending unit
2. After filling up the system, close the ball valves
3. Note the required parameters listed on the label on
the cartridge
9. Maintenance
9.1 Inspection
9.1.1 Testing pressure reducing valve
1. Close ball valve on the outlet side of the refilling
combination
2. Check outlet pressure on pressure gauge when no
flow is occurring
o If the pressure is increasing slowly, the valve may
be dirty or defective. In this instance, carry out
servicing and cleaning
3. Slowly open the ball valve on the outlet side of the
refilling combination
9.1.2 Testing discharge valve
1. Procedure according to instruction of the test control
unit TKA295 resp. TK295
9.1.3 Testing outlet check valve
1. Procedure according to instruction of the test control
unit TKA295 resp. TK295
9.2 Maintenance
In accordance with DIN EN 1717 a regular mainte-
nance must be taken.
9.2.1 Valve insert and filter
1. Close ball valve on the inlet side of the refilling
combination and on the outlet side of the blending
unit
2. Decompress the outlet side by opening the
sampling valve (air bleed valve of the blending unit)
3. Loosen the slotted screw of the refilling combination
o Do not remove slotted screw
4. Slacken tension in compression spring
o Turn the adjuster knob (grey) left (-) as far as it will
go
5. Unscrew spring bonnet
o Use double ring wrench ZR06K
6. Remove slip ring
7. Remove valve insert with a pair of pliers
8. Check that sealing ring, edge of nozzle and slotted
ring are in good condition, and if necessary replace
the entire valve insert
9. Reassemble in reverse order
10.Set outlet pressure
9.2.2 Maintenance and cleaning of cartridge insert
1. Close ball valve on the inlet side of the refilling
combination and on the outlet side of the blending
unit
2. Decompress the outlet side by opening the
sampling valve (air bleed valve of the blending unit)
3. Remove cover from cartridge insert
4. Remove cartridge insert and strainer
5. Remove strainer from cartridge insert
6. Clean or replace strainer and cartridge insert
7. Reassemble in reverse order
o push down the cartridge insert till it snaps in
8. Check operation
Because of casual fluctuation of pressure drip-
ping water at discharge valve can occur!
This is no malfunction and therefore no reason for
complaint!
Maintenance of backflow preventer must be
carried out by authorized personnel!
• Frequency: every 6 month (depending on local
operating conditions)
• To be carried out by an installation company
• Inspection with a test control unit and mainte-
nance-set (see accessories)
Take note of the instructions of the test control
unit TKA295 or TK295
Quick test for the discharge valve:
• Lower the inlet pressure
o if the discharge valve opens (it drops), the
function is o.k.
Take note of the instructions of the test control
unit TKA295 or TK295
We recommend a planned maintenance contract
with an installation company
Frequency: every 1-3 years (depending on local
operating conditions)
To be carried out by an installation company
There is a spring in the spring bonnet. It may
cause injuries if the spring is derailing.
• Make sure that the spring is released!
Do not use any cleaning agents containing
solvents and/or alcohol to clean the plastic parts!
Detergents must not be allowed to enter the envi-
ronment or the sewerage system!
Do not dismantle cartridge insert in individual
parts!
Содержание NK300soft
Страница 55: ...Honeywell GmbH 55 MU1H 1546GE23 R0908 CZ ...