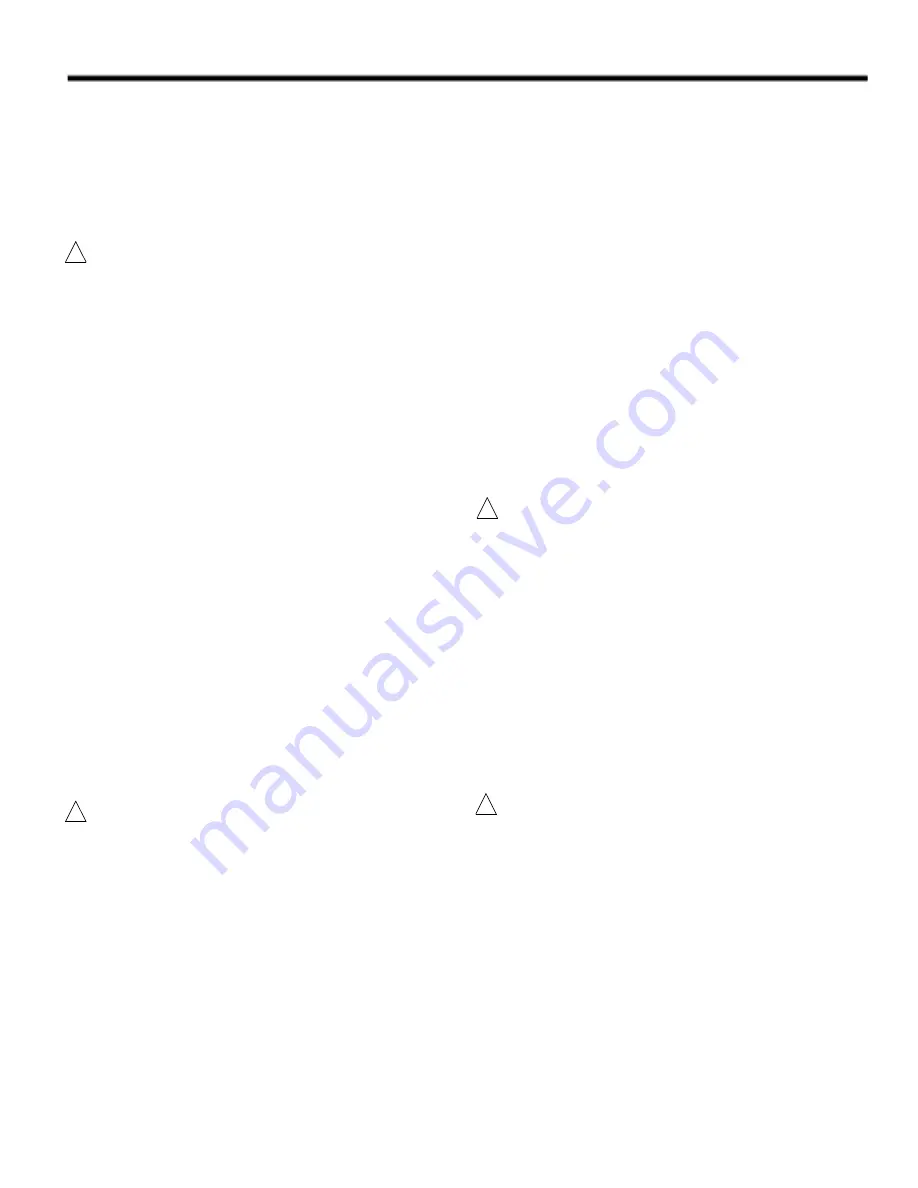
OPERATION
Each time actuator terminals T5-T6 are (re)powered, the micro-
processor will cycle the valve through a full stroke to calibrate its
position. Any stroke between 1/2
”
(13 mm) and 1
”
(25 mm) will be
divided into 30 equal steps. Run time is proportional to stroke length
and power supply voltage. The actuator will also slow down as the
valve closes off the seat. The LED lights when terminals T5-T6 are
powered, and flashes when the actuator is in motion. T5 is con-
nected to Terminal R in ML6984 and to Terminal W in ML7984.
Initial callibration does not apply to ML6984 installed for 3-wire
control or installed for 5-wire control without the 272630D position
feedback/auxiliary switch module. Span and start positions will need
to be set during controller set-up. See ML6984 Operation 3-wire,
below.
ML7984 Operation:
The microprocessor responds to the signal across the input
terminals based on the configuration DIP switch settings.
When correctly connected to the actuator, a control signal between
signal input terminals is converted to a digital run time and compared
to pulse counts from the first gear in the gear train. When these
counters are equal, the drive motor and drive shaft are stationary.
As long as the value of the controlled medium remains at the
controller setpoint, the control loop circuit is in balance, and the
actuator does not run. When the controller set point or controlled
temperature changes, the controller output voltage is changed,
causing the counters to differ. As the actuator moves in the direction
to correct the difference, the counters increment or decrement,
and stop the actuator when the input and gear counts agree.
At the end of the valve stroke, the actuator develops the necessary
force for positive valve close-off. The motor stops automatically
when the motor draws a predetermined current which corresponds
to a force level. The digital counters are reset and calibrated at
each end of stroke.
Modulating actuators will automatically travel to the position
corresponding to analog input signal following the self-calibration
cycle.
1. Disconnect power supply before beginning installation to prevent
electrical shock and equipment damage.
2. All wiring must comply with applicable local electrical codes,
ordinances, and regulations.
3. Make certain that the voltage and frequency of the power supply
correspond to the rating of the device.
4.
DO NOT electrically operate the MLx984 actuator before
assembly to the valve because damage not apparent to the
installer may occur.
5.
DO NOT connect 24 Vac between any ML7984 signal input
terminals. DEVICE FAILURE WILL RESULT!
!
NOTE:
!
Caution
GENERAL NOTE:
1. The ML7984 must be field configured with the DIP switches which
are located beside the terminal block. See wiring diagrams for
details. Turn power off before setting the DIP switches.
2. There is a 1.5 second delay in actuator response to every signal
change. This occurs to screen out electrical noise.
3. For proper operation, voltage on the T5 and T6 must not be less
than 22 Vac or 24 Vdc during running or force generating stages.
Increase transformer VA rating or use a model with better
regulation if voltage drops below 22 Vac when the valve is closing
off.
ML6984 Floating Operation, 5-Wire:
The motor is controlled by a microprocessor. Connecting B to R for
1/10 second or longer tells the microprocessor to cause the actua-
tor to drive upwards. Connecting W to R will cause the actuator to
drive downwards. For “floating” control, the actuator will remain in
the last position when there is no connection to R.
At the end of the valve stroke, the actuator will develop the neces-
sary force for positive valve close-off. As forces are developed, the
current to the motor increases. The microprocessor stops the ac-
tuator automatically when motor current and force reaches the fac-
tory-calibrated level.
There must be at least 1.5 second delay between successive
floating input signals. The actuator will ignore floating signals during
calibration cycle and does not remember any pulses sent during
this period. The controller may need to run through its own
calibration cycle before use.
ML6984 Operation, 3-Wire:
ML6984 may be installed like a conventional (non-electronic)
floating actuator. The interface electronics are powered at the same
time as the motor. Pulses must be at least 100 ms long with a
delay of at least 1500 ms between pulses. When ML6984 is not
powered between terminals T6 and T5/R, self-calibration will not
occur.
The controller must drive the valve through a cycle manually
to calibrate stroke to the controller.
The 272630D position feedback/auxiliary switch module cannot
be used with ML6984 3-wire installation. The 272630D requires
continuous power.
ML6984 XL10 Controller Compatibility:
XL10 controllers are designed to work with constant-speed actua-
tors. ML6984 actuators use direct current motors which vary their
speed as the valve seats or if power supply voltage is not consist-
ent. ML6984 actuators in 5-wire mode offer 30 discrete positions
only. To minimize potential valve position drift, XL10 controllers
should use the 3-wire installation and be programmed for a daily
valve exercise cycle.
!
NOTE:
!
NOTE:
9
95C-10939-4