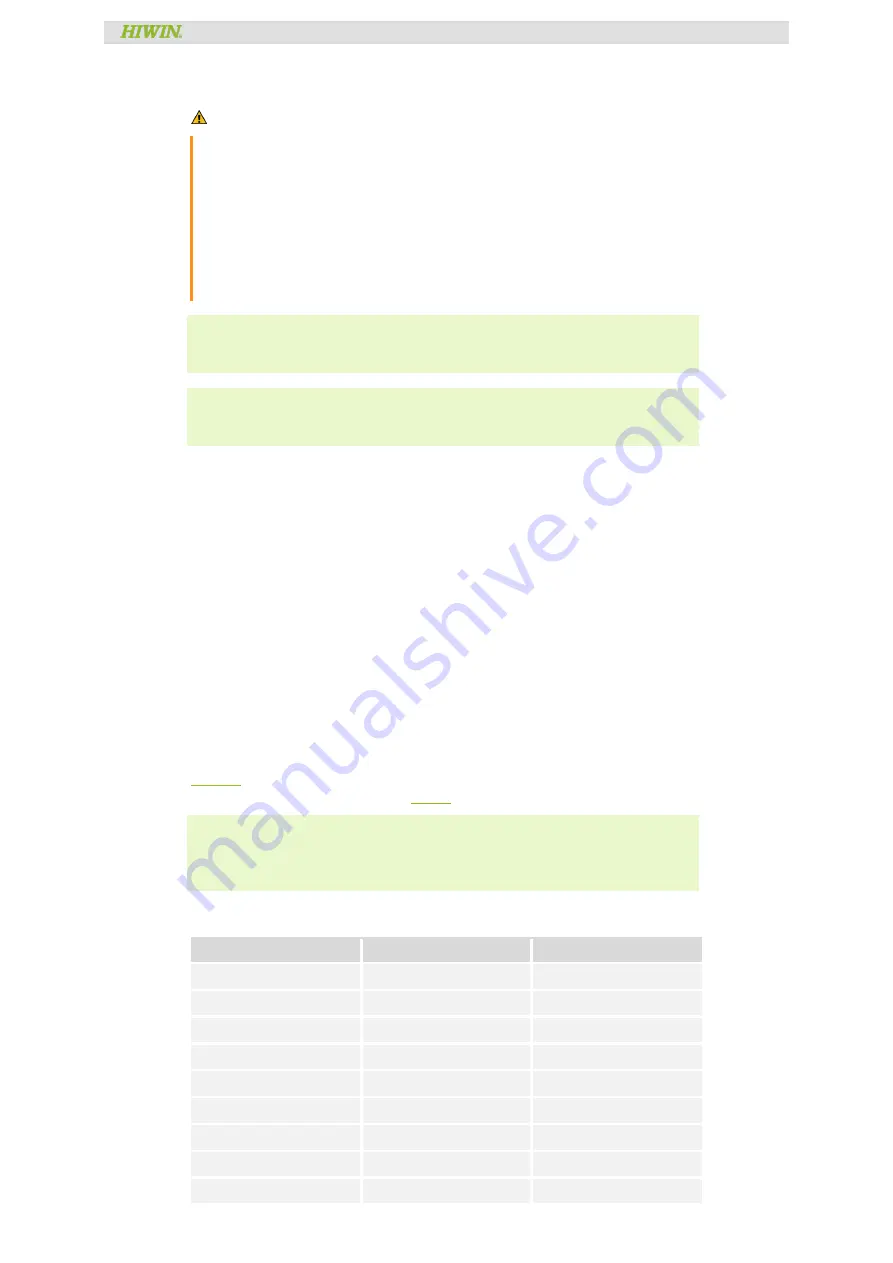
Assembly instructions
Electrical connection
HIWIN MAGIC Distance Measuring Systems
MAGIC-01-14-EN-2207-MA
Page
22
of
32
5
Electrical connection
Warning
! Danger due to electrical voltage!
Dangerous currents may flow before and during assembly, disassembly and repair work.
Make sure that the system (e.g. linear motor axis) is properly earthed via the PE rail in the
switch cabinet before connecting the electrical power supply!
Electrical currents can also flow when the motor is not moving. Never disconnect electrical
connections while they are live. In unfavourable cases, electric arcs can occur and injure
persons and damage contacts!
Observe the assembly instructions of the other system components (e.g. linear motor,
servo drive)!
Note:
Since the sensor is operated with a low voltage, it alone does not normally pose a risk of injury
or death.
Note:
Do not operate the sensor with a voltage other than the specified voltage, otherwise it may be
destroyed!
5.1
Cable and plug
The cable at the encoder is a maximum of 5
m long. Up to a length of 5
m, the voltage drop is
minimal and the encoder complies with EMC interference immunity according to EN61000-4-4,
test severity level 3.
For HIWIN linear motor axes and generally for all highly dynamic applications, we recommend
our pre-assembled extension cables, which are specially designed for dynamic use in energy
chains. The high-quality 8-core extension cables (each: V1+/V1–,V2+/V2– and V0+/V0–
or: A, Ā
and B, B
¯
and Z, Z¯ for digital signals according to RS422, twisted pair and double shielded) are
supplied with a single-sided round connector (coupling, female) or are customised.
Keeping the sensor cable as short as possible is also recommended when using the sensor near
an EMC interference source, e.g. a linear motor. Generally, the shorter the line, the lower the
sensitivity to interference.
Up to a cable length of 500
mm and use of the described plug and the prescribed extension
cable, test severity level 4 is also achieved with insulation of the encoder housing to machine
ground with an insulation thickness greater than 4
kV in accordance with EN61000-4-4.
Table 5.1 shows the assignment of the open cable ends and the optionally available round plug.
The structure of this plug is illustrated at Fig. 5.1.
Note:
To avoid EMC interference in the encoder signal, the encoder cable extension must be shielded
and the shielding must be contacted over a wide area via the plugs. High-quality, fully shielded
plugs must be used.
Table 5.1: Line and plug assignments
Colour of encoder cable
Round plug pin no.
Signal
Brown
4 and 5
Power supply 5
V
White
12 and 13
GND
/
0
V
Green
9
V1+
/
A
Yellow
1
V1-
/
Ā
Blue
10
V2+
/
B
Red
2
V2-
/
B¯
Purple
3
Ref+
/
Z
Grey
11
Ref-
/
Z¯
Plug connector housing
Shielding