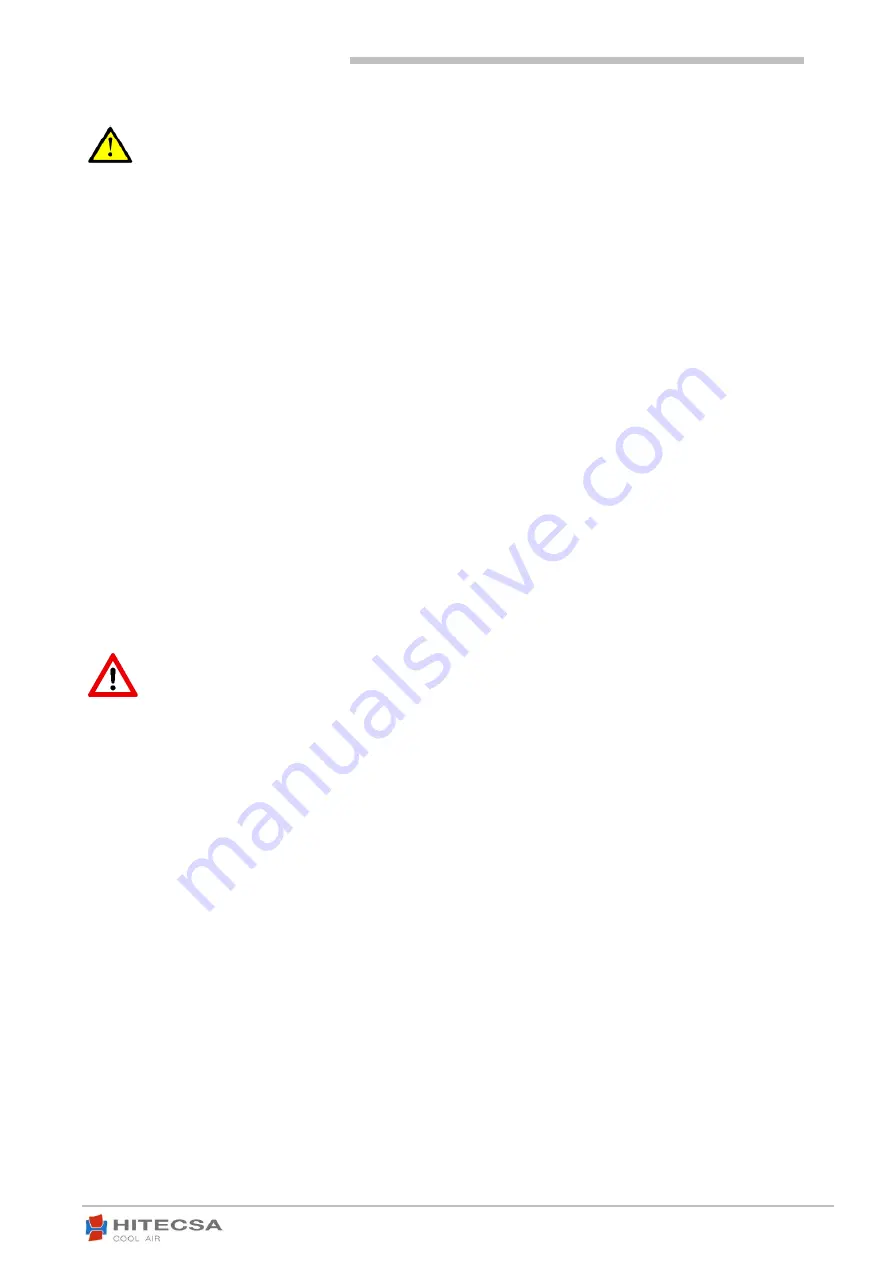
22
IOM_WPVBZ HE-WPVZ HE_401-1201-4002_208110_200901_EN
PACKAGED COMPACT VERTICAL
– WATER / AIR
WPVBZ HE / WPVZ HE
OPERATION
BEFORE START-UP
Make sure that all the electrical connections are properly tight.
Make sure that the panels are firmly secured with screws.
Check that there is no leakage of oil or refrigerant.
Ensure that the unit is evenly levelled.
Check that there is enough space for operation and maintenance.
Check that the drainage is not blocked.
Check that there is no water leakage. Verify the correct operation of the valves.
Verify that the water circuit enables the complete evacuation of the water for repairs and shutdown periods. Verify
that the water circuit can be purged for air correctly.
Always use the electrical diagram of the unit to make the connections.
Make sure that all electrical connections are properly tight.
The power supply of the unit must comply with the data stated on the serial plate. Damage caused by the start-
up of the unit with an incorrect voltage line will not covered by Hitecsa’s warranty.
The unit must not be supplied with any other voltage than that indicated on the serial plate. The power supply to
the unit must be within 10% of the voltage indicated on the serial plate.
Check the correct rotation direction of the fans.
The installer must place line protection parts according to the current legislation.
The electrical wires must be protected by a tube or other cable conduits.
Make sure that the crankcase heater of each compressor has been operating for 24 hours prior the Start Up.
Check that the air filters are clean and fitted correctly.
Check the condition and position of the grilles, diffusers, air ducts, tarpaulins, etc…
START UP
It is very important to proceed to purging the system for air and to remove all dirt particles from the
water circuit. Proceed to both operations at the same time.
At first start up the water pump for a few minutes.
Stop the water pump and notice if the automatic purge is working. Repeat this operation 10 times. If it proceeds
in this way, all the existing air will go from the system and the water circuit will be filled.
The next step is to remove the water mesh filter and clean it. The performance of the system will improve since
the dirty mesh filter has a high pressure drop.
It is necessary to register the air inlet and outlet temperatures to the internal coil, the volts and amps of the
compressor and motor fan, as well as the suction and discharge pressure of each compressor.
Remember that it is necessary to clean the air filters after the first 4 hours of operation.
Complete at least 3 cooling cycle operations.