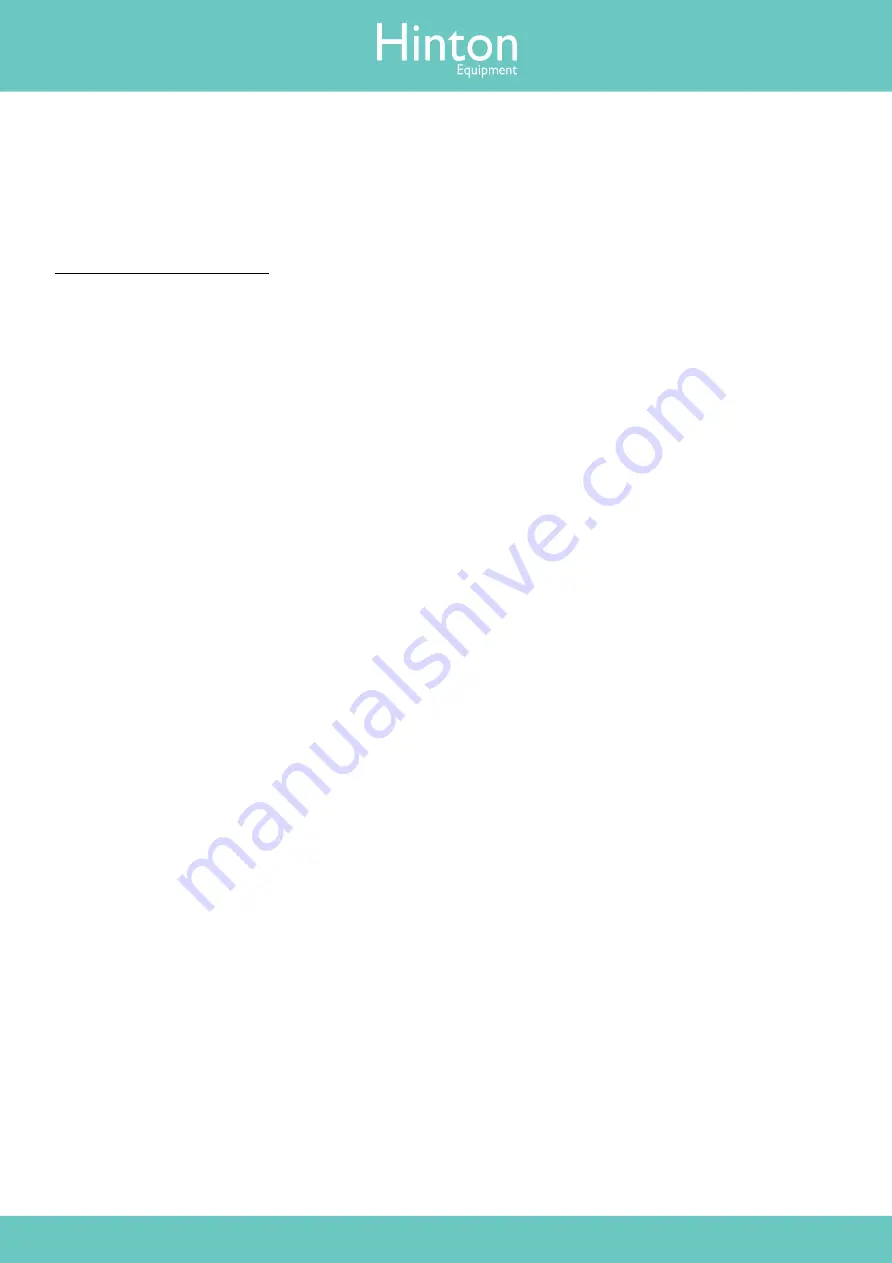
COMMON BRAZING FAULTS
JOINT FRACTURE
Joint fractures are more commonly found on larger joints and joints manufactured from dissimilar
materials. When metals are heated they expand and when cooling they contract. If the two metals
being brazed are manufactured from different compositions they will have different expansion and
contraction rates. On cooling they will contract at different rates resulting on both metals pulling
against each other which can result in fracture. This can be overcome by ensuring that the joint is
kept out of draughts and allowed to cool slowly.
(wrap joint in asbestos fire blanket or similar material to ensure slow cooling)
HEATING OF JOINT
The flame should be applied to the joint in an even manner by moving the flame around. If one section
of the joint is thicker than the other, more heat should be applied to the thicker section.
BRAZE/SOLDER WILL NOT RUN
If brazing alloy or solder will not run then there are generally two reasons that attribute to this: not
enough heat applied to joint or a fluxing problem. Both of these problems can be overcome quite
easily by increasing the heat input (use larger nozzle if need be) and the flux is suitable for the alloy
being used.
TOO MUCH ALLOY FLOWS AROUND JOINT
It must be appreciated that the alloy will always flow where the most heat is applied to the joint. If too
much heat is applied the alloy will flow all over the joint, similarly if too much flux is applied during
silver brazing the alloy will
always flow towards the flux. Ensure the correct diameter of braze alloy is being used. Too large a
diameter for joint means too much metal being added to joint. (makes for expensive joints)
Page 8
Flametech Lite Assembly & Safety Instructions
Содержание Flametech Lite
Страница 1: ...Flametech Lite Assembly and operating instructions ...
Страница 11: ...Page 11 ...