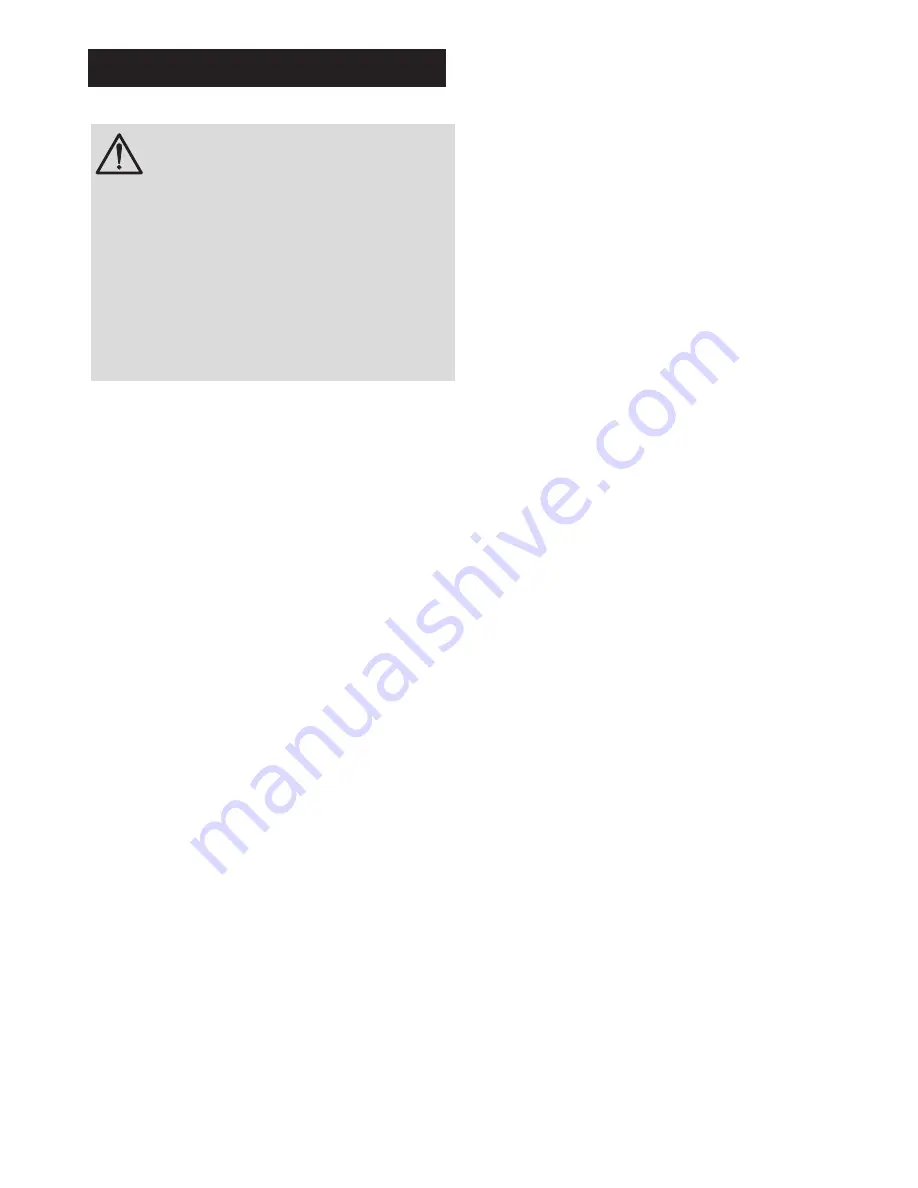
20
8. Operation
8.1 General
WARNING
`
If water discharges from the
temperature/pressure relief valve on the
cylinder shut down the heat source. Do
not turn off any water supply. Contact a
competent installer for unvented water
heaters to check the system.
`
Do not tamper with any of the safety
valves fitted to the system. If a fault is
suspected contact a competent installer.
`
DO NOT bypass the thermal cut-out(s)
in any circumstances.
Benchmark
The cylinder is covered by the Benchmark Scheme
which aims to improve the standards of installation
and commissioning of domestic heating and hot water
systems in the UK and to encourage regular servicing
to optimise safety, efficiency and performance.
Benchmark is managed and promoted by the Heating
and Hotwater Industry Council. For more information
visit www.centralheating.co.uk.
Please ensure that the installer has fully completed the
Benchmark Checklist (page 26) of this manual and that
you have signed it to say that you have received a full
and clear explanation of its operation. The installer is
legally required to complete a commissioning checklist
as a means of complying with the appropriate Building
Regulations (England & Wales).
All installations must be notified to Local Area Building
Control either directly or through a Competent
Persons Scheme. A Building Regulations Compliance
Certificate will then be issued to the customer who
should, on receipt, write the Notification Number on
the Benchmark Checklist.
This product should be serviced regularly to optimise
its safety, efficiency and performance. The service
engineer should complete the relevant Service Record
on the Benchmark Checklist after each service.
The Benchmark Checklist may be required in the event
of any warranty work.
Flow performance
When initially opening hot outlets a small surge in
flow may be noticed as pressures stabilise. This is
quite normal with unvented systems. In some areas
cloudiness may be noticed in the hot water. This is due
to aeration of the water, is quite normal and will quickly
clear.
Temperature controls – direct units immersion
heater(s)
`
All immersion heaters are fitted with a combined
thermostat and thermal cut-out located under the
terminal cover mounted on the side of the product.
`
Access to the thermostat can be made by opening
the immersion heater cover - DISCONNECT THE
ELECTRICAL SUPPLY BEFORE OPENING THE
COVER(S).
`
Temperature adjustment is made by inserting a flat
bladed screwdriver in the slot on the adjustment
disc on top of the thermostat and rotating. The
adjustment represents a temperature range of
12°C to 72°C. Figure 11, page 20.
`
Maximum working temperature is 72°C/154°F. In
very hard water areas limit to 60/65°C (140/150°F).
DO NOT bypass the thermal cut-out(s) in any
circumstances.
Temperature controls - indirect units
`
The cylinder units are fitted with an indirect
thermostat and thermal cut-out. These controls
must be wired in series with the 2 port motorised
zone valve supplied to interrupt the flow of primary
water around the heat exchanger coil when the
control temperature has been reached.
`
The controls are located within the lower terminal
housing along with the immersion heater
thermostat. The thermostat is factory set to give a
water storage temperature of approx 55°C to 60°C.
`
Access to the thermostat can be made by opening
the terminal housing cover. DISCONNECT THE
ELECTRICAL SUPPLY BEFORE OPENING THE
COVER.
`
Temperature adjustment is made by inserting a flat
bladded screwdriver in the adjustment knob and
rotating. The minimum thermostst setting is 12°C,
The maximum thermostat setting is 72°C.
DO NOT bypass the thermal cut-out(s) in any
circumstances.
Operational faults
Operational faults and their possible causes are
detailed in the Fault Finding section (p.23) of this book.
It is recommended that faults should be checked by a
competent installer.
The air volume within the expansion vessel will
periodically require recharging to ensure expanded
water is accommodated within the system. A discharge
of water INTERMITTENTLY from the expansion valve
will indicate the air volume has reduced to a point
where it can no longer accommodate the expansion.
This will require a suitably qualified person to check the
expansion vessel pressure and no attempt should be
made to re-pressurize the expansion vessel by the end
user.