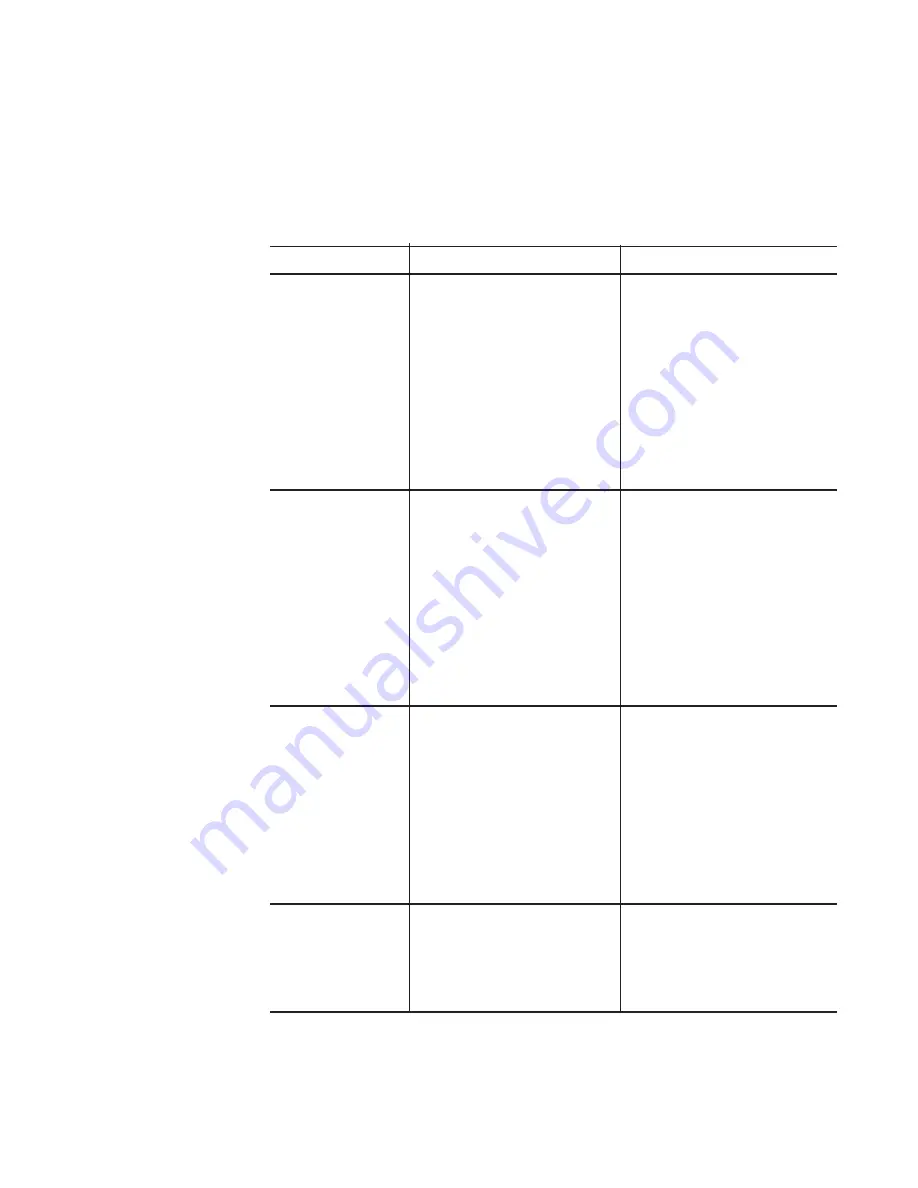
The following chart is provided to give you some guidance in determining the probable
cause and suggested corrective action for some problems that may occur with cryogenic
liquid containers. This chart is specifically tailored to your XL-65 or XL-65HP.
TROUBLESHOOTING CHART
Symptom
Possible Cause
Corrective Action
Consistently low
1. Relief valve open at low
1. Remove and replace relief
operating pressure.
pressure.
valve.
2. Economizer side of
2. Remove and replace
P.B./Economizer Regulator
regulator.
stuck open.
3. Cold liquid.
3. Open pressure building valve.
With P.B. inoperative, the
container will build pressure
over time, or an external
pressure source can be used
to pressurize container.
No pressure shown
1. Bad container pressure
1. Remove and replace bad
on container
gauge.
gauge.
pressure gauge.
2. Open inner container
2. Remove and replace bursting
bursting disc.
disc. Pressurize container
and check relief valve
operation.
5
3. Leaks in valves or
3. Leak test and repair leaks.
plumbing.
For valve repairs, see
Maintenance section.
4. Cold liquid.
4. Open pressure building
circuit.
No pressure showing 1. Pressure drop to below
1. Re-pressurize with C0
2
gas
but container is full
70 psig (4.8 bar/483 kPa)
and check for leaks. Repair
by weight.
has caused contents to
leaks, re-pressurize to relief
freeze solid. Check pres-
valve setting and allow to set
sure gauge (C0
2
only).
until contents re-liquefy.
2. Broken pressure gauge.
2. Replace pressure gauge.
3. Vent valve open/P.B.
3. Close vent valve, open P.B.
valve closed.
valve.
4. Faulty relief valve.
4. Replace relief valve.
Container full by
1. Liquid too cold.
1. Open P.B. valve or allow
weight and Liquid
to stand.
Level Gauge but very 2. Possible leak in vent valve. 2. Rebuild valve.
low pressure
3. Faulty relief valve.
3. Replace valve.
TROUBLESHOOTING
5
For containers in C0
2
service, see caution on releasing container pressure at the beginning of the
Maintenance section.