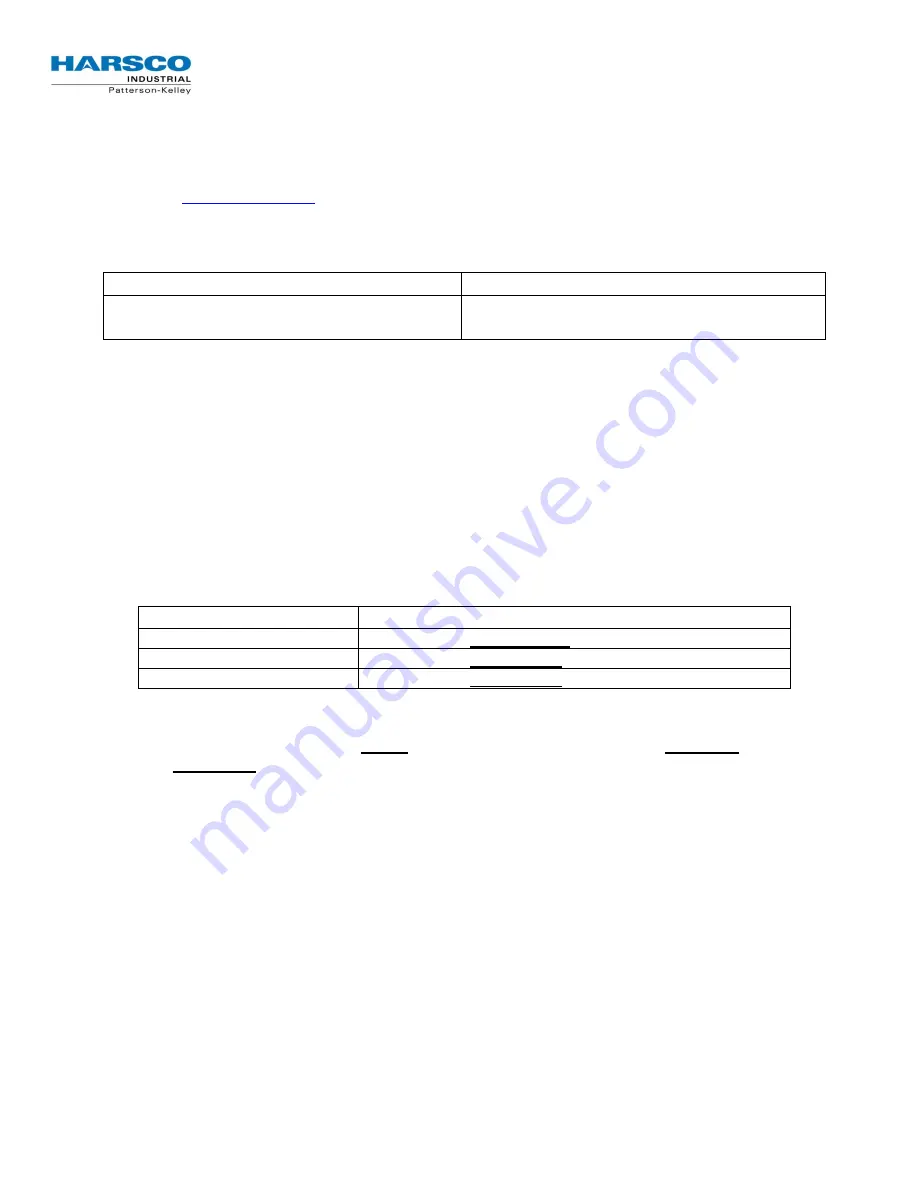
P-K SONIC
TM
Gas Fired Boiler
T
T
T
Technical Service 1.877.728.5351
echnical Service 1.877.728.5351
echnical Service 1.877.728.5351
echnical Service 1.877.728.5351
Appendix D – Installation and Quick Reference
Fuel/Gas Supply
•
Refer to
Section 3.6 Piping
for information on proper sizing of the gas supply piping. Undersized gas
piping with too much pressure drop will negatively impact the boiler’s performance.
•
Install a lock-up type gas regulator to supply an appropriate gas pressure as described below:
Natural Gas
Propane Gas
Minimum Inlet Pressure = 4.0”
W.C
.
Maximum Inlet Pressure = 14.0”
W.C.
Minimum Inlet Pressure = 7.0”
W.C.
Maximum Inlet Pressure = 14.0”
W.C.
NOTE
Harsco Industrial, Patterson-Kelley recommends installing an individual lock-up
type gas regulator in the gas supply piping to each boiler. For installations
where one master lock-up type gas pressure regulator will service multiple
boilers, Patterson-Kelley recommends contacting the local regulator
representative for application assistance specifying the appropriate lock-up
type regulator and gas pipe sizing.
Electrical/Power Supply
•
Carefully inspect the boiler’s nameplate labels which describe the power supply requirements.
•
Provide an appropriate power feed to the boiler with overcurrent protection:
Boiler Model
Power Supply Requirements
SC-1500 / SC-2000 (240V)
208-240VAC,
single phase
, 60Hz sized for 15 Amps.
SC-3000 / SC-4000 (240V)
208-240VAC,
three phase
, 60Hz sized for 20 Amps.
SC-3000 / SC-4000 (480V)
460-480VAC,
three phase
, 60Hz sized for 20 Amps.
NOTE
The SC-3000 & SC-4000
MUST
be ordered to the correct voltage!
IT IS NOT
POSSIBLE
to convert an SC-3000 or SC-4000 between the 240V and 480V
configurations in the field.
•
Prior to startup, carefully check all electrical connections for tightness as connections can come lose
during shipping.
Exhaust Venting
•
The
P-K SONIC
TM
boilers are dual-certified as Category II & Category IV appliances, capable of
operating with slightly negative to slightly positive exhaust pressure. It is critical to ensure the flue
venting material is suitable for use with the boiler.
•
For Category II installations, ensure the flue venting system is designed to maintain a slightly negative
exhaust pressure which does not exceed -0.04”
W.C.
•
For Category IV installations, ensure the flue venting system is designed to maintain a slightly positive
exhaust pressure which does not 0.22”
W.C.