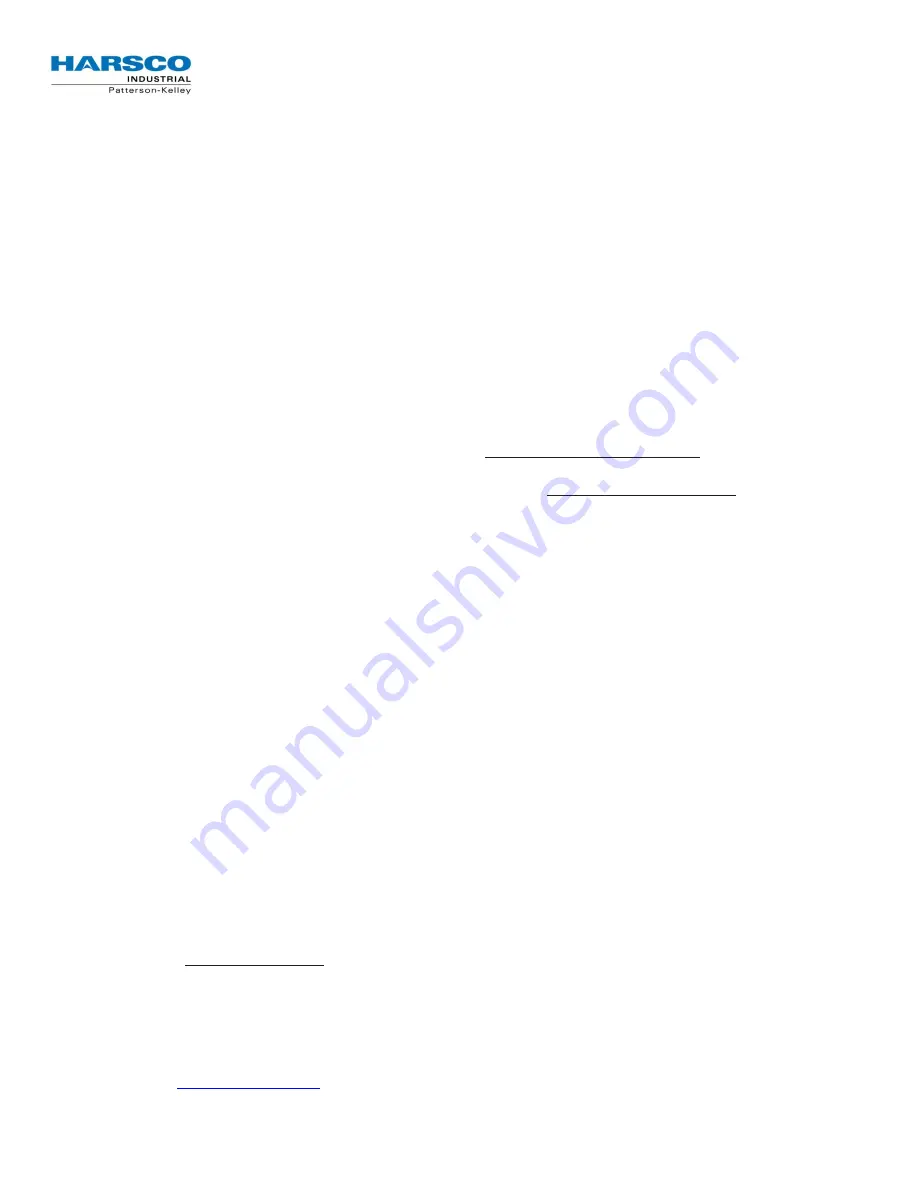
P-K SONIC
TM
Gas Fired Boiler
T
T
T
Technical Service 1.877.728.5351
echnical Service 1.877.728.5351
echnical Service 1.877.728.5351
echnical Service 1.877.728.5351
reduce the performance of the heat exchanger. Adequate circulation of good clean water is essential for
maximum efficiency and long life of the boiler.
3.7.2.2 Relief Valve Piping
Each boiler is supplied with a pressure-relief valve sized in accordance with ASME requirements. The relief
valve discharge must be piped to an acceptable drain at a safe point of discharge. Reducing couplings or
other restrictions are not permitted in the discharge line.
The SC-1500, SC-2000, SC-3000 and SC-4000 boilers require an ASME Section IV relief valve to be installed on
the top of the OUTLET (Supply) connection. The spindle of the relief valve must be vertical. The ASME Section IV
relief valves are available for purchase from Harsco Industrial, Patterson-Kelley.
The SC-3000 and SC-4000 boilers also require an ASME Section VIII relief valve to be installed somewhere on
the boiler or connecting piping before any isolation valve(s). A side port on the OUTLET (Supply) connection is
available for this purpose. The ASME Section VIII relief valve is provided with the SC-3000 and SC-4000
boilers for convenience.
3.7.2.3 Low Water Cut-Off
The boiler is furnished with a probe-type low water cut-off; no field piping is required. If the water level in the
boiler drops below the probe, the boiler will shut down and
LOCKOUT LOW WATER LEVEL
will be displayed on
the control panel. The low water cutoff circuit will automatically reset
when the low water condition clears;
however the boiler controls will retain the lockout condition until the reset button on the display is depressed.
Installation of external limit controls may be required by certain codes or in certain installations. Review
applicable local codes for details
.
N
OTICE
!
The low water cut-off probe only prevents boiler operation when the water level in
the boiler is insufficient. It does not detect low water conditions in other parts of
the system. Installation of high point vents or additional low water safety devices
to protect the system should be considered.
3.7.2.4 Drain Valve and Piping
A drain valve is factory installed in the boiler inlet (system return) piping. Prior to draining the boiler, electrical
power and gas supply must be turned off to the boiler, and the boiler must be isolated from the system at the
supply and return connections
.
N
OTICE
!
This drain valve is factory installed for draining of the boiler water only, not the
entire system. Draining of the system through the boiler will result in depositing
sediment from the system in the boiler which will result in poor heat transfer
characteristics of the boiler and early boiler failure.
3.7.2.5 Condensate Drain
The condensate is acidic (pH between 3.0 and 5.0) and may be corrosive to some building drain systems. A
condensate neutralization system may be required and is available from Harsco Industrial, Patterson-Kelley. If
the condensate drainage system is exposed to freezing temperatures, it must be field heat traced. The boiler
could generate up to one gallon of condensate per 100,000 BTU input. As an example, an
SC-4000
boiler at full
fire can produce 40 gallons per hour of condensate
. Disposal of condensate must comply with all state and
local codes.
3.8 Water Quality
The SONIC
TM
boiler heat exchanger is made of cast aluminum alloy. The heat exchanger requires proper
water conditions to remain efficient and function properly. Information of proper water treatment can be found
on our website
www.harscopk.com
type in search: For information, please refer to Harsco Industrial,