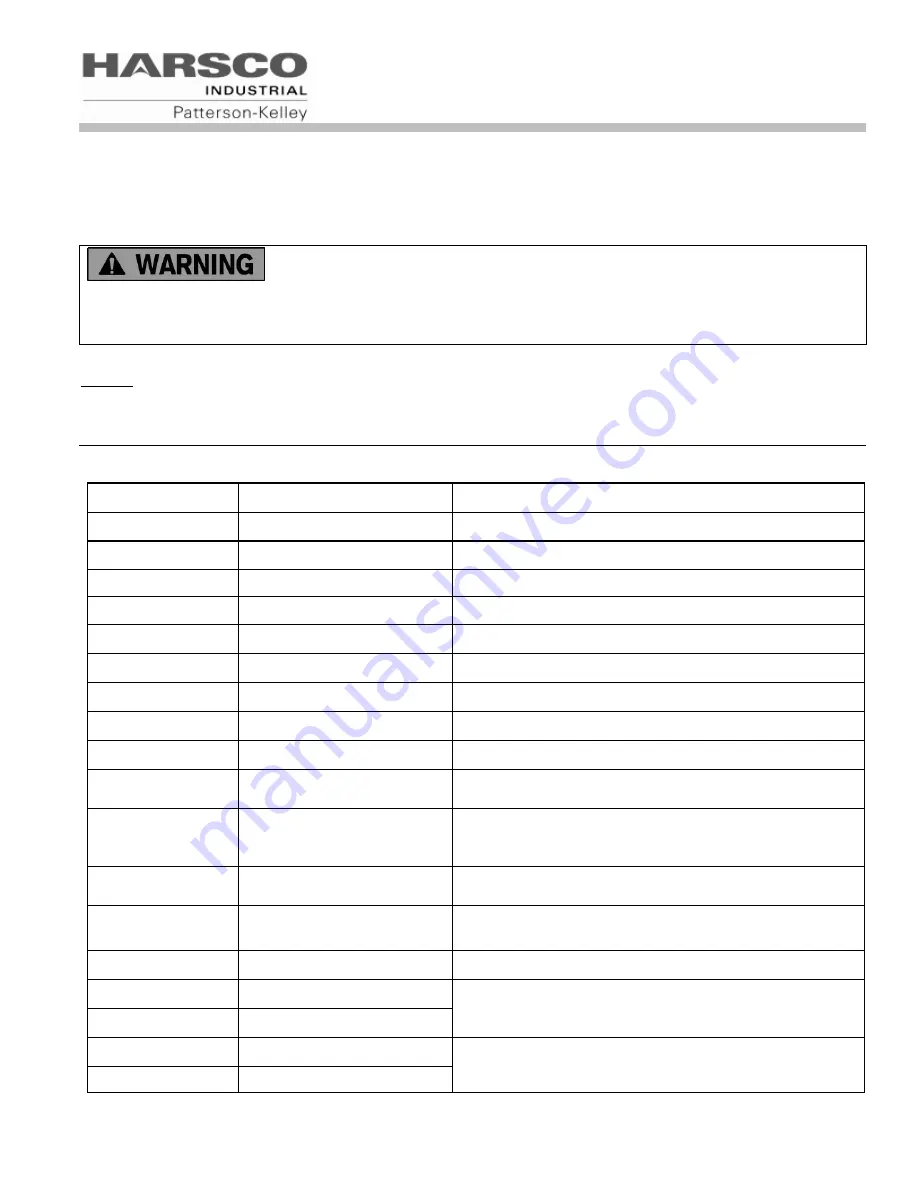
MACH® Gas-Fired Boiler
Page 47
6.0 PARTS/TECHNICAL SUPPORT
Spare parts and replacement parts can be ordered from Harsco Industrial, Patterson-Kelley by calling toll free (877)
728-5351. The fax number is (570) 476-7247. Technical information is also available at the above number and at
the Harsco Industrial, Patterson-Kelly website www.harscopk.com.
Use of Non-Factory-Authorized replacement parts are not recommended for this
equipment. All control components are engineered for safety and are designed to work in unison with
each of the other components. Use of non-factory-authorized replacement parts jeopardizes the
functionality of the safety features as well as the performance of the boiler.
When ordering replacement parts please have the
model number
and
serial number
of your boiler available.
Typical schematic drawings are shown on the following pages. Drawings specific to your particular boiler can also be
supplied by your local Harsco Industrial, Patterson-Kelley representative.
6.1
W
IRING
D
IAGRAMS
6.1.1 Terminal Block Assignments
– High Voltage Circuit (TB2)
Terminal Number
Label
Description
1
120 VAC LINE
Boiler Supply Power, 120 VAC, 1 ph , 60 Hz
2
120 VAC NEUTRAL
Boiler Supply Neutral, 0 VAC
3
120 VAC NEUTRAL
Neutral for use with TB2-10, Switched Output
4
120 VAC NEUTRAL
Neutral for use with TB2-11, 3 Way Valve
5
120 VAC NEUTRAL
Neutral for use with TB2-12, DHW Pump Contactor
6
120 VAC NEUTRAL
Neutral for use with TB2-13, CIRC Pump Contactor
7
120 VAC NEUTRAL
Neutral for use with TB2-14, Damper Output
8
GROUND
Boiler Supply Ground, 0 VAC
9
GROUND
Boiler Supply Ground, 0 VAC
10
120VAC SW OUTPUT
120V AC output when boiler is switched on (4 amp
max)
11
120VAC 3 WAY VALVE
120V AC output during CH Mode. 3 way valve is
normally closed (not powered) for DHW, and powered
open for CH Mode.
12
120VAC DHW PUMP CNTR 120V AC output when boiler is in DHW Mode (pilot duty
only)
13
120VAC CIRC PUMP CNTR 120V AC output when boiler is in CH Mode (pilot duty
only)
14
120VAC DAMPER
120V AC output when boiler is enabled (pilot duty only)
15
MASTER ALARM RELAY
This circuit closes when the boiler is in an alarm state
16
MASTER ALARM RELAY
17
FLAME DETECTED RELAY This circuit closes when the boiler is firing
18
FLAME DETECTED RELAY
Содержание MACH C1500GG
Страница 49: ...MACH Gas Fired Boiler Page 49 6 1 3 MACH Boiler C1500GG C2000GG Wiring Diagram ...
Страница 50: ...MACH Gas Fired Boiler Page 50 6 1 4 Dual Fuel Control Wiring MACH C1500GG C2000GG ...
Страница 58: ...MACH Gas Fired Boiler 58 8 3 MAINTENANCE LOG Date Hi Low Fire O2 CO CO2 Stack Temp pH Action By ...