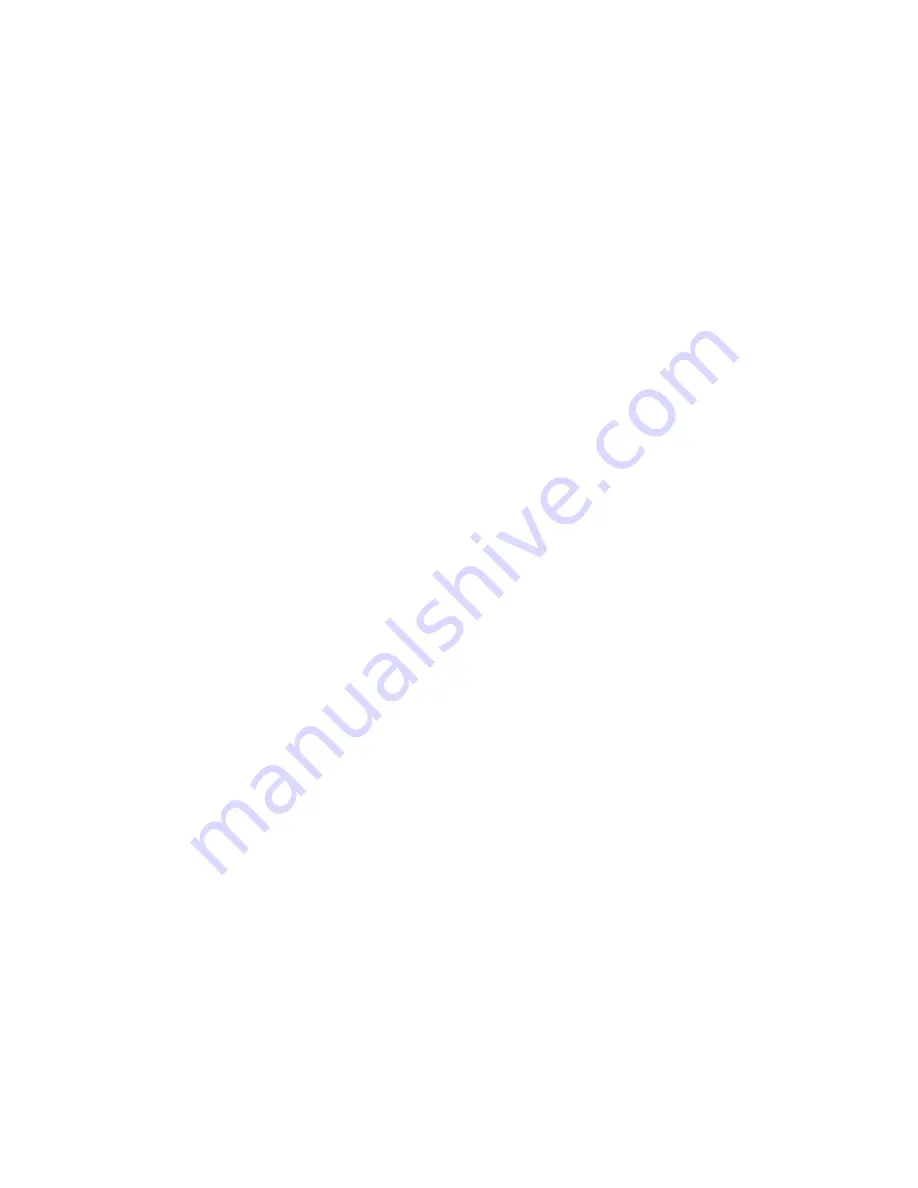
MAKE CERTAIN that all guards are in good condition and are functioning properly before op-
erating the machine.
INSPECT ALL SAFETY DEVICES AND GUARDS to make certain that they are in good con-
dition and are functioning properly before the cycle is started.
CHECK THE POSITION of the tool top plate before pressing the Cycle Start push button.
CHECK SETUP, TOOLING, AND SECURITY OF THE WORKPIECE if the machine has been
OFF for any length of time.
DRY CYCLE a new setup to check for programming errors.
MAKE CERTAIN that you are clear of any “pinch point” created by moving slides before start-
ing the machine.
DON’T OPERATE any equipment while any part of the body is in the proximity of a potentially
hazardous area.
DON’T REMOVE CHIPS with hands. Use a hook or similar device and make certain that all
machine movements have ceased.
BE CAREFUL of sharp edges when handling a newly machined workpiece.
DON’T REMOVE OR LOAD a workpiece while any part of the machine is in motion.
DON’T OPERATE ANY MACHINE while wearing rings, watches, jewelry, loose clothing, neck-
ties, or long hair not contained by a net or shop cap.
DON’T ADJUST tooling or coolant hoses while the machine is running.
DON’T LEAVE tools, workpieces or other loose items where they can come in contact with a
moving component of the machine.
DON’T CHECK finishes or dimensions of workpiece near running spindle or moving slides.
DON’T JOG SPINDLE in either direction when checking threads with a thread gage.
DON’T ATTEMPT to brake or slow the machine with hands or any makeshift device.
ANY ATTACHMENT, TOOL, OR MACHINE MODIFICATION not obtained from Hardinge Inc.
must be reviewed by a qualified safety engineer before installation.
USE CAUTION around exposed mechanisms and tooling especially when setting up. Be care-
ful of sharp edges on tools.
DON’T USE worn or defective hand tools. Use the proper size and type for the job being per-
formed.
USE ONLY a soft-faced hammer on tooling and fixtures.
DON’T USE worn or broken tooling on machine.
MAKE CERTAIN that all tool mounting surfaces are clean before mounting tools.
INSPECT ALL CHUCKING DEVICES daily to make certain that they are in good operating
condition. Replace any defective chuck before operating the machine.
USE MAXIMUM ALLOWABLE gripping pressure on the chuck. Consider weight, shape, and
balance of the workpiece.
M-448B
iii
Содержание Talent 6/45
Страница 9: ...NOTES M 448B vii...
Страница 10: ...NOTES viii M 448B...
Страница 17: ...NOTES M 448B 1 7...
Страница 18: ...NOTES 1 8 M 448B...
Страница 27: ...NOTES M 448B 2 9...
Страница 28: ...NOTES 2 10 M 448B...
Страница 32: ...NOTES 3 4 M 448B...
Страница 43: ...NOTES M 448B 4 11...
Страница 44: ...NOTES 4 12 M 448B...
Страница 49: ...NOTES M 448B 5 5...
Страница 50: ...NOTES 5 6 M 448B...
Страница 61: ...NOTES M 448B 6 11...
Страница 62: ...NOTES 6 12 M 448B...
Страница 65: ...NOTES M 448B A1 3...
Страница 66: ...NOTES A1 4 M 448B...
Страница 68: ...A2 2 M 448B Figure A2 3 Coolant Pump Electrical Connection TALENT 6 45 and 8 52 Lathes TP6027...
Страница 73: ...M 448B A2 7 Figure A2 10 Tailstock Quill Hydraulic Valves TALENT 8 66 and 10 78 Lathes TP6040...
Страница 77: ...M 448B A2 11 Figure A2 15 Collet Closer and Tailstock Foot Switches TALENT 8 66 and 10 78 Lathes TP6025...
Страница 78: ...A2 12 M 448B Figure A2 16 Tailstock Hydraulic Valves TALENT 6 45 and 8 52 Lathes TP5240...
Страница 79: ...M 448B A2 13 Figure A2 17 Tailstock Hydraulic Valves TALENT 8 66 and 10 78 Lathes TP6045...
Страница 86: ...A2 20 M 448B Figure A2 24 Internal Power Case View Relay Panel TP5208A...
Страница 91: ...M 448B A2 25 Figure A2 29 Internal Power Case View Service Entrance to Power Case TP5217A...
Страница 92: ...A2 26 M 448B Figure A2 30 Internal Power Case View Fuse and Contactor Panel TP5209A...
Страница 97: ...M 448B A2 31 Figure A2 35 Pump for Through Tool Coolant TP5231...
Страница 98: ...A2 32 M 448B Figure A2 36 Spindle with Chuck Removed TP5236...
Страница 99: ...M 448B A2 33 Figure A2 37 Spindle with Chuck Installed TP5243...
Страница 100: ...A2 34 M 448B Figure A2 38 Tailstock Assembly TALENT 6 45 6 45SV 8 52 and 8 52SV Lathes TP5754...
Страница 101: ...M 448B A2 35 Figure A2 39 Tailstock Assembly TALENT 8 66 and 10 78 Lathes TP6044...
Страница 102: ...A2 36 M 448B Figure A2 40 Z Axis Drive Motor TALENT 8 66 and 10 78 Lathes TP6049...
Страница 103: ...NOTES M 448B A2 37...
Страница 104: ...Hardinge Inc Elmira New York 14902 1507 USA Phone 607 734 2281 FAX 607 734 8819 www hardinge com...