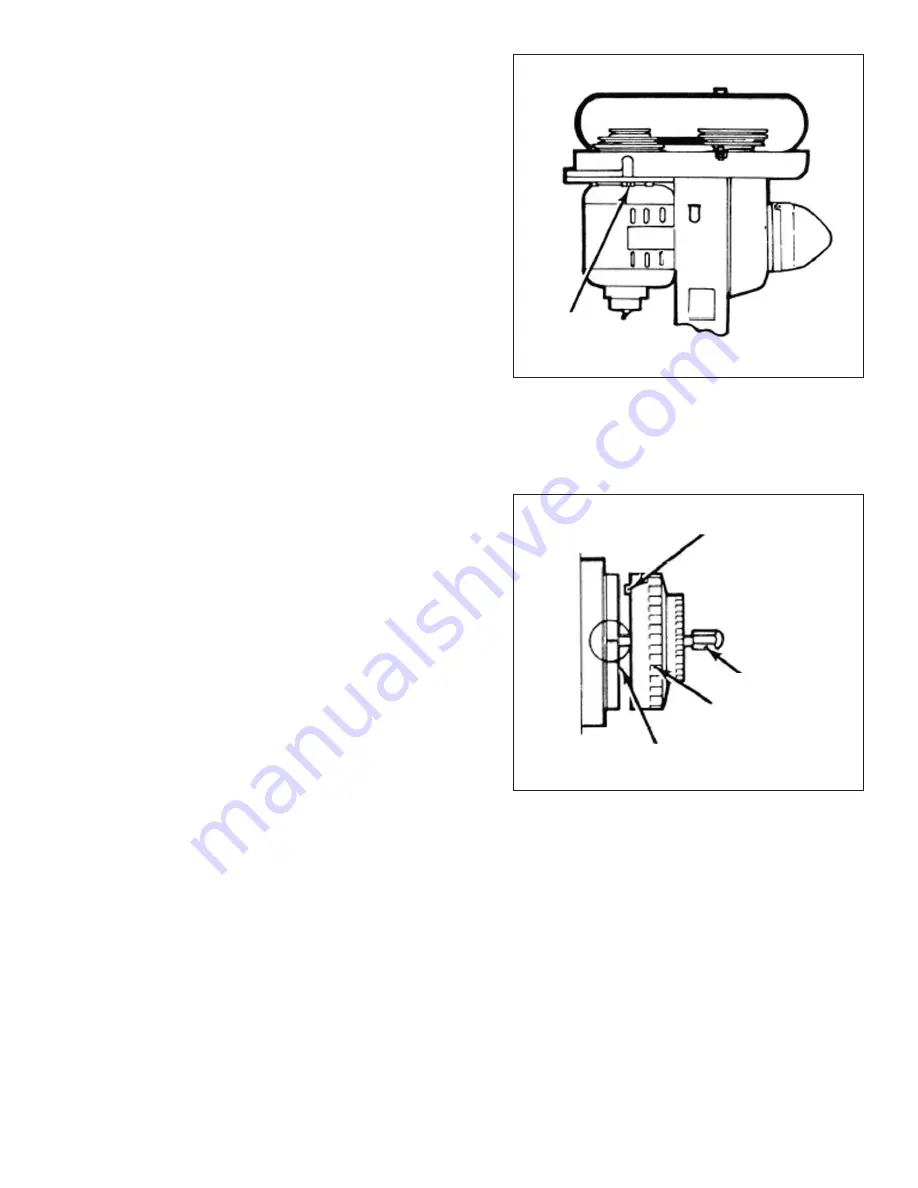
To Change Speed
1. Disconnect power from head.
2. Loosen the two motor locknuts (see Figure
2.33).
3. Slide motor forward.
4. Position vee belt on appropriate pulleys.
5. Slide motor to rear to tension vee belt.
6. Tighten the two motor locknuts.
With 50 cycle 1425 rpm 60, 85, 120, 170, 245 350
strokes per minute.
To Change Stroke
1. Loosen locknut (see Figure 2.34).
2. Turn stroke dial to required setting.
3. Press dial home to engage pin.
4. Tighten locknut.
- NOTE -
Before operating attachment, ensure
locknut is tight.
M-450
2-19
Figure 2.33 - Changing E-Head Speed
Locknuts
TP5317
Figure 2.34 - Changing E-Head Stroke
Engage Pin
Locknut
Stroke Dial
Setting Datum
TP5318
Содержание SERIES I
Страница 22: ... NOTES M 450 2 21 ...
Страница 23: ......