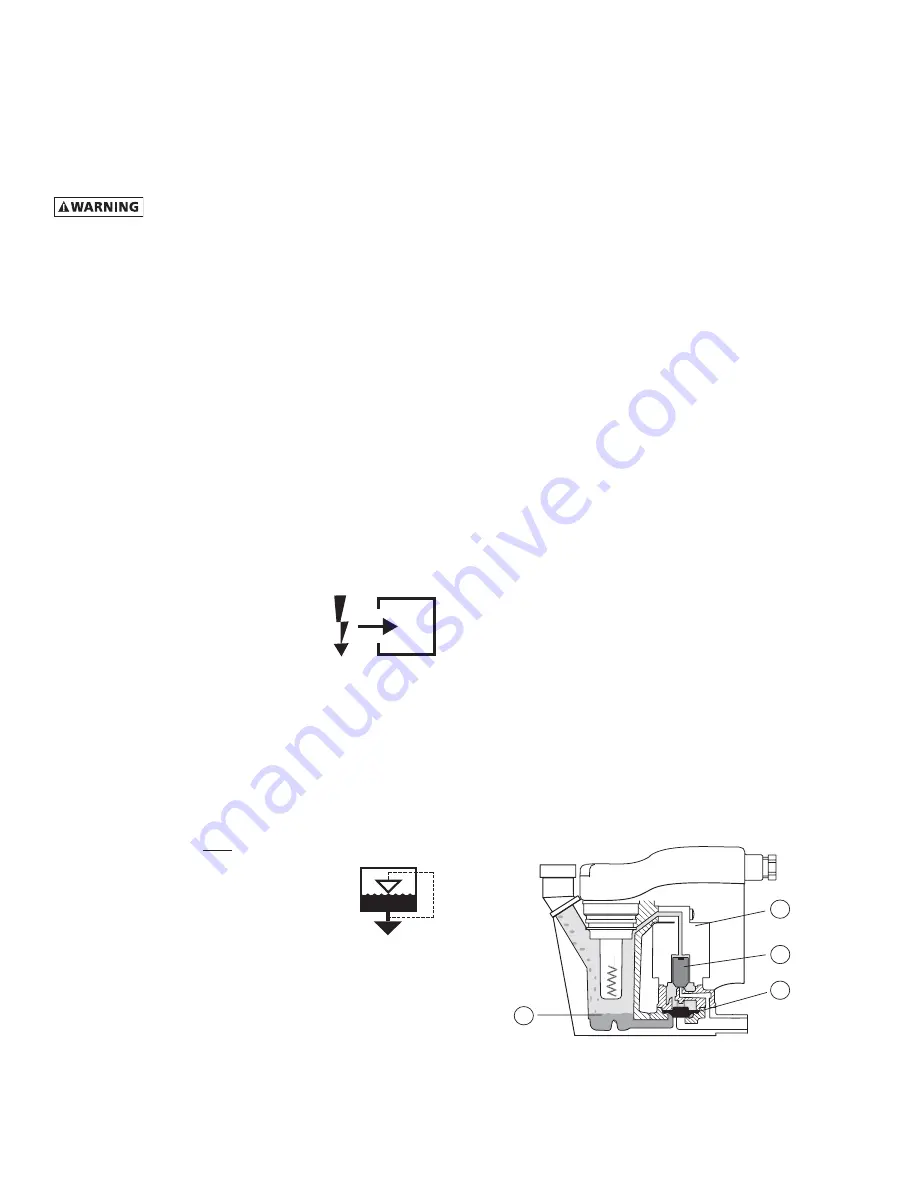
4
1.2 Mounting
Mount the dryer on a level solid surface. Holes are provided in
the dryer base to permanently mount the dryer to the floor.
1.3 Piping connections
A.
Air Inlet - Connect compressed air line from air source to
air inlet. (See callout drawing on page 3 for air in/outlet
connection locations)
Refer to Serial Number Tag for maximum
working pressure. Do not exceed dryer’s Maximum Working
Pressure.
NOTE: Install dryer in air system at highest pressure possible
(e.g. before pressure reducing valves).
NOTE: Install dryer at coolest compressed air temperature
possible. Maximum inlet compressed air temperature: 120°F
(49°C). If inlet air exceeds this temperature, precool the air with
an aftercooler.
B.
Air Outlet - Connect air outlet to downstream air lines.
C.
Bypass piping - If servicing the dryer without interrupting
the air supply is desired, piping should include inlet and
outlet valves and an air bypass valve.
D.
Water-cooled models - cooling water inlet and outlet
1.
Connect cooling water supply to cooling water inlet.
2.
Connect cooling water return line to cooling water
outlet connection.
NOTE: Strainer and water regulating valve are supplied on
water-cooled models. Also, it is recommended to add water
inlet/outlet temperature and pressure gauges to the water
piping.
1.4 Electrical connections
IMPORTANT: Use copper supply wires only.
A.
Dryer is designed to operate on the
voltage, phase, and frequency listed on
the serial number tag.
B.
Electrical entry is through a hole in the cabinet, located in
the separator compartment near the top, and in the
electrical enclosure. Connect power source to the terminal
strip in the electrical enclosure as shown on the electrical
schematic included with the dryer.
If optional disconnect is supplied, use entry hole in
disconnect enclosure.
NOTE: Refrigeration condensing unit is designed to run
continuously and should NOT be wired to cycle
on/off with the air compressor.
1.5 Electronic Demand Drain
A.
An automatic electric demand drain (EDD)
discharges condensate removed by the
separator.
B.
All dryer models are supplied with one EDD. Models with
the additional (optional) oil removal filter are supplied with
a second EDD.
C.
At installation install the petcock on the bulkhead fitting for
the manual drain. For manual draining, convenient dryer
depressurization, and EDD service, a three-way valve at
the bottom of the moisture separator and before the EDD
is installed. For manual draining, turn the valve handle so it
is in a horizontal position. Open the petcock on the side of
the dryer base pan to discharge the condensate or to
depressurize the dryer if it has been bypassed. The
petcock can be left in a throttled (partially opened) position
should there be a problem with EDD.
The drains are piped to fittings in the back leg of the unit.
Condensate should be piped from this fitting to an open
vented floor drain or sump.
NOTE
:
Discharge is at system pressure. Drain line should be
anchored.
NOTE
:
Condensate may contain oil. Comply with applicable
laws concerning proper disposal.
D.
Verify that isolation valves are open. If the drain fails to
discharge after the valve is energized, the electronic
control circuit will repeatedly energize the valve in an
attempt to clear the discharge port. If, after 60 seconds,
the drain still fails to discharge, the control circuit then
switches to the alarm mode. In this mode the valve is de-
energized and the red alarm light is activated on the drain
and the dryer controller. The valve is then automatically
energized every 4 minutes for 5 seconds. Check the drain
operation. Push drain (push-to-test) button on the Energy
Management Monitor control board to energize drain. A
flow of condensate and/or air should be present at the
drain outlet. The alarm mode automatically clears after the
drain returns to normal operation.
E.
Condensate enters the reservoir (1) through the inlet port.
When the condensate level in the reservoir covers the
capacitance sensor, an electronic signal is sent to the solid
state countdown processor. The processor delays the
opening of the solenoid valve for a given period of time.
Once the time has elapsed, the solid state processor
transmits information to energize the coil in the solenoid
valve (2). The magnetic force of the coil causes the
solenoid core (3) to move, closing the pilot air supply line
and opening the pilot air exhaust line. After the pilot air
above the diaphragm (4) is vented, pressure in the
reservoir opens the discharge port and forces the conden-
sate through the discharge port and outlet piping.
1
2
3
4
Содержание HPRP 1000
Страница 19: ...19 NOTES...