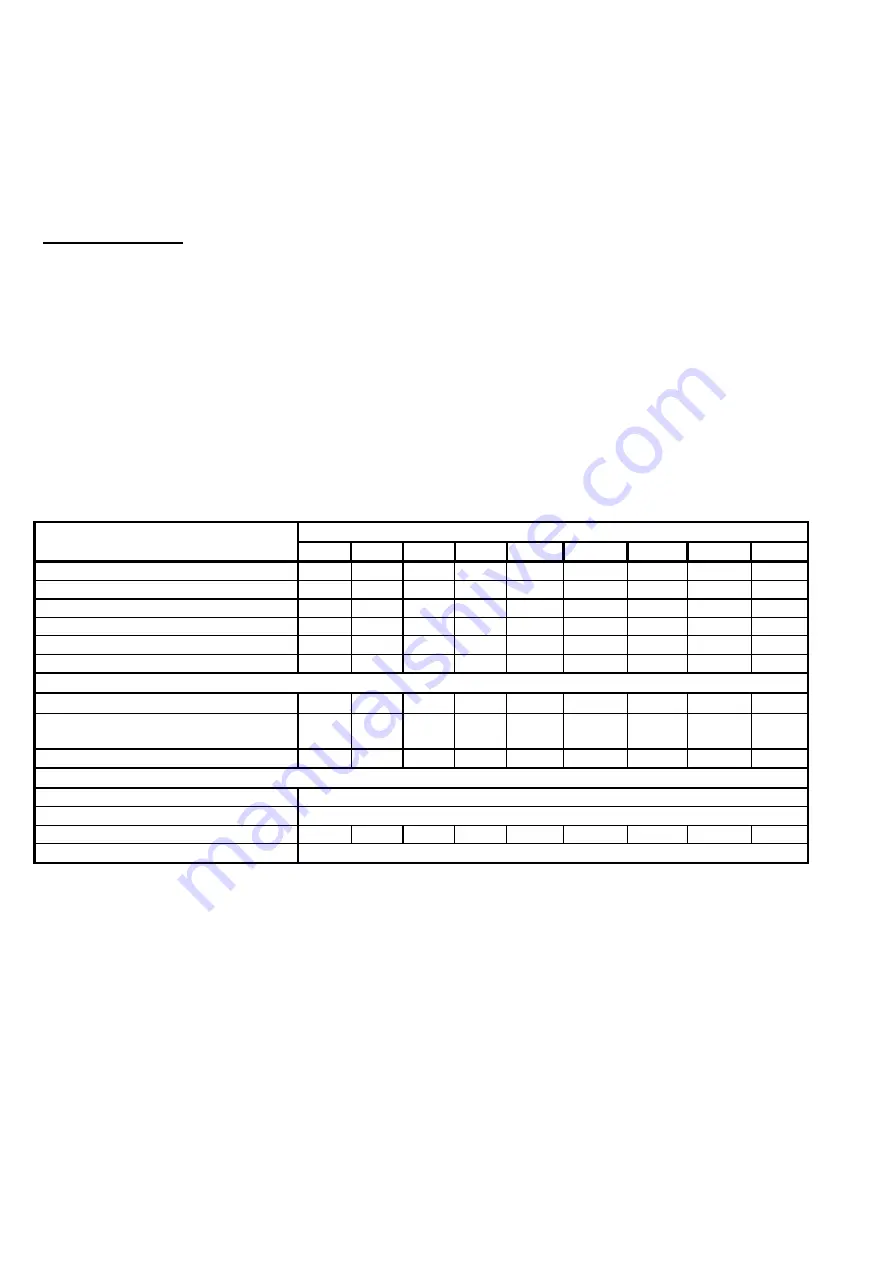
HAMWORTHY HEATING LTD. PUREWELL PERMANENT IGNITION 500001090/B
30
APPENDIX ‘A’ TO INSTALLER’S GUIDE
INFORMATION RELATING TO PROPANE FIRING
NOTE!
LPG FUELS - IT IS STRONGLY RECOMMENDED THAT, ON LPG INSTALLATIONS, GAS DETECTION
EQUIPMENT BE FITTED. THIS EQUIPMENT SHOULD BE POSITIONED NEAR THE BOILER AND AT LOW
LEVEL. IT IS ALSO IMPORTANT THAT THE SPACE HOUSING THE BOILER IS ADEQUATELY
VENTILATED AT HIGH AND LOW LEVEL. REFER TO MAIN INSTALLER’S GUIDE.
1.0 INTRODUCTION
The operation of the Purewell range of boilers on
LPG-Propane (3
rd
family)I
3P
is similar to that on
Natural Gas (2
nd
family)I
2H
and the design and
installation details described in the main body of the
installer’s guide should be followed. There are
however, differences in the construction and setting
of the propane fired boiler which are as follows: -
a) The pilot injector marked 56/42A for Natural Gas
is replaced with an injector for Propane, marked
0.23P (perm/pilot only).
b) The main gas injectors (located in the gas
manifold) are replaced with those detailed the
Performance and General Data Information table
below.
c) The nominal gas inlet pressure for propane
should be 37mbar.
d) Relevant labels are replaced to indicate the
appropriate gas for which the boiler is set up to fire.
The following tables and paragraphs, using the
same numbering system as the main installer’s
guide, highlight the different values and procedures
to be used when firing propane, and should be
used in conjunction with the Main Installer’s Guide.
Performance and General Data Information
Model
GENERAL DATA
40
50
60
70
80
95
100
105
120
Boiler Input kW (Gross)
49.3
63.4
74.5
88.4
101.0
120.0
126.0
132.0
150.0
Boiler Input kW (Net)
45.4
58.4
68.6
81.4
93.0
110.5
116.0
121.6
138.1
Boiler Output kW
40
50
60
70
80
95
100
105
120
Gas flow rate
m
3
/h
1.9
2.4
2.8
3.3
3.8
4.5
4.7
5.0
5.7
kg/h
3.5
4.6
5.3
6.3
7.2
8.6
9.0
9.5
10.7
Gas manifold pressure
mbar
15
15
15
15
17
29
23
25
24
FLUE DATA
Approx. flue gas temp
q
C
180
190
190
200
210
200
200
210
190
Approx. flue gas vol. @
68
83
81
97
110
132
147
147
175
9% CO
2
& NTP. m
3
/h
CO
2
%
8.0
9.0
11.0
11.0
11.0
11.0
10.0
11.5
10.0
GAS DATA
Nominal gas inlet pressure
mbar
37
Maximum gas inlet pressure
mbar
45
Injector marking/ Dia.
mm
2.1
2.3
2.6
2.8
2.9
2.4
2.7
2.7
2.9
Pilot burner(Perm/Pilot)
Q349A-1034 (with 0.23P injector)
11.5 BOILER CHECKS PRIOR TO LIGHTING
Ensure that the gas supply is connected but turned
to the ‘OFF’ position. Remove the cover on the low
gas pressure switch and connect a multi-meter
across terminals ‘C & NO’ - to measure circuit
continuity.
Connect a manometer suitable for 50mbar to the
pressure tapping on the switch body and gradually
turn ‘ON’ the gas supply. The switch should operate
at approximately 20mbar - noted on the multi-
meter.
Turn ‘OFF’ the gas supply and undo the pressure
test point on the gas valve inlet and allow the gas
pressure to fall. The switch should operate at
approximately 20mbar - noted on the multi-meter.
11.5.1 Gas Pressure Adjustment
After approximately 30 minutes of normal firing,
connecting a manometer to test point on the
manifold should check the manifold gas pressure.
Minor adjustments to the appliance governor may
be necessary to correct for site gas pressure
conditions.
NOTE:
The above is a first order check. Final
setting must be made using a gas meter.