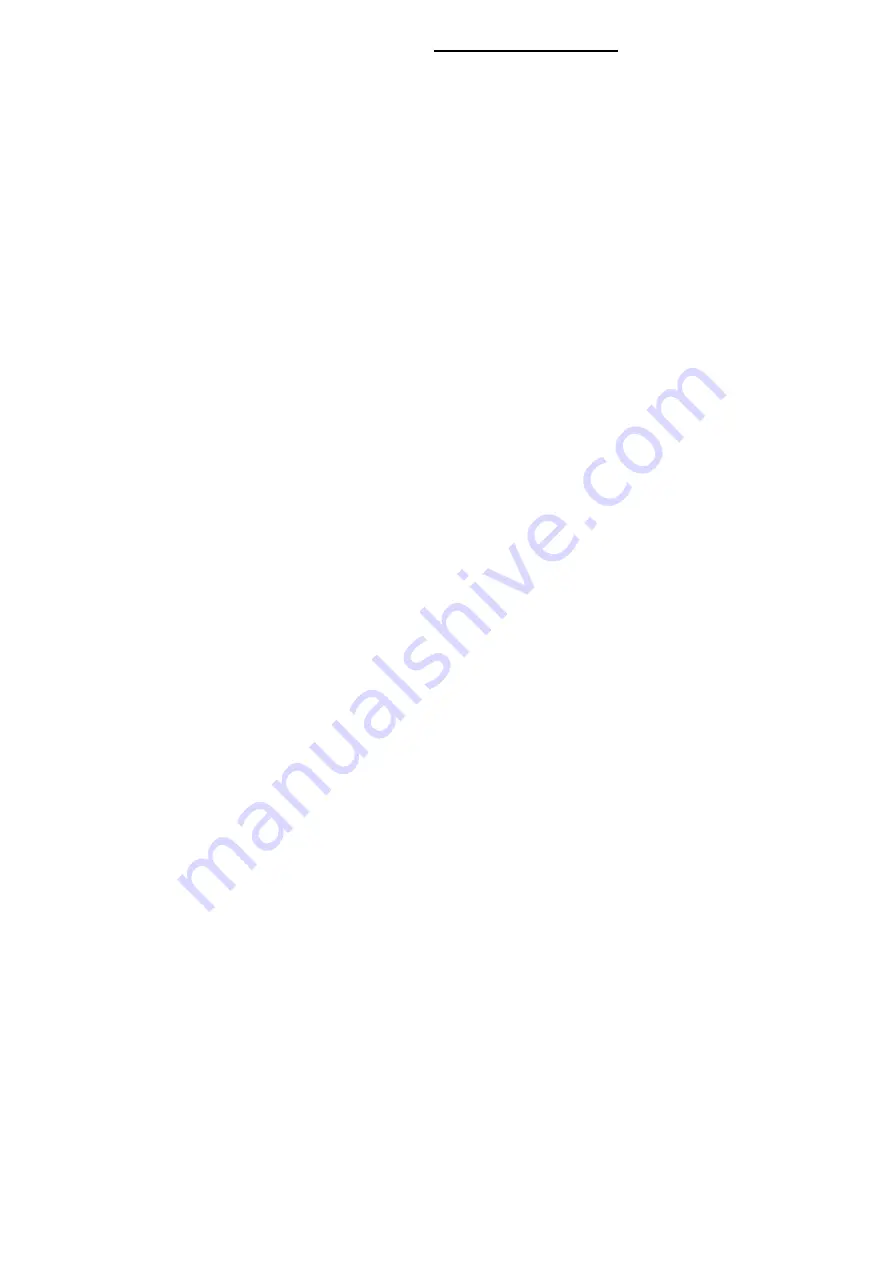
HAMWORTHY HEATING LTD. PUREWELL PERMANENT IGNITION 500001090/B
8
Note! A high temperature control kit is available
incorporating a new temperature limiter, and
instructions. For further information contact
Hamworthy Heating for details.
8.10.2 Water Flow Controls
Any external mixing valves or similar controls should
always ensure that the minimum water flow rate
shown in Figure No. 2 is maintained.
8.10.3 Frost Protection
Consideration should be given to fitting a frost
thermostat set at approximately 4°C.
8.11 Unvented Pressurised Systems
See Figure No. 8 for typical layout of a Pressurised
(Un-vented) Hot Water System.
In order to correctly size a Pressurisation Unit for
any Heating System certain parameters are
required. These are: -
1) Static height of highest component in system.
2) System volume - if not known a general rule of
thumb of 10 litres/kW installed boiler power can be
used.
3) Maximum flow temperature, i.e. most systems run
at 82°C.
4) Maximum system hot working pressure, generally
given in barg.
From the above information Hamworthy Heating can
size the pressure unit and also the expansion vessel
required.
Care must be taken in sizing expansion vessels to
ensure maximum acceptance factors are not
exceeded. Normally manufactures of vessels
impose a limit of 0.5. This value must not be
exceeded at any time during the operation of the
boiler: this includes the over pressure condition
should a safety valve lift.
Consideration should also be given to sizing of the
safety valve(s) in the system. See
BS 6759
: Part 1
for information.
See also
BS 6880
: Part 1 for design considerations.
8.12 Modular Boiler Control Schemes
For Modular applications Hamworthy Heating can
supply a unique boiler management control system
called the 'Marshall HE' - see Figure No. 8. This
system comprises of a remote master control unit,
which houses the main interface processor and will
control up to 8 stages. For further information
contact Hamworthy Heating for details.
9.0 ELECTRICAL SUPPLY
WARNING: THIS APPLIANCE MUST BE
EARTHED.
Wiring external to the boiler must be installed in
accordance with the IEE Regulations and any local
regulations, which apply. Wiring must be completed
in heat resistant 3-core cable. (Size 1.0mm² csa).
Boilers are normally supplied suitable for 230 volts,
50Hz. Control panel fuse rating is 2A. External
fuses should be 6A for all single boiler sizes.
The method of connection to the mains electricity
supply must facilitate complete electrical isolation of
the single boiler with a contact separation of at least
3mm in all poles.
This appliance must be isolated from the mains
electricity supply in the event of electric arc
welding being carried out on any connecting
pipework.
A mains isolator must be provided adjacent to the
boiler in a readily accessible position. The supply
should only serve the boiler.
NOTE!
There is no facility on the Purewell boiler for
the connection of any remote signals, alarms or
control. Any controls MUST interrupt the supply to
the boiler. Accordingly, any pumps MUST be wired
to the control to achieve operation and desired
overrun.
NOTE!
When an optional On/Off Primary Flue
Damper is fitted, there is a facility for the connection
of a remote start/stop loop. This loop requires a volt
free contact for operation. Power is supplied by the
boiler to allow this circuit to function. Refer to the kit
instructions for wiring details. Further details
regarding connection to the electricity supply are
given in
BS EN 60335, Part 1 or BS 3456, Part 201
.
Refer to Figure No. 12 for typical site wiring
connections. See
BS 6644
for further information.
9.1 Site Wiring
Access to the controls is achieved by rotating the ¼
turn latch and removing the door. A 20mm dia.
knockout is provided in each side panel if required
for electrical connections. Any other routing of site
cables should ensure that cables do not pass close
to the boiler flue hood or that any cable trunking
does not interfere with normal air circulation and
supply ducts.
An IEC 3 pin fused (2A) plug and socket
arrangement is utilised for the site terminal
connections. Care must be taken to ensure correct
connections are made to the relevant terminals
before applying power.
Refer to Figure No. 12 for typical wiring diagram.
If the optional Flame Failure kit is fitted, the electrical
input/output cannot be interfaced with the boiler
controls. Separate provisions must be made for the