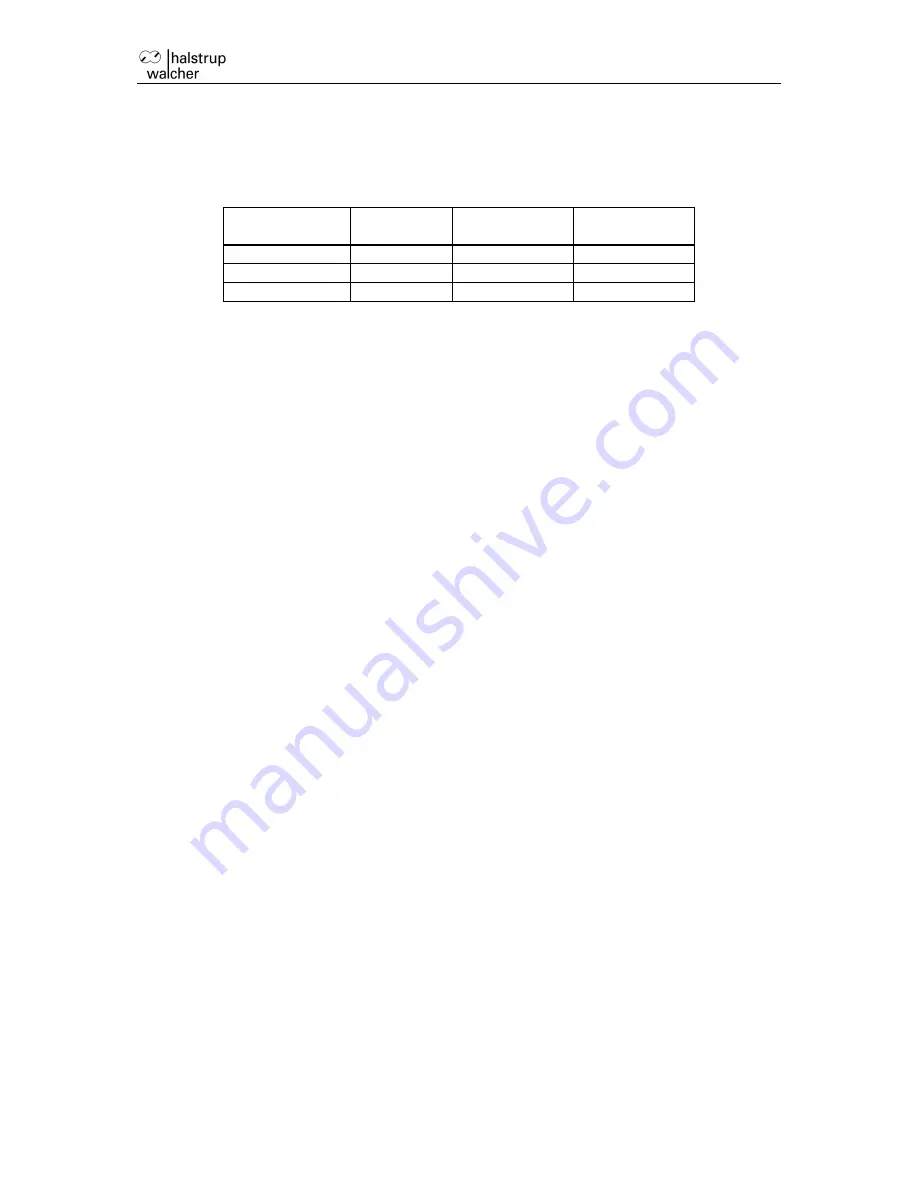
Instruction Manual PSx3xxPL
27
The denominator factor serves as a simple means of setting the spindle pitch and
resolution.
The numerator factor is primarily used for setting “unlevel” resolutions.
Examples:
Spindle pitch
Resolution
Numerator
factor
Denominator
factor
4 mm
1/100 mm
400
400
1 mm
1/100 mm
400
100
2 mm
1/10 mm
400
20
Numerator and denominator factors may take on values between 1 and 10,000.
h) Drag error monitoring
During a positioning run, the device compares the computed target position with the
current actual val
ue. If the difference is larger than the ‘drag error’ value (SDO
#2005), the device sets the corresponding bit in the status word. This situation is
especially likely to occur if external factors (required torque, voltage to motor too low)
prevent the device from achieving the target rpm
By setting SDO #2005 to 0 the drag error monitoring can be disabled.
i) Drag error correction
With SDO #2046 the drag error correction can be enabled. With this feature enabled,
the drive will raise or lower the target speed proportional to the drag error by the
configured value. The drive attempts under consideration of the configured maximum
current to compensate the drag error which has developped by controlling the target
speed to a value which lays slightly above or below the specified value of the target
speed (SDO #2012).
By setting SDO #2046 to 0 the drag error correction can be disabled.
Drag error monitoring and correction take effect always except during a braking
operation when approaching a target position or when aborting a positioning. The
actual target speed when accelerating is determined by the actual speed at the
beginning of the positioning and the acceleration setting (SDO #201C).
j) Abort run when the master fails
If the connection to the master is interrupted during a positioning run, the master
cannot abort an actual run. In order to generate an automatic run abort in this case,
there’s a mechanism implemented in the drive that monitors the communication to the
Powerlink Managing Node (e.g. the bus master). In case of a timeout, the drive will
abort any positioning (if bits 1-0 of SDO #2049 are set to 01, which is the default
value). If the connection contains valid data after its re-establishment, the drive might
continue to move immediately (where applicable).
Instead of aborting any positioning if the connection to the master is interrupted,
alternatively a continuation of the run or a run to a configurable save position might be
configured with the help of SDOs #2049, #204A and #204B.
Содержание PS*3**PL series
Страница 28: ...Instruction Manual PSx3xxPL 28...
Страница 33: ...Instruction Manual PSx3xxPL 33...