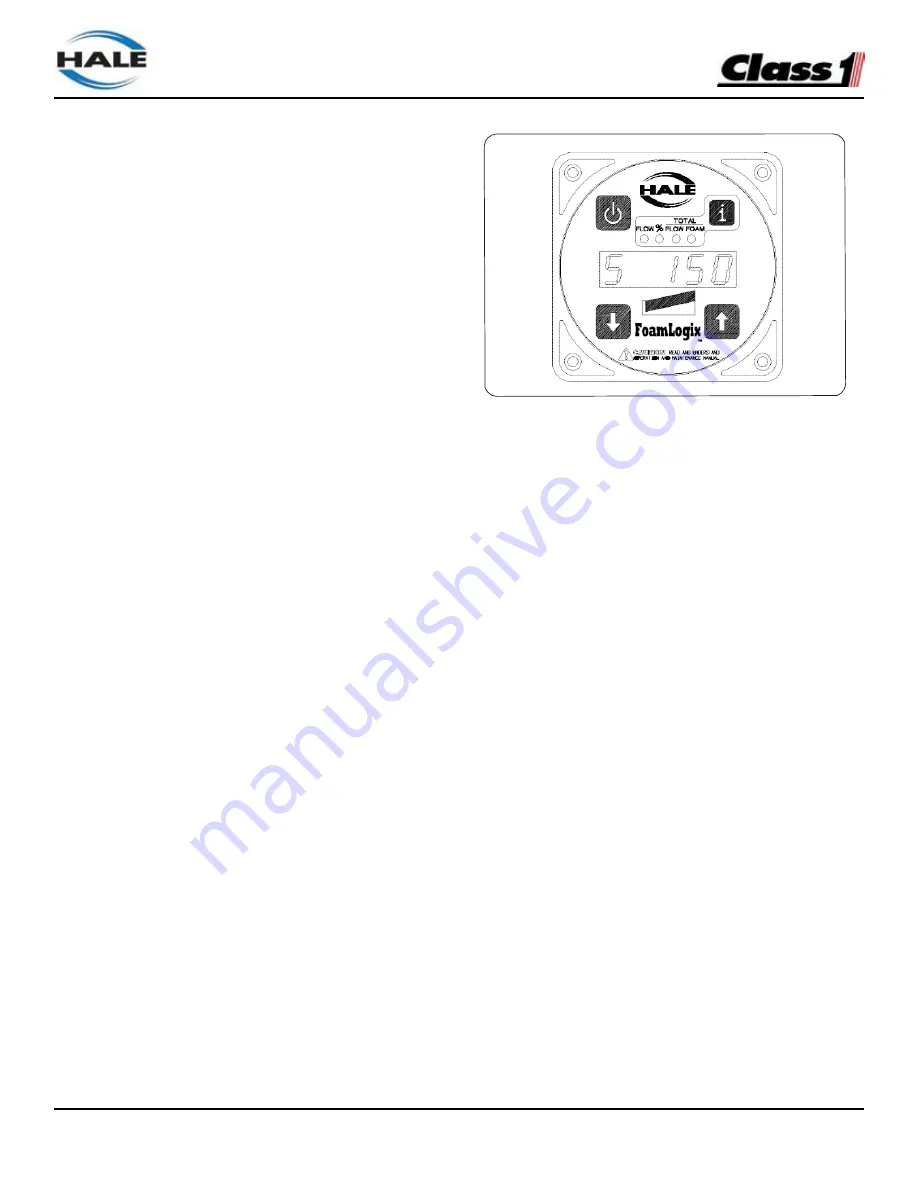
FoamLogix, Model 2.1A and 1.7AHP Class
“A”
Electronic Foam Proportioning Systems
50
DO NOT PUMP WATER WITH THE HALE FOAM-
LOGIX FOAM PUMP FOR MORE THAN ONE (1)
MINUTE. DO NOT ATTEMPT TO CALIBRATE FOAM
PUMP FEEDBACK SENSOR WITH OTHER THAN
END USER SPECIFIED FOAM CONCENTRATE.
MAKE SURE THE BYPASS VALVE IS IN THE
BYPASS POSITION WHEN PUMPING WATER
WITH THE FOAM PUMP.
1. Upon initial power-up with the foam tanks empty,
the display on the control unit alternates between
0
and
Lo A
, indicating the foam tank is empty.
Fill the foam concentrate tank with WATER. The
Lo
A
indication clears from the display, indicating the
low tank level sensor is operating properly.
2. Place the bypass valve to the
BYPASS
position
to check foam pump operation. Place a calibrated
five gallon container at the discharge of the bypass
hose.
3. Place the system in simulated flow mode by
pressing the SELECT DISPLAY button
(
i
) until the LED under
FLOW
lights. Then
press both up
and down
buttons
simultaneously.
Set simulated flow value to
100
GPM by
pressing UP
or DOWN
button. The
display shows
S
at the left most position to
indicate the simulated flow. (See Figure
24:
“Simulated Flow Display.”)
4. Press the (
i
) button until the LED under
%
FOAM
lights. Set foam concentrate injection rate to
1.0
using the UP
or DOWN
button.
5. Cycle the (
i
) button until the LED under
TOTAL
FOAM
lights. Press the
ON
button to energize the
Hale FoamLogix system.
Figure 24: Simulated Flow Display
Observe the discharge at the bypass hose to make
sure the foam pump is operating.
6. After one minute press the
ON
button again to
STOP the foam pump. Approximately one gallon (3.8
liters) of water should discharge into the container.
The TOTAL FOAM display reads approximately
1.0
.
7. Exit the simulated flow mode by selecting the
FLOW
display and pressing both up
and down
buttons simultaneously.
8. Drain water from foam tanks and concentrate
lines and return the bypass valve to the
INJECT
position.
9. Verify operation of the flow sensor. Also calibrate
the flow sensor using the calibration procedures.
See heading
“User calibration” beginning on page
53.
This completes the Hale FoamLogix system
operation checks accomplished at the system
installer facility.
Foam pump feedback calibration along with
setting of user specified default simulated flow and
concentrate injection rates should be accomplished
upon delivery to the end user using actual end user
specified foam concentrates and default values.
Содержание FoamLogix 1.7AHP
Страница 4: ...FoamLogix Model 2 1A and 1 7AHP Class A Electronic Foam Proportioning Systems 4 NOTES...
Страница 10: ...FoamLogix Model 2 1A and 1 7AHP Class A Electronic Foam Proportioning Systems 10...
Страница 14: ...FoamLogix Model 2 1A and 1 7AHP Class A Electronic Foam Proportioning Systems 14 NOTES...
Страница 25: ...FoamLogix Model 2 1A and 1 7AHP Class A Electronic Foam Proportioning Systems 25 p n 038 1570 08 0...
Страница 28: ...FoamLogix Model 2 1A and 1 7AHP Class A Electronic Foam Proportioning Systems 28 NOTES...
Страница 47: ...FoamLogix Model 2 1A and 1 7AHP Class A Electronic Foam Proportioning Systems 47 Figure 22 Extra Cable Storage...
Страница 52: ...FoamLogix Model 2 1A and 1 7AHP Class A Electronic Foam Proportioning Systems 52 NOTES...
Страница 68: ...FoamLogix Model 2 1A and 1 7AHP Class A Electronic Foam Proportioning Systems 68 NOTES...
Страница 79: ...NOTES FoamLogix Model 2 1A and 1 7AHP Class A Electronic Foam Proportioning Systems 77...