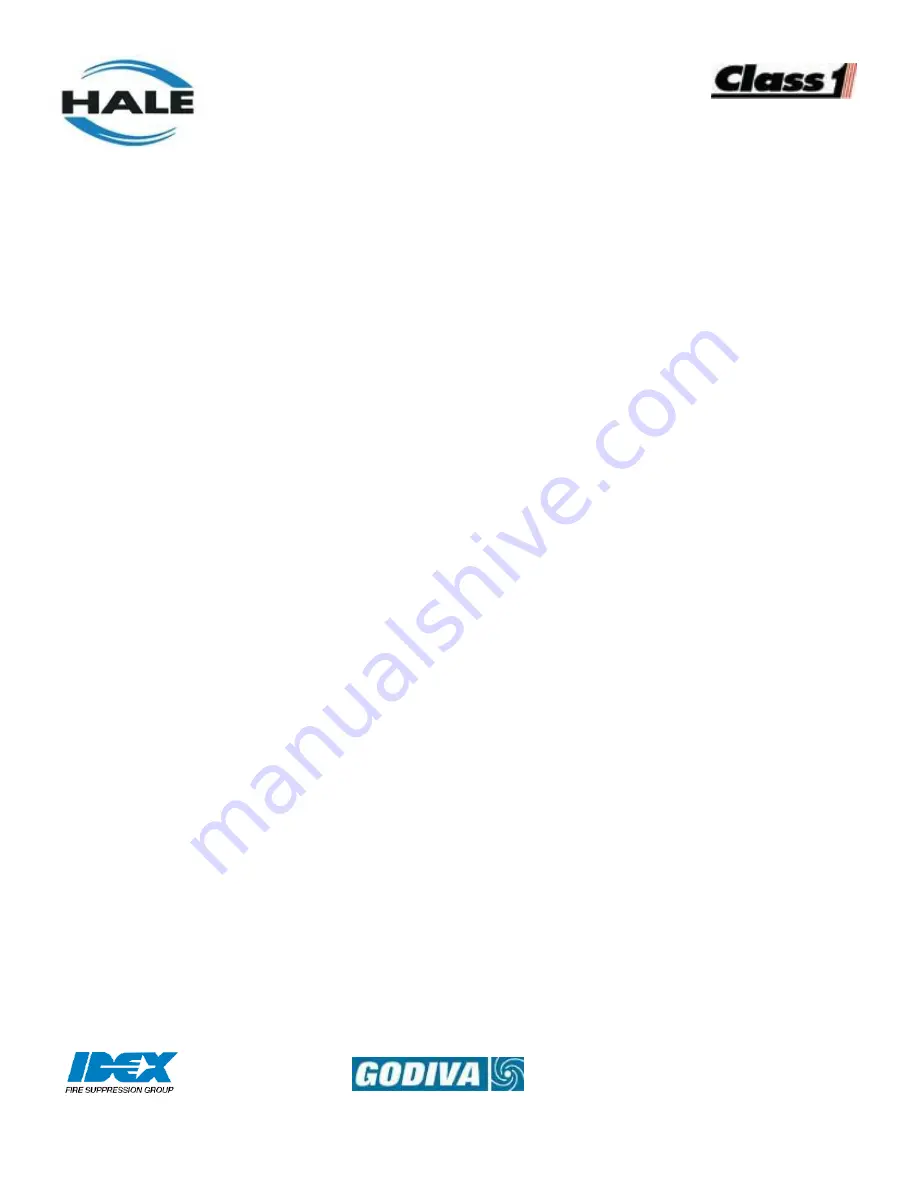
FoamLogix
TM
Model 2.1A and 1.7AHP Class “A”
Electronic Foam Proportioning Systems
Description, Installation and
Operation Manual
HALE PRODUCTS, INC / CLASS 1
607 NW 27th Avenue
●
Ocala, FL 34475
U.S.A. Telephone: 352-629-5020
FAX: 800-533-3569
GODIVA LTD.
Charles Street
●
Warwick, England CV34
5LR Phone: 44-1-926-623600
5LR Phone: 44-1-926-623600
IDEX DINGLEE TECHNOLOGY
(Tianjin) Co. Ltd.
No.9, 2nd Haitai Fazhan Road Huayuan Industrial Development Area (outside of ring road)
Tianjin High-Tech Industrial Park Tianjin China
Telephone: 011-86-22-8568-9800
FAX: 011-862285689808
Manual p/n: 029-0020-74-0-F
Содержание FoamLogix 1.7AHP
Страница 4: ...FoamLogix Model 2 1A and 1 7AHP Class A Electronic Foam Proportioning Systems 4 NOTES...
Страница 10: ...FoamLogix Model 2 1A and 1 7AHP Class A Electronic Foam Proportioning Systems 10...
Страница 14: ...FoamLogix Model 2 1A and 1 7AHP Class A Electronic Foam Proportioning Systems 14 NOTES...
Страница 25: ...FoamLogix Model 2 1A and 1 7AHP Class A Electronic Foam Proportioning Systems 25 p n 038 1570 08 0...
Страница 28: ...FoamLogix Model 2 1A and 1 7AHP Class A Electronic Foam Proportioning Systems 28 NOTES...
Страница 47: ...FoamLogix Model 2 1A and 1 7AHP Class A Electronic Foam Proportioning Systems 47 Figure 22 Extra Cable Storage...
Страница 52: ...FoamLogix Model 2 1A and 1 7AHP Class A Electronic Foam Proportioning Systems 52 NOTES...
Страница 68: ...FoamLogix Model 2 1A and 1 7AHP Class A Electronic Foam Proportioning Systems 68 NOTES...
Страница 79: ...NOTES FoamLogix Model 2 1A and 1 7AHP Class A Electronic Foam Proportioning Systems 77...