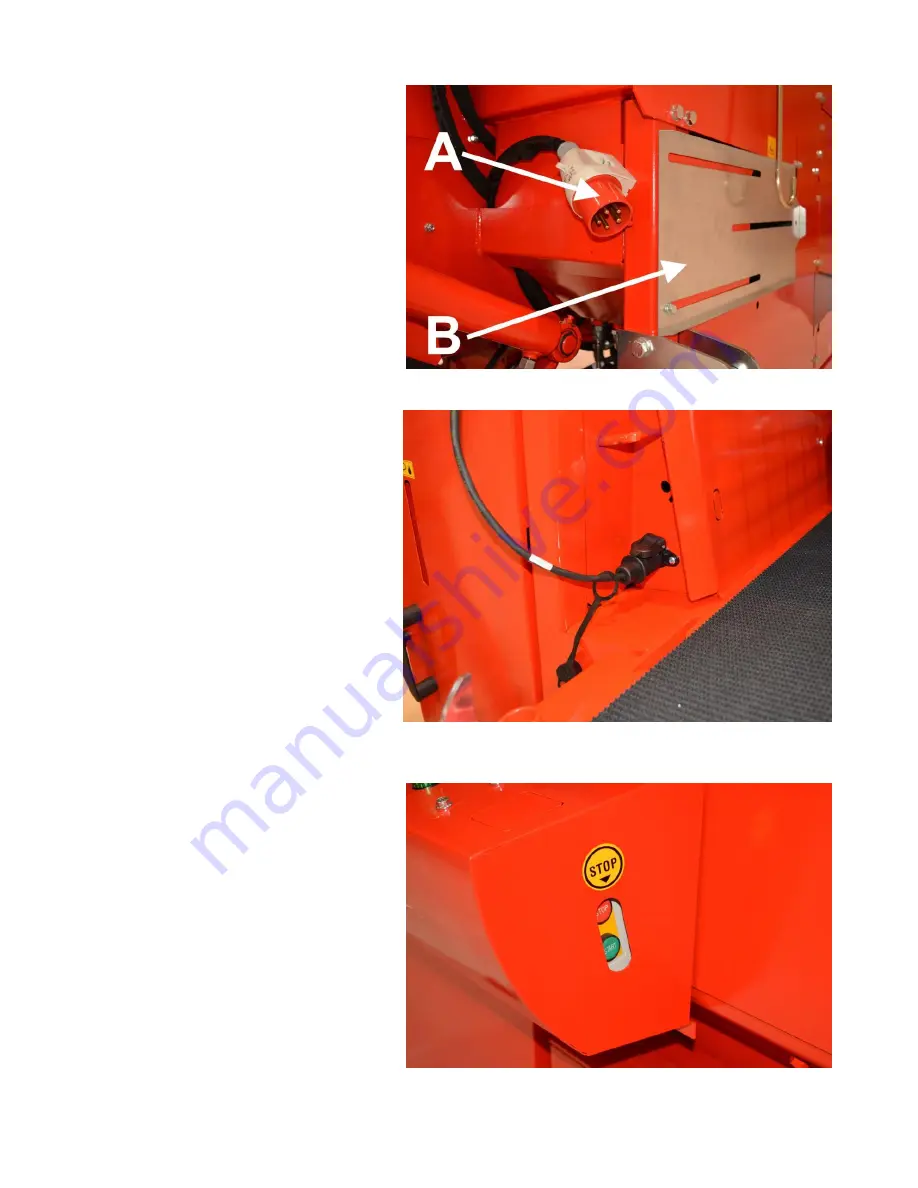
17 / 48
Hakki Pilke 43 Pro
Translation
Version 6-2018
3.2.2.
Electrical drive
An electrically powered machine
is driven by a 15 kW electric
motor. The IP rating of the
electric motor is 55. The fuse
must be at least a 32 A type C
fuse. The electrical cable must be
at least 5 x 6 mm², and the
recommended maximum length
is 25 metres. In order to connect
the cable, move protective cover
B of socket A and the angle gear
and secure it into a position
where it covers the angle gear.
In
an
electrically
powered
machine, the power cable for the
electric controls is connected to
the 3-pin socket on the side of
the machine.
The electrically powered machine
is turned on with the green
button of the remote starter,
located in the control panel in
the front of the machine (Figure
15). The actual starter is located
below the machine’s control
panel. The starter features an
automatic fuse and a thermal
relay for the electric motor. The
thermal relay can be reset by
pressing the red stop button on
the starter.
If the electric motor rotates in
the wrong direction (i.e. the
machine makes an abnormal
noise and the hydraulic functions
are inoperable), the current
phase
is
incorrect.
We
recommend using an extension
cord that allows you to switch
the current phase, or an adapter.
Note! If the extension cord does
not have a phase switch, the
electrical
work
related
to
changing the phase must only be
performed by an electrician.
Figure 13. The machine’s electrical drive
Figure 14. Electrical connector of the electric control device
Figure 15. The machine’s remote starter