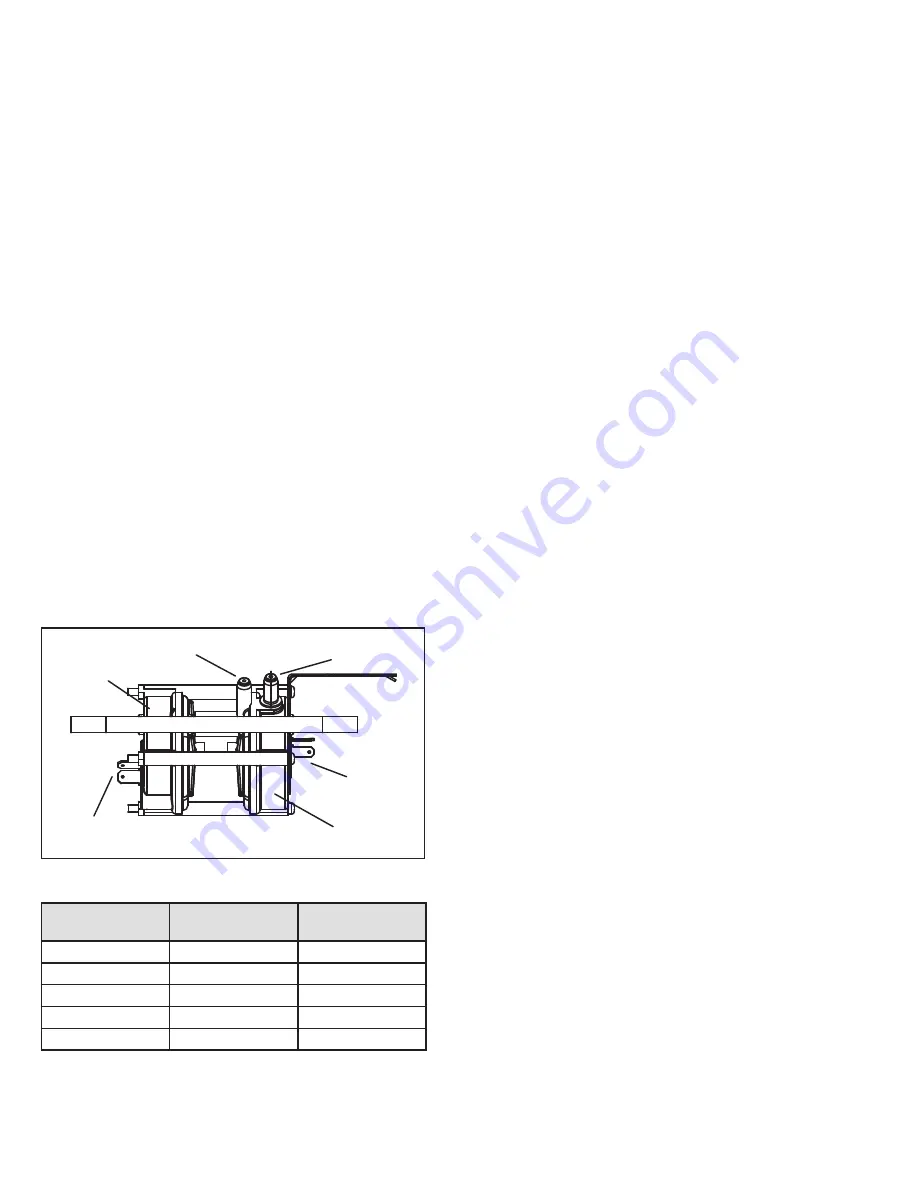
Page 16
31-5000726 Rev. 0
Combustion Air Inducer Pressure Switch (S18)
NF96UV series units are equipped with a dual combustion
air pressure switch (first and second stage) located on the
combustion air inducer orifice bracket. See Figure 11. The
switch is connected to the combustion air inducer housing
by means of a flexible silicone hose. It monitors negative
air pressure in the combustion air inducer housing.
The switches are a single-pole single-throw proving
switch electrically connected to the integrated control.
The purpose of the switch is to prevent burner operation
if the combustion air inducer is not operating or if the flue
becomes obstructed. On heat demand (first or second
stage) the switch senses that the combustion air inducer is
operating. It closes a circuit to the integrated control when
pressure inside the combustion air inducer decreases to a
certain set point.
Set points vary depending on unit size. See Table 6.
The pressure sensed by the switch is negative relative
to atmospheric pressure. If the flue becomes obstructed
during operation, the switch senses a loss of negative
pressure (pressure becomes more equal with atmospheric
pressure) and opens the circuit to the furnace control and
gas valve. A bleed port on the switch allows relatively
dry air in the vestibule to purge switch tubing, to prevent
condensate build up.
NOTE:
The switch is factory set and is not field adjustable.
It is a safety shut-down control in the furnace and must
not be by-passed for any reason. If switch is closed or
bypassed, the control will not initiate ignition at start up.
Figure 11. Combustion Air Pressure Switch
3/16 Terminals
Low Fire Switch
High Fire Switch
1/4" Terminals
Tap (negative - )
Tap (po)
Unit
Set Point
Low Heat
Set Point
High Heat
-045
0.40
0.70
-070
0.50
0.85
-090
0.50
0.85
-110
0.50
0.90
-135
0.45
0.90
Table 6.
Pressure Switch Setting 0 - 4500’
Pressure Switch Check
To check pressure switch differential, refer to Figure 12
and use the provided fittings and tubing to follow the steps
below.
1.
Remove thermostat demand and allow unit to cycle
off.
2.
Remove the tubing from the negative side (red and
black or red) and positive side (black) of the pressure
switch (leave both connected to cold end header box).
3.
Take the 2” length square tubing and connect to the
positive (+) side of the pressure switch. Take the 10”
length square tubing and tee into the tubing from the
positive side of the cold end header box and the other
side of the 2” square tubing. Connect the other end of
the 10” square tubing the the positive (+) side of the
measuring device.
4.
Take a second piece the 2” length square tubing and
connect to the negative (-) side of the pressure switch.
Take a second piece of 10” length square tubing and
tee into the tubing from the negative (-) side of the cold
end header box and the other side of the 2” square
tubing. Connect the other end of the 10” square tubing
the the negative (-) side of the measuring device.
5.
Operate unit and observe manometer reading.
Readings will change as heat exchanger warms.
a. Take one reading immediately after start-up.
b. Take a second reading after unit has reached
steady state (approximately 5 minutes). This
will be the pressure differential. The pressure
differential should be at least 0.15” greater than
those listed in Table 6. Readings in table are the
set points or “break points”.
6.
Remove thermostat demand and allow to cycle off.
7.
Replace original pressure switch tubing.
NOTE:
Pressure differential values (set point) in table are
the ”break”, or ”open” specifications. ”Make”, or ”close”
pressure differentials are 0.15” greater than the set points
listed in table.