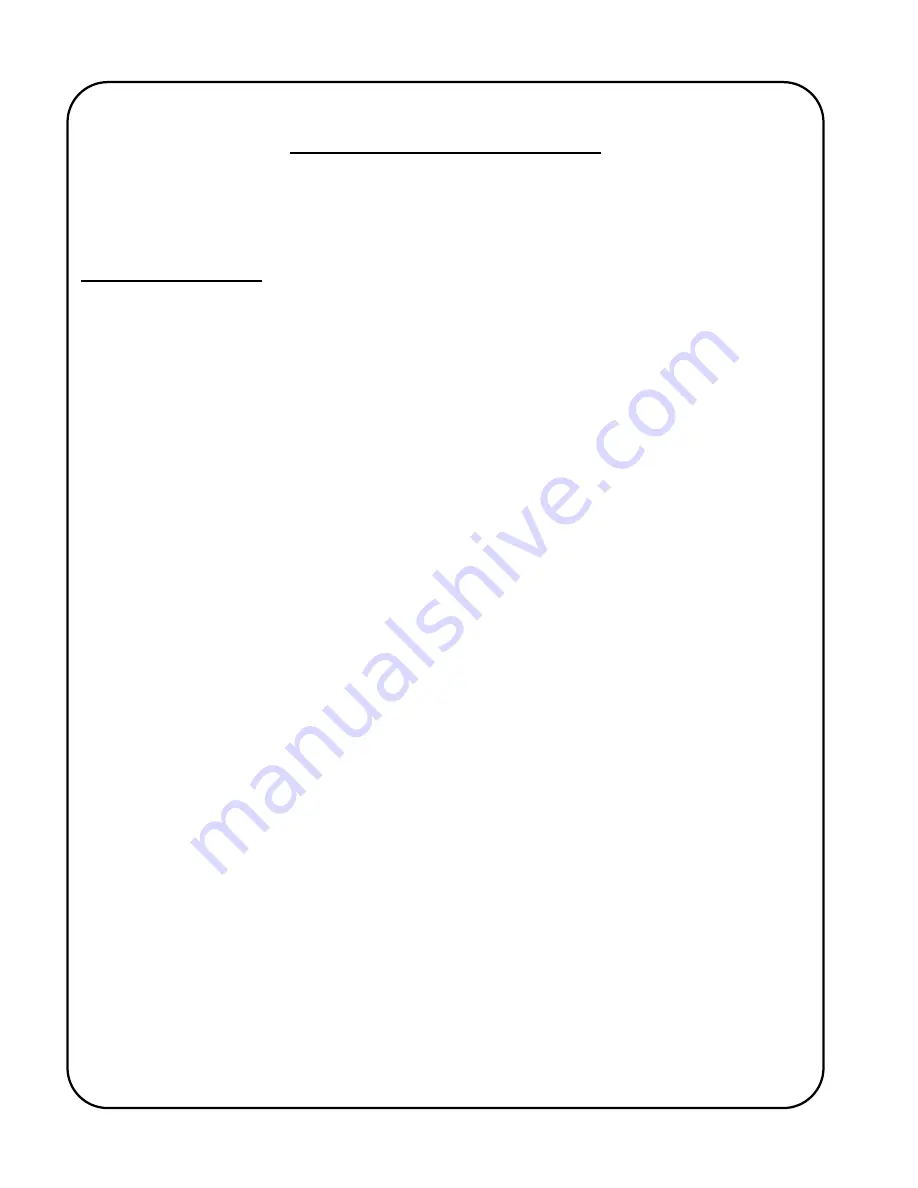
32
INSPECTION & MAINTENANCE
The Gullco KBM
®
-18 Portable Plate Edge Bevelling Machine is a heavy duty, robust piece of
equipment and under normal conditions, it will provide years of trouble free service if it is operated
within the limits of its expected use and if the following inspection and maintenance points are
adhered to.
DAILY INSPECTIONS
Check for smooth and free movement of the Main and secondary Support Rollers.
IMPORTANT: The Main Roller should always run free. Cutting chips, dust, dirt etc. can
restrict the free movement of the Main Roller, which, in turn creates feeding
drag. This will result in undesirable stress and will likely damage the
feed/guidance components and possibly the cutter and drive line components.
To avoid this problem, check that the Main Roller runs smoothly before each
use. If necessary clean or replace the bearing and roller. It is also
recommended that the Main Roller be demagnetized on a regular basis. This
will help reduce the build up of cutting chips etc. from around the roller.
Check the security of the Cutter Nut; the Slide Base Clamping Bolt; and the nut of the Angle
Alignment Bolt.
IMPORTANT: The Slide Base Clamping Bolt must be tightened firmly. If it is loose during
use, damage to Pivot Arm Assembly components, and possibly cutter and
drive-line components, will result.
IMPORTANT: Ensure that no contamination has been trapped behind the Slide Base before
retightening. It is essential that the clearance between the Slide Base and the
Pivot Arm Block be zero. If even a slight clearance is present, due to chips
etc., it could result in significant damage to Pivot Arm Assembly components,
and possibly cutter and drive-line components.
NOTE:
In order to clean contamination from behind the Slide Base, the Support Roller
Assembly, the Main Roller Assembly and the Slide Base Assembly must first
be removed.
Check for smooth and free movement of the Clamp Rollers. Inspect the condition of the clamp
roller wheels. Replace the pins and roller wheels if play is present, or if there is any damage.
Check the condition of the cutter.
Check the set-up of the machine for conformity to that described earlier in this manual.
Check that the Guide Rollers are adjusted correctly.
IMPORTANT: The Guide Rollers must be adjusted so that the plate being fed into the
machine contacts the Guide Rollers prior to contacting the face of the Guide
Roller Bracket, however, the Guide Rollers must not be too far out to
significantly twist the plate as it is being bevelled (resulting in component
damage). For straight edged plate the Guide Rollers should be in front of the
face of the Guide Roller Bracket by approximately 0.02” [0.5 mm]. Curved
Содержание KBM-18
Страница 2: ......
Страница 8: ...4 KBM 18 080 UNDERCARRIAGE ...
Страница 23: ...19 22 5º 30º 22 5º BEVEL ARRANGEMENT 30º BEVEL ARRANGEMENT ...
Страница 24: ...20 37 5º 45º 37 5º BEVEL ARRANGEMENT 45º BEVEL ARRANGEMENT ...
Страница 25: ...21 55º 55º BEVEL ARRANGEMENT ROOT FACE SCALE EXAMPLES ...
Страница 42: ...38 KBM 18 100 GENERAL ASSEMBLY BREAKDOWN Drawing Number KBM 18 100 ...
Страница 43: ...39 KBM 18 100 GENERAL ASSEMBLY BREAKDOWN Drawing Number KBM 18 100 ...
Страница 45: ...41 PIVOT ARM ASSEMBLY BREAKDOWN Part Number KBM 18 213 ...
Страница 46: ...42 SLIDE BASE ASSEMBLY BREAKDOWN Part Number KBM 18 212 ...
Страница 49: ...45 STARTER ASSEMBLY BREAKDOWN Drawing Number KBM 18 214 ...
Страница 50: ...46 MANUAL STARTER ASSEMBLY BREAKDOWN Drawing Number KBM 18 215 1 2 3 ...
Страница 54: ...50 OPTIONAL HYDRAULIC UNDERCARRIAGE ASSEMBLY BREAKDOWN Part Number KBM 18 080 ...
Страница 55: ...51 OPTIONAL HYDRAULIC UNDERCARRIAGE ASSEMBLY BREAKDOWN Part Number KBM 18 080 ...
Страница 56: ...52 OPTIONAL UNDERCARRIAGE ASSEMBLY BREAKDOWN Part Number KBM 18 069 ...
Страница 57: ...53 KBM 18 WIRING SCHEMATIC Drawing Number KBM 18 215 SCH ...
Страница 60: ...www GULLCO com ...